1. INTRODUCTION
Mycotoxins, toxins produced by fungi on various food and feed products such as cereals and nuts, present a worldwide food and feed safety concern, which can lead to several health problems in humans and animals, as well as major economic losses for farmers, the industry, and society (Marin, Ramos, Cano-Sancho, & Sanchis, 2013). The Food and Agriculture Organization estimated that approximately one quarter of all cereal products worldwide are contaminated by mycotoxins (Boutrif & Canet, 1998). Furthermore, according to the Rapid Alert System for Food and Feed (RASFF), mycotoxins, in particular aflatoxins, are the main reason for European border rejections (Marin et al., 2013). The high percentage of contaminated batches and the high number of border rejections show that mycotoxins are common, especially in cereals and nuts. Mycotoxin presence in cereal commodities could lead to direct market losses (associated with lost trade or lost revenue due to batches that are downgraded or even destroyed), losses related to human health costs, and less productive animals (IARC, 2012).
Proper monitoring of batches throughout the cereal food supply chain reduces the probability that a contaminated product will be sold for feed or food production, and the consequences thereof, such as expensive recalls or, even worse, reduced animal or human health. Cereal batches are monitored by collecting and analyzing multiple samples from the batch. Since mycotoxins are heterogeneously distributed (Cheli, Campagnoli, Pinotti, Fusi, & Dell’Orto, 2009), samples collected at different locations in a cereal batch are expected to have different mycotoxin concentrations. Therefore, collecting multiple samples to estimate the mycotoxin concentration in the batch is essential for a true estimate of the batch concentration. When more samples are collected, the sampling plan becomes more accurate (Johansson, Whitaker, Giesbrecht, Hagler, & Young, 2000a).
For official monitoring, regulations describe the minimum number of samples to collect (e.g., Regulation [European Union] Number 691/2013 defines the sampling and analysis methods for feed products; EU, 2013). In the case of a private company, the number of samples required for routine checks, customer demands, or certification systems depends on the private system in place, and/or the available budget. Companies often want to limit their budgets for mycotoxin monitoring in cereals and do not have to follow the sampling requirements stated in the regulations accurately. For companies, the choice between monitoring frequency and costs is often difficult: the optimal monitoring plan for a private company is a cost-effective monitoring plan. This, in turn, is a plan that results in a low probability of contamination of the end product, without extremely high sampling and analysis costs.
A few earlier studies have used optimization modeling to optimize monitoring plans for various types of hazards in food and feed products (Ferrier & Buzby, 2013; Lascano-Alcoser et al., 2014; LascanoAlcoser, Velthuis, van der Fels-Klerx, Hoogenboom, & Oude Lansink, 2013; St-Pierre & Cobanov, 2007). In this study, a single-objective constrained optimization problem, solved by linear approximation, was applied to the case of mycotoxin monitoring along the cereal chain. The objective is cost minimization, and the main constraint is an end-of-chain contamination level below the predetermined limit. To monitor mycotoxins along the cereal chain, from the fields to the end product, samples can be collected at different control points (CPs; e.g., field, storage silo, trucks, processing plant, end product). This study provides insight into the most critical CPs and the number of samples required to fulfil the concentration criterion at the end of the chain. We assumed that there was one budget available for monitoring the entire maize chain, for example, that one big company was responsible for the entire chain. This article focuses in particular on AFB1 in the maize chain. AFB1 is of great interest, since it is the most toxic mycotoxin, is heterogeneously distributed throughout the batch, and can be formed on the field as well as during transport and storage in case of improper conditions.
2. METHODS
2.1. The Maize Chain
The optimization model was based on a representative but simplified Dutch maize chain, in which maize grown in South East Europe was transported by ship to the Netherlands and processed into compound feed for dairy cows (Fig. 1). In this chain, 60,000 tons of maize was followed from the fields in South East Europe to the storage silos, through sea shipment, and finally to the barges en route to the processing plant in the Netherlands. The model assumed that, on average, a field has a 100 tons production capacity. Maize from 600 fields were assumed to be transported to 60 large storage silos, each with a 1,000 tons storage capacity (B1). The content of these storage silos was transferred to a 60,000 tons sea-going ship with six compartments of 10,000 tons each (B2 and B3). At the harbor, the maize was transferred to 30 smaller 2,000 tons barges (B4), destined for the processing plants, which are mostly situated along the rivers. All fields, silos, ships and ship compartments, and barges had the same capacity, and other possible (smaller) transport steps were not considered.
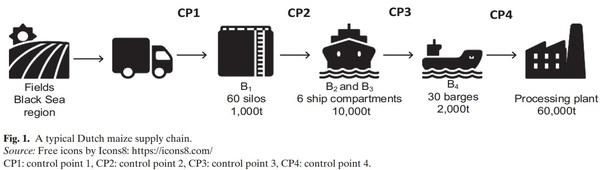

We assumed that the processing plants need a predefined amount of maize; therefore, if the AFB1 concentration of a batch exceeded the threshold and the batch was rejected, it had to be replaced. For the purpose of this study, a batch was defined as maize of the same origin and conditions: for example, a batch was the content of one silo or the content of one compartment in the ship. During mixing, the number of batches and their size varied along the supply chain.
2.2. The Control Points (CPi)
Four CPs to monitor for AFB1 were chosen, following current practices. The first control point (CP1) was set at the point where the storage silos were loaded after harvest; in case of contamination, the content of the silo was replaced. CP2 was set at the point where the sea-going ship was loaded; in case of contamination, the content of the cargo space was replaced. CP3 was set at the point where the ship was unloaded in the country of destination; since the tests results last a couple of days, in case of contamination, the barges with the content of the contaminated cargo spaces were replaced. The last control point, CP4, was set at the point where the barges were unloaded at the final destination; in case of contamination, the content of the barges was replaced. For simplicity, it was assumed that the same number of samples were collected from each silo, compartment, or barge.
2.3. Scenarios
We considered six scenarios, with the characteristics as shown in Table I. Two scenarios (S1, S2) started with a low in-field AFB1 concentration of 1 µg/kg, two scenarios (S3, S4) started with a higher (4 µg/kg) AFB1 concentration, and the two last scenarios (S5, S6) started with a very high (10 µg/kg) in-field AFB1 concentration. In some scenarios, the storage conditions during transport by ship were assumed to be suboptimal, that is, the water activity and temperature were not controlled well. During this period, the Aspergillus fungi could grow and produce AFB1. Based on the results of Abdel-Hadi, Schmidt-Heydt, Parra, Geisen, and Magan (2012), we assumed the following suboptimal conditions: a temperature between 25 °C and 30 °C and a water activity of 0, 95, and consequently an AFB1 production of 100 µg/kg in the sections of the ship compartments contaminated with the fungi (prod). AFB1 was only produced in hot-spots in ship compartments that were contaminated by the fungi and had high water activity and temperature. We assumed that these hot-spots comprised 5% of the total compartment volume.
2.4. Sampling and Analysis
Since we assumed that the processing plants required a fixed amount of maize, batches that exceeded the predefined maximum limit after sampling and analysis were replaced. The concentrations of the batches after sampling, analysis, and replacement (cmj) were based on the probability of accepting and rejecting a batch; cmj reflects the average concentration after monitoring of all batches at CPi. This is the average concentration of batches, in cases where the same batches were monitored an infinite number of times. This average was calculated as follows:
cmi = ci × PAi + m × (1 − PAi),
with ci being the average initial concentration of all batches at CPi before sampling and analysis; PAj the probability to accept this batch; m the mean AFB1 concentration of the replacing batch; and 1 − PAi the probability to reject a batch. If no samples were collected, PAi was equal to 1 and, therefore, the concentration after sampling and analysis remained the same as the initial concentration.
The probability to accept a batch is the probability that the measured batch concentration is below the predetermined limit, based on a lognormal distribution (Equation (2)).
with µi being the mean of distribution of test results at CPi; lim the predetermined limit in µg/kg; and ci the mean AFB1 concentration at CPi before sampling and analysis.
The test result followed a lognormal distribution with mean µi and variance σi 2, calculated with Equations (3) and (4), respectively:
with ci being the mean AFB1 concentration at CPi before sampling and analysis, and var(ci) the total variance of the sampling and analysis plan, which is a function of ci and the number of samples collected per batch (nsj) (Equation (5)):

This variance includes the variance due to sample collection (Johansson et al., 2000b), as well as the variance due to analysis. Variance due to sample preparation was in this case integrated in the variance due to analysis. We assumed that nsi 100 g samples were collected from each batch at CPi and combined into one aggregate sample, which was analyzed in a laboratory with an instrumental method such as liquid chromatography with tandem mass spectrometry (LC-MS/MS). A total uncertainty of 50% was associated with sample preparation and analysis. This was based on the measurement uncertainty for an LC-MS/MS-based multimycotoxin assay estimated by Stadler, Sulyok, Schuhmacher, Berthiller, and Krska (2018). The total variance of the sampling plan was based on the variance due to collecting multiple samples from the batch during unloading or loading of the silos, ships, or barges, as well as the analytical variance.
In this study, we assumed a predetermined limit of 2.5 µg/kg for AFB1 in maize intended for dairy cow feed and did not consider the measurement uncertainty when deciding to reject or accept the batch. The AFB1 limit for dairy-cattle feed listed in Directive 2002/32/EC is 5 µg/kg (EU, 2002).
2.5. Monitoring and Replacement Costs
The sample collection and LC-MS/MS analysis costs of a sample are €10 and €100, respectively, in the case where samples are aggregated for analysis. These analysis costs are quoted per analyzed batch, and are only accounted for when samples were collected from that batch. The costs at each CPi were calculated with Equation (6):
where ni represents the number of batches (silos, ship compartments, and barges) sampled and analyzed at CPi; nsi is the number of samples collected from the batch at CPi; ri represents the replacement costs for one batch at CPi; and PAi represents the probability that the batch will be accepted.
We assumed that the costs for sample collection and analysis were the same at each CP. Replacement costs at CP1 were considered to be an average FOB (Free on Board) export price expected for 2019 from the Black Sea region of €160/ton. At the subsequent CPs along the chain, recall and replacement costs increased, since the transport costs of the replaced batch had to be added. At CP2, we assumed that the batch was on its way to the country of destination, and an additional €20/ton was added as transport cost. At CP3 and CP4, an additional €10 was added at each CP as transport and transshipment costs. More details and cost references are shown in Table II.
2.6. The Optimization Model
An optimization model was constructed to minimize the total cost for monitoring and replacing the batches that exceeded the predetermined limit, with the constraint that the AFB1 concentration in the batch was below the predetermined limit at the end of the chain.
Min:
subject to
where ni is the number of batches (silos, ship compartments, or barges) sampled and analyzed at CPi; nsi is the number of samples collected from each batch, between 0 and 200, at CPi; rj reflects the replacement costs for one batch at CPi; PAi is the probability to accept the batch and keep it in the chain depending on ni and nsi; Bi is the number of batches at CPi; lim is the predetermined limit for AFB1; c1 is the average AFB1 concentration at CP1 before sampling and analysis; cmi is the average AFB1 concentration at CPi after monitoring and replacement; and m is the AFB1 concentration of the replacing batch. The parameters of the model can be found in Table III. The COBYLA algorithm from the R package “nloptr,” version 1.0.4—Constraint Optimization by Linear Approximation—was used to solve the problem.
3. RESULTS
Table IV shows the optimization results for each scenario (S1, S2, S3, S4, S5, and S6): the optimal CP, the optimal number of batches checked at this CP, the number of samples collected from each batch, the costs for monitoring and replacing, the concentration at the time of sampling, the probability of accepting the batches, the concentration at the end of the chain, and the volume-based percentage of maize replaced.
S1 had a low AFB1 concentration and no AFB1 production during transport, indicating that it was optimal not to collect any samples. S3 and S5 had high (4 µg/kg) or very high (10 µg/kg) AFB1 concentrations in the fields, and no production during transport. For these scenarios, it was optimal to collect samples early in the chain, after harvest and before transport, at CP1, since the replacement costs were the lowest, and the AFB1 concentration did not change after this CP. In S2, S4, and S6, there was AFB1 production during transport. For these scenarios, it was optimal to delay sample collection after transport at CP3, when unloading the sea-going ship.
The number of samples collected per batch depended on the concentration: A high concentration at the time of sampling, for example, 15 µg/kg for S6, required only a few samples for contamination detection: six samples per ship compartment, with a 9% probability of error. A concentration closer to the limit, for example, 4 µg/kg for S3, required more samples to lower the concentration below the predetermined limit: 23 samples per silo, with a 50% probability of error. The monitoring costs were the highest at CP1 (€19,800 for S3 and €12,000 for S5), since the number of batches, in this case silos, was higher than the number of ship compartments at CP3. The replacement costs were higher at CP3 than at CP1. Replacement of the batch at the end of the chain, a higher AFB1 concentration and, consequently, a higher percentage of replaced maize, led to higher replacement costs.
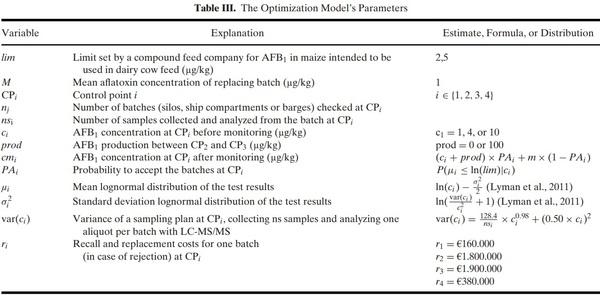
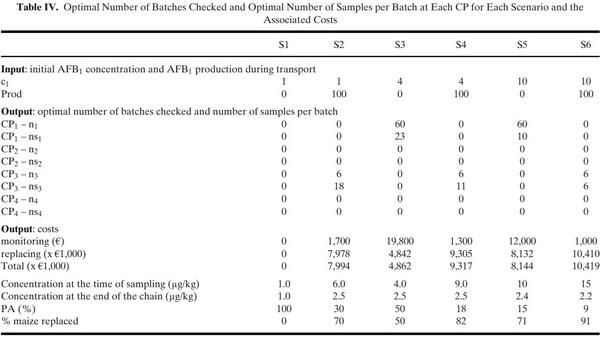
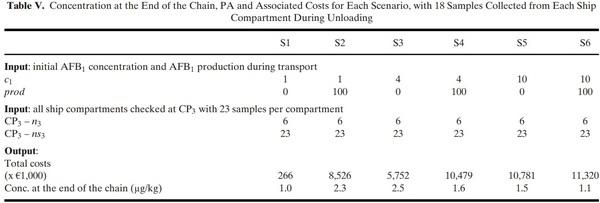
Table IV shows that the optimal CP was different, depending on whether AFB1 production occurred during transport. Hence, no conclusion can be drawn from Table V with regard to the most critical CP. Collecting samples only at CP1 would not lead to a satisfactory concentration at the end of the chain, in case of AFB1 production later in the chain. The safest option would be to collect samples at CP3 when unloading the sea-going ship. S3 needed the highest number of samples per batch (23 samples) to lower the average concentration to the predetermined limit. If we collected 23 samples per ship compartment at CP3 for all scenarios, the average concentration at the end of the chain for all scenarios would be below the predetermined limit (Table V). However, the costs would be higher than when tailoring the number of samples and the CP to each scenario.
Table IV shows that for S2, collection of 18 samples from each ship compartment with an average concentration of 6 µg/kg led to a probability to accept and retain the batch in the chain—that is, a 30% probability of error and, consequently, a probability of 70% to reject and replace the batch. Since we only considered the average concentration at the end of the chain, the average concentration after replacing 70% of the maize would be 2.5 µg/kg, which is exactly the predetermined limit. However, in individual cases, each tested compartment has a 30% chance to remain in the chain, and the end concentration could be 6 µg/kg, which is above the predetermined limit.
If a company prefers to lower the probability of error, more samples should be collected. As an example, we took a 5% probability of error at one CP. The results are shown in Table VI. Again, the closer the concentration was to the predetermined limit, the higher the number of samples needed to correctly classify the batch as compliant or noncompliant. For a concentration of 6 µg/kg (S2), 422 samples per batch were needed for a 5% probability of error. For a concentration of 4 µg/kg, it was impossible to have a probability of error of less than 20%, since the concentration was too close to the predetermined limit, and sample collection and analysis introduce significant uncertainty.
Table IV indicates that it was optimal to test all batches at one CP. This was because all batches had the same average concentration. If this average concentration was above the predetermined limit, all batches needed to be tested and replaced. For the case where only 50% of the batches could be tested at one CP, it was not always feasible to have an average concentration at the end of the chain below the predetermined limit (Table VII). More samples per batch, as well as more CPs, were needed (Table VII). The associated monitoring and replacement costs were both much higher (Table VII).
4. DISCUSSION
Optimization models have been frequently used to optimize monitoring plans in the life sciences, such as for the detection of animal diseases, the detection of pests or invasive species, the detection of water contamination, and, in some instances, for the detection of hazards in food and feed (Focker, van der Fels-Klerx, & Oude Lansink, 2018). This research provides insight into the most critical CPs and gives an indication of the number of samples needed to be collected to fulfill the concentration criterion at the end of the chain.
This study’s first conclusion is that it is most cost effective to collect samples from all batches after harvest when no aflatoxin production was possible after harvest, since the replacement costs are the lowest at the beginning of the chain. The same result would be applicable to mycotoxins such as replace contaminated batches after the a deoxynivalenol, which are produced in the fields and not during storage. If there is aflatoxin production during storage, it is most cost effective to sample, analyze, and replace contaminated batches after the aflatoxin production period to avoid the double monitoring and replacement costs before and after storage and transport. This result would be applicable to other storage mycotoxins, such as ochratoxin A.
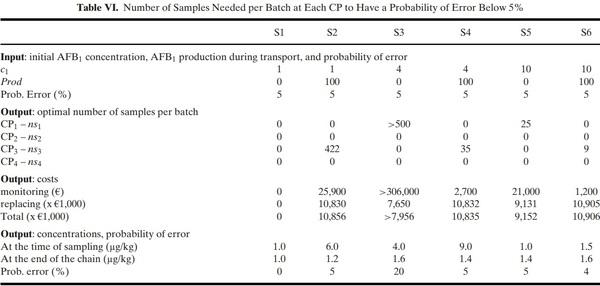
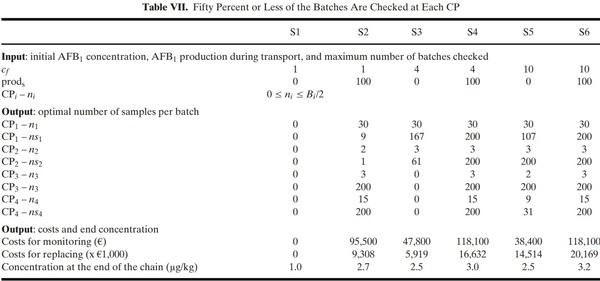
Based on the optimization model used in this study, samples were collected from all batches at one CP along the chain, rather than from half of the batches. This is because the average concentration of all batches was used at one point, which is the same as all batches having the same concentration. If a different concentration was seen in each batch, the results could have indicated that only half of the batches should be tested: testing and replacement of the half with a high concentration would be sufficient. Forecasting models for aflatoxins in maize at harvest could assist with deciding from which fields to collect samples. In this study, it is assumed that all fields have the same average concentration; however, in practice, concentrations will differ across fields, depending on the weather, location, and agricultural practices. The fields with high concentrations—and not necessarily those with low concentrations—should be tested.
The results of this study show the average outcome when the same scenario with the same batches are monitored for an infinite amount of times. As discussed before, the probability of error remains high in some cases. Increasing the number of samples reduces the chance that a batch with a high concentration is processed into an end product that will be consumed, but also results in higher costs. As can be seen from the results, more samples are required to correctly classify a batch with an AFB1 concentration that is close to the predetermined limit as contaminated or compliant, compared with a batch with an AFB1 concentration that is much higher than the preset limit. A probability of error below 5% might not be achieved at one CP, even with a high number of samples collected, when the concentration is close to the predetermined limit. When following Regulation Number 152/2013 for the sampling and analysis methods for the official control of feed (EU, 2013), 100 samples should be collected from a ship compartment of 10,000 tons. Since the batch is very large, samples may be collected from only a part of the batch. For a silo of 1,000 tons, 100 samples should be collected. A minimum of 100 samples should be collected from a barge of 2,000 tons. These sample sizes are, in most cases, more than sufficient for a low probability of error. However, when the concentration is close to the predetermined limits of 6 µg/kg in S2 and 4 µg/kg in S3, 100 samples per ship compartment were not sufficient to achieve a probability of error below 5%. In addition to increasing the number of samples from a batch, collecting and analyzing samples at multiple CPs could decrease the overall probability to accept a contaminated batch, in cases where the AFB1 concentration does not change along the chain.
The total cost estimated in this study, up to €10 million (Table IV), were much higher than only the costs for monitoring only, which went up to €19,800 (Table IV). First, this was because scenarios were considered where AFB1 could be produced during transport, or cases where the concentration in the fields was high, resulting in replacement of a high percentage of maize. In addition, only the replacement costs per batch were considered, whereas the batch could be sold for other purposes in practice. Most rejected batches have an AFB1 concentration above the considered limit of 2.5 µg/kg, but below the European limit for animal feed of 20 µg/kg (EU, 2002). These batches could thus be sold and used as pig and poultry feed, as such significantly lowering the replacement costs. Investment in good storage conditions would eliminate the high recall costs later in the chain and would be the most cost-effective solution in the long term.
With an official control (described in Regulation Number 152/2013) that prescribes the sampling and analysis methods for the official control of feed (EU, 2013), the analytical result is reported with a confidence interval that is based on the measurement uncertainty of the analytical method. This measurement uncertainty includes different aspects: bias, recovery, and precision—both within and between laboratories. Only if the entire confidence interval, including the lower bound, is above the predetermined limit, a batch is rejected. However, most private companies do not consider measurement uncertainty when buying maize. Furthermore, companies often have an internal predetermined limit for AFB1, which is lower than the European limit; in this study, a predetermined limit of 2.5 µg/kg was considered.
5. LIMITATIONS OF THE MODEL
This study has some limitations, which are discussed below. First, the model was based on several assumptions: the maize supply chain, the costs for sampling and analysis, and the costs for replacing the batches. Further, the estimated probability to accept a batch assumes that the test results followed a lognormal distribution. In addition, the variance due to sampling was estimated by Johansson et al. (2000b) using a limited number of batches, while the variance due to sample preparation and analysis was based on the work of Stadler et al. (2018). Furthermore, only six scenarios were considered, most of which are extreme scenarios, which rarely occur. In practice, Scenarios 1 or 3 are the most likely to occur. Nevertheless, most assumptions are based on previous studies, and on what is observed in practice. Therefore, we believe that the model can still provide insights into cost-effective monitoring plans for mycotoxins along the cereal chain.
6. CONCLUSION
Since aflatoxins can accidently be produced during maritime transport under conditions of high temperatures and humidity, the harbor in the country of destination is a critical CP. The number of samples to be collected at the CP depends on the average batch concentration. With a high concentration, few samples will be sufficient for contamination detection; however, with a low concentration or a concentration close to the predetermined limit, many samples are required. The replacement costs become higher and higher further along the chain: Transport costs are added and, if contaminated maize is processed into feed, expensive recalls can be expected.