The house has been preheated for 36 hours to 92°F. The chicks will be arriving in a few hours and the controller’s six temperature sensors (positioned one foot above the floor) indicate the air temperature is between 91 and 92°F (Figure 2). A thermal image indicates the floor temperature is between 87 and 102°F (Figure 1) There is no measurable ammonia due to the fact that litter treatment that was applied three days prior and the litter is dry. Feeders as well as supplemental feeders are full of feed and the water lines set to the proper height. Minimum ventilation fans are operating 30 seconds out of five minutes and the humidity is approximately 60%. Everything appears to set for getting the chicks off to a good start.
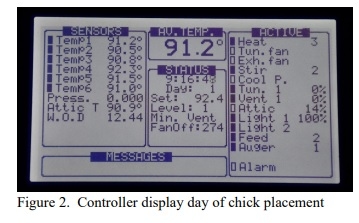
But, this farm is a little different from most. First, the farm manager does not use partial-house brooding, and more importantly the heating systems installed on each end of the house are different. On one end, 12 radiant brooders are installed and on the other, three forced air furnaces. Both types of heating systems can, and have been, successfully used for decades to provide the supplemental heat during brooding, but that being said, they heat a house very differently. Nothing makes this point more clearly than when the thermal image of the end equipped with forced air furnaces (Figure 3) is compared to the end heated by the radiant brooders (Figure 1).
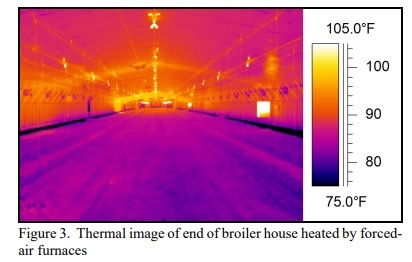
The controller indicated that the air temperature on each end of the house was essentially identical, but thermal images tell a different story. Although the floor temperature on the radiant brooder end was between 87°F and 102°F, the floor temperature on the end heated with forced-air furnaces was between 78°F and 87°F... roughly 10°F cooler. Figure 4 is a histogram floor temperatures on each end of the house. On the end of the house with furnaces 72%, of the floor area was between 81°F and 84°F. On the end with radiant brooders, 85% of the floor was between 90°F and 96°F. Though air temperature is obviously important to a day-old-chick, floor temperature is just as important, if not more important, to chick thermal comfort, considering they will be sitting on the floor and the cooler it is the more heat they will potentially lose to the floor. When the farm manager was shown the thermal images, he was surprised by the difference and immediately adjusted controller settings to increase the temperature on the end the house with forced-air furnaces (lowered the calibration of the controller sensors on the nonbrooding three degrees).
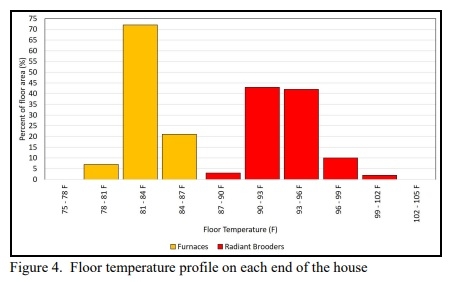
Figures 5 and 6 were taken 24 hours after the chicks were placed. The adjustments to forced-air furnaces’ controller temperature settings helped to increase floor temperatures from those seen 24 hours earlier. An analysis of the thermal images indicated that on average the floor temperatures on the furnace end were only 3°F cooler than those on the radiant brooder end of the house (Figure 9). Interestingly, though the differences in floor temperatures between the two ends of the house were relatively minimal, the chicks on the end of the house with forced-air furnaces appeared much cooler than those on the end of the house equipped with radiant brooders (Figures 5 and 6). The chicks were huddling near the feed lines and the level of activity was noticeable lower (Figures 7 and 8).
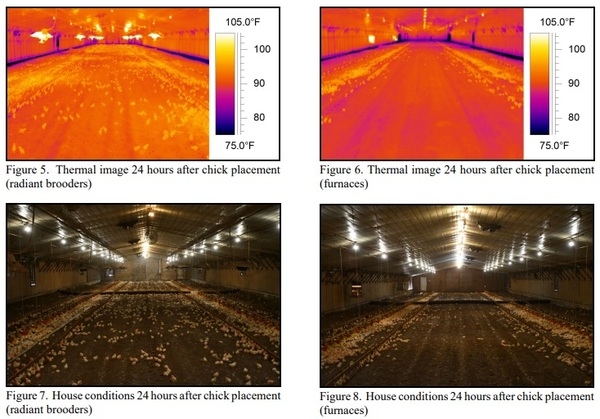
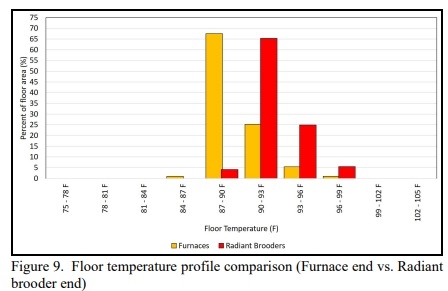
This house provided a good example of a few very important points when it comes to brooding chicks. First, young chicks have a fairly narrow band of temperatures they find acceptable. Secondly, optimal target temperature during brooding will vary with the type of heating system used. Last but not least, there isn’t a single optimal brooding temperature that will work for all chicks under all situations.
