The primary objective of pelleting is to produce a palatable, high quality product with minimum production expense. Manipulation of the feed pellets during the storage, transporting, and transfer to feeding lots seriously reduces the number of feed pellets that finally reach the feed pans. It seems that the best solution for this problem is to increase the Pellet Durability Index (PDI) of the feed pellets using different settings in the manufacturing process and different raw ingredients.
The factors influencing pellet quality such as grinding, mixing, conditioning process, pelleting techniques and cooling are fertile ground for pellet quality improvement.
Norwegian University of Life Sciences (UMB) has carried out research as a part of the Feed Manufacturing Technology (FMT) Master of Science program. The research experiments were carried out at Centre for Feed Technology, an experimental feed plant associated with the university.
Pellet press settings - Gap between the rolls and pellet-press die influence the PDI
Previous research has shown that increased pressure generated in the die hole increases the physical properties of the feed pellets. Elevated pressure seriously depends on the coefficient of friction (CF%) between conditioned feed compound and die wall, plastic properties of conditioned material and its conditioning time. In the gap between the die wall and roller, a layer of feed material with a specific thickness is forming. This layer of the feed material and its thickness directly influences formation and compaction of the material inside the pellet press die-hole by roller/die frictional force.
Research has been performed with different roller/die pellet press settings in order to find the best roller/die gap settings related to increased physical properties of feed pellets. Results showed that by increasing the roller/die gap, several layers of feed mash are created and CF% is increasing (figure 1).
Figure 1. Layers of feed mash and coefficient of friction areas during the pelleting process
Increasing the roller/die gap to 2 mm, as well as reducing feeder rate by 50%, resulted in significantly (P<0.05) increased PDI (table 1). This is probably caused by prolonged kneading effect time. Obviously, by decreasing the feeder rate, CF% helps forming higher PDI values, but energy consumption and production capacity reaches commercially non satisfactory level and reduced production capacity. In addition to the CF% influence on PDI, larger roller/die distance forms better pressing angle. This produces higher pressure on the material that enters the die hole, thus material in the hole as well (figure 2). All this leads to better-compacted particles into the single feed pellets and elevates physical properties of the animal feed.
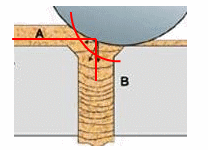
Figure 2. Angle of Pressure "Angle of nip"
Table 1
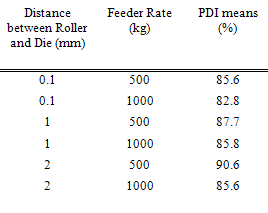
When roller/die gap set to be too big, that often results irritating choke-ups. Opposite, if rollers are adjusted hard against the die, some damages of the die-hole inlets and die blockages are possible.
Pressing angle between the die and roller and the gap between them increases the total amount of fine particles, as shown in figure 3. This shows the grinding ability of the pellet press produced by the roller/die kneading effect. This effect might be used for better control of the particle size and energy consumption in the process of grinding.
Figure 3. Roller/die gap and particle size distributionEffects of Die Whole Diameter and Die Thickness on Pellet Quality
Pellets are sensitive to shearing actions at the places where they are cut off after leaving the die. Through this impact, newly created surfaces are sensitive to further deterioration. Therefore problems related to the feed pellet quality, die whole diameter and die thickness have been studied through the "Pellet Quality" project at the Department for Animal and Aquacultural Sciences at UMB. The aim of the study was to observe how the same die-hole diameter with different die thicknesses affects the pellet quality in relation with the different feeder rates.
The same die-hole diameter (3.5mm) and different die thickness (50mm and 60mm) were used, with additional feeder rate change, from 500 kg/h to 1000 kg/h. Holmen Pellet Test showed highest durability value (PDI=90.1%) in samples for 3.5mm die-hole and 60mm die thickness configuration with the feeder rate 500 kg/h. Significantly lower PDI values (P<0.05) was demonstrated for 1000 kg/h feeder rate independent on die thickness (figure 4). This is caused by lower pressure in the die-holes and higher feed mash acceptance in the pellet press, which makes the newly formed feed pellets more vulnerable for abrasion and cracks. The highest durability loss (3.3%) was found with 50mm die thickness and 1000 kg/h feeder rate.
Figure 4. Holmen Test results- feeder rate and die thickness influences PDI values
Similar research, studying the variation of the die-hole diameter, illustrated a strong positