A 54" tunnel fan with a 1.5-hp motor is running and consuming 1,700 watts of power. The belt suddenly breaks and the fan blades stop rotating, but the motor continues to spin. How much power do you believe the motor is now consuming? 1,700 watts? It is important to understand that the primary factor determining how much power a fan will use is how fast the motor is spinning the prop. The faster the prop spins, the greater the amount of work required, and the greater the amount of power used by the motor. So, as a result, when the belt breaks, the amount of work required of the motor decreases dramatically, as does its power usage, to around 200 watts.
What might surprise you even more is that motor size and/or whether the motor is single-phase or three-phase has little effect on fan power usage. This is because it’s not the size of a motor that determines how much power it will use, but rather how much work is required of the motor. Though it is true that a 2-hp motor is capable of doing more work than a 1-hp motor, if spinning a fan prop only requires 1 hp worth of work a 2-hp motor will use essentially the same amount of power as a 1-hp motor.
To demonstrate this fan principle, the performance of a fairly typical 54" tunnel fan was evaluated in a fan test chamber* with three different motors using the same size prop pulley (AK104 - 10.4" diameter) and motor pulley (AK34 - 3.4" diameter):--- 1.5 hp 240 V single-phase motor (standard) 2 hp 240 V single-phase motor 1.5 hp three-phase motor with an integrated phase converter (single to three-phase).
The fan test chamber allowed the precise determination of both the fan's power usage and air moving capacity at a wide range of operating static pressures (0 - 0.30").
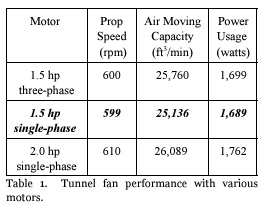
Table 1. shows the performance of the 54" fan, operating at a static pressure of 0.10", with the three different motors. Since all three motors were designed to operate at a fixed speed (1,750 rpm), and the motor and prop pulleys were the same, there was less than a 2% difference in prop speed between the three motors. The air-moving capacity of the fan varied a few percent between the three motors which could have been due to slight differences in fan prop speed and/or slight variations of measurements taken in the fan test chamber. The power usage was slightly higher, 4%, for the 2-hp motor which is likely attributed to its efficiency being lower than the other two motors (81% vs 84% and 86%). Though there were technically differences in fan performance between the three motors, they were so small it is doubtful that if the fans were installed on a farm in three identical houses that there would be any notable difference in the air speed produced by the fans or power usage among the three houses.
In contrast, varying the size of the motor pulley, which changes the speed at which a fan prop rotates, can have a dramatic effect on both the air-moving capacity and power usage of a fan. Three different pulleys were installed on the same 54" tunnel fan with a 240 V single-phase motor and fan performance was again evaluated (Figure 1):
- AK34 (standard)
- AK30 (smaller diameter-reduced prop speed)
- AK39 (larger diameter-increased prop speed)
Reducing the motor pulley diameter by 0.4" (AK34 vs AK30) reduced fan prop speed and air-moving capacity by about 10% (Table 2). In contrast, increasing the motor pulley diameter by approximately 0.5" increased the speed of the fan and speed and airmoving capacity by approximately 10%. These results were not unexpected because well-established fan laws dictate a linear relationship between fan speed and the air moving capacity of the fan (10, 20, 30% more speed = 10, 20, 30% more cfm). It is important to note that the pulleys could have been changed on the other motors tested as well and the results would have remained essentially the same.
What many people don’t realize is that simply changing the motor pulley can have a dramatic effect on fan power usage and current. This is because of the exponential relationship between prop speed and the work required of a fan motor. Namely, small changes in prop speed can result in very large changes in the work required and therefore the power used by a fan. With the same 1.5-hp motor used in the first test, increasing the pulley size from AK34 to AK39 only increased the air-moving capacity of the fan by 10%, while power usage and current increased by more than 22%. Now, if the motor was not designed to handle this dramatic increase in current and power usage, the motor would overheat and, in time, fail. For this reason, it is very important when replacing a motor, to install the same size pulley that was on it previously. If you are unsure of the correct motor pulley size you can check with the fan manufacturer.
Installing the smaller motor pulley and reducing the prop speed/air-moving capacity of the fan by 10% resulted in nearly a 25% reduction in fan motor power usage and current This is the principle driving the increasing use of variable speed tunnel fans to reduce poultry house power usage. The objective is to reduce overall power usage by using more fans operating at a lower speed instead of operating fewer fans at full speed.
It is important to always keep in mind that fan power usage is primarily determined by the work required to spin the prop at a given speed and not by the size or type of motor. Though installing a slightly larger fan motor pulley will increase the air-moving capacity of the fan, it can result in overloading the motor, resulting in dramatically increased power usage and reduced motor life. Conversely, it is possible to potentially increase fan motor life without increasing fan power usage by installing a larger motor, and since it isn’t fully loaded, it will tend to operate at a lower temperature and therefore last longer.
This article was originally published in Poultry Housing Tips, Volume 36, Number 8, 2024. University of Georgia, College of Agricultural and Environmental Sciences Cooperative Extension (https://www.poultryventilation.com/).