The ability of chicks to regulate their body temperature is limited during the first few days of life. Whereas with market-age birds house temperature can easily drop ten or more degrees below the target without adversely affecting the bird’s body temperature, a chick’s body temperature can decrease with house temperature changes of five degrees or less. In a way, a young chick is more like a reptile than a bird. House temperature decreases a few degrees and their body temperature will decrease in response. To maintain their body temperature when the house is lower than the chicks desire, they will huddle, which reduces their surface area exposed to cooler house temperatures. Though the huddling will help a chick to maintain its body temperature, the more time it spends huddling the less time it will spend eating and bird performance as well as health will suffer.
Forced-air furnaces are very tricky to manage with young birds for a number of reasons. First, furnaces tend to do a very good job of heating the ceiling and not good job of heating the floor due to the simple fact that the hot air produced by furnaces quickly rises to the ceiling. This results in the ceiling temperatures often being 10 to 20°F higher than they are at floor level. Furthermore, floor temperatures will always be lower than the temperature of the air next to floor. How much lower depends on factors such as house tightness, the use of circulation fans, furnace spacing, and preheat time. The net result is that floor temperature, which in many ways more important than house temperature to a young chick, will often be two to ten degrees lower than the air temperature a controller’s sensors, positioned a foot or two above the floor, are indicating. Secondly, since forced-air furnaces tend to produce fairly uniform floor temperatures, a chick has a limited ability to self regulate its body temperature by moving to a warmer or cooler area of the house. It is important to keep in mind that the house temperature a chick wants will change based on a variety of factors such as chick size, humidity, air movement, house tightness, litter moisture, and even time of day. Add to this the fact that all chicks may not want/need the same house temperature. Variations in chicks size, breeder flock age, etc. can affect the house/floor temperature a chick will seek. Since the chicks have a limited ability to self regulate their thermal environment in houses with forced-air furnaces, it is the farm manager’s responsibility to closely watch chick behavior and make adjustments to house environmental controller settings accordingly, possibly multiple times a day.
The primary advantage of radiant brooders over forced-air furnaces is that a portion of the heat produced is delivered directly into the litter. The radiant heat produced by the brooder will cause the floor temperature in the vicinity of the brooder to be warmed above house air temperature. How much the floor is warmed above air temperature is primarily a function of distance from a radiant brooder. It can be as little as a degree or two eight to ten feet from the brooder to as much as 30 degrees directly below a brooder. Regardless, there is a range of floor temperatures for chicks to chose from to meet their individual needs. As a result, if the house air temperature is not optimal, the chicks have the ability to self regulate by moving closer or farther away from a brooder. In houses with forced air-furnaces, if the temperature is lower than the chicks desire, the only option is to stay huddled with other chicks for warmth. As mentioned previously, the greater the amount of time a chick spends huddling, the less feed it will consume, and the more likely performance as well as bird health will suffer.
When comparing Figures 7 and 8, it is clear that optimal set temperatures for young chicks will vary with the type of heating system used. Though air temperature on both ends of the house was essentially identical, the chicks level of thermal comfort was not. Generally, higher set temperatures have to be used with forced-air furnaces than with radiant brooders because floor temperatures will tend to be lower than air temperature. Most farm managers have found through experimentation that with forced-air furnaces house temperatures often need to be set 3 to 5°F higher than those heated with some type of radiant heaters. This of course will vary with sensor height, houses tightness, use of circulation fans, etc.
It is important to recognize that controller set temperatures may also need to be adjusted for different types of radiant heating systems. The more floor area covered with radiant heat, the lower the set temperature can be without adversely affecting chick comfort. Therefore, the larger the number and/or size of radiant heaters, the more floor area covered with radiant heat, and the more forgiving the birds will be if house temperature is not optimal.
The lesson to be learned is poultry house controllers, no matter how advanced, are only designed to control house air temperature...not bird thermal comfort. Any brooding target temperature provided by a poultry company, primary breeder, equipment company, or university is at best a starting point. Nothing will ever replace the importance of simply going into a house at least a few times a day, and taking a few moments to simply watch the chicks. In the end, how well the chicks are spread out across a house, their level of activity, the sounds they are making, are more important in determining if they comfortable than the display screen on a house’s environmental controller.
This article was originally published in Poultry Housing Tips, Volume 32, Number 2, 2020. University of Georgia, College of Agricultural and Environmental Sciences Cooperative Extension (https://www.poultryventilation.com/).