Sustainable solutions for hygienic feed production are increasingly important as the antibiotic-free/no antibiotics ever (ABF/NAE) trend becomes stronger and more widespread. Once only considered in the most mature and advanced markets, today ABF production is a regular discussion point in all regions and will eventually become a reality for smaller and developing markets.
Evolution of the market – consumer and industry
ABF production places ever-increasing pressure on the animal protein industry and has ushered in a new era of best practices and trends. The industry continues to evolve to meet the needs of a more demanding and sophisticated consumer base. Consumer preferences for “clean” and more humane production practices have cascaded from farm-to-table, white linen restaurants to mainstream fast food establishments further driving meat producers to meet these requirements. Furthermore, globalization of the industry has resulted in two additional phenomena: 1) a global market has forged a regulatory network and knowledge base that is much more informed and discerning than ever before, and 2) consolidation of businesses at the local and multinational level has introduced additional requirements to support a global business that is both compliant and profitable.
Solutions for reducing pathogens – direct and indirect approaches
In the absence of antibiotics, growth promoters, hormones etc., addressing feed-borne challenges such as Salmonella, C. perfringens and E. coli have become a significant focus to ensure fock and herd health. The presence of pathogens in feed has a downstream and often adverse effect on the health, physiology and performance of the animal. In ABF production these challenges can be addressed indirectly by modulating factors related to gut health, status of the immune system, and nutrition. Newer and more sophisticated technologies hold significant promise but are still in the beginning days of regulatory clearance. Feed hygiene can also be improved directly through the pre-pellet application of additives including acids, antioxidants, etc. An alternative approach to lower microbial load in finished feed is simply more rigorous feed processing methods – increasing temperature, pressure and duration of conditioning times. Conditioning temperatures above 90°C, double conditioning, and expansion/extrusion are more and more common – the latter often incorporate temperatures > 120°C. One downside to extreme processing conditions is the resulting loss of activity in additives like enzymes and vitamins, resulting in reduced efficacy or even complete loss of their benefits altogether.
Benefits of post-pellet liquid application– PDI and enzyme recovery
In addition to the benefit of improved feed conversion ratio, post-pellet liquid application (PPLA) has been leveraged to add other ingredients in order to circumvent the harsh processes using high temperatures and long conditioning times. While special thermostable coatings have been successfully used to protect enzymes and other additives, these technologies can work against the goals of the producer by adding cost and impairing bioavailability. There is limited research on the use of PPLA for simultaneous delivery of fat and other liquid additives such as enzymes.
Researchers at Novus International, Inc. explored the addition of enzymes and fat via PPLA to see the potential impact on feed quality and enzyme activity. Three different diet treatments were prepared to equivalent final fat content but varied in the amount of fat delivered in the mixer or via post-pellet (Table 1). For all three diets, the liquid phytase (CIBENZA PHYTAVERSE) was sprayed @500 u/kg diet post-pellet after fat was applied using PPLA system. The common basal diet for all three diets was formulated to meet industry specifications with calculated fat levels of 6.84% (including 4.5% supplemental fat).
This data indicates that reducing the fat added in the mixer and instead adding fat using a fat coater post-pellet helped to achieve significant reduction in % fines and an increase in pellet durability. Beyond this, no significant change in enzyme activity was seen (Table 2) (Manangi et al. 2019).
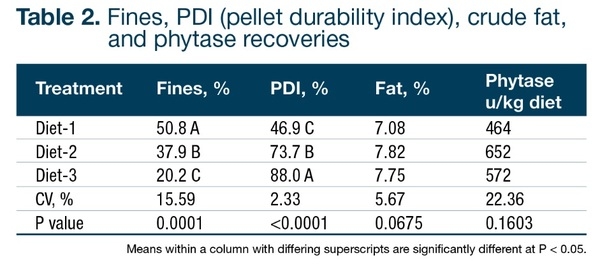
According to research, mixer-added fat (MAF) inherently reduces pellet quality. The hydrophobic nature of fat is likely to create interference of feed particle binding (Loar and Corzo, 2011) and the pellet durability index (PDI) is further reduced when using high levels of MAF due to a decrease in pelleting pressures caused by additional lubrication in the pellet die. Pellet durability as related to fines have been well-documented to have a direct impact on feed conversion deficiencies in animals (Wondra et al., 1995). By delivering some portion of the final fat content post-pellet can reduce fines and increase pellet durability as well as overall efficiency in feed production at the mill (Muramatsu et al., 2015). Improving these factors results in higher overall efficiency and lower costs for feed manufacturing and protein production.
Status of the technology
PPLA systems of the past were prohibitively expensive and required extensive support in the field, making the technology inaccessible to all but the largest, well-resourced productions. Less expensive solutions were available but were prone to failure and lacked the accuracy needed for reliable day-to-day operations. Recently however the industry has seen great advances in bringing more sophisticated and reliable PPLA technologies to the market at very affordable prices. As a result, a shift is happening in the industry – smaller and less sophisticated operations are combining PPLA of fat with other liquid and water-miscible additives such as enzymes. This trend speaks to the importance and value brought by PPLA, and the expectation is to see a continuing increase use of this technology in the years to come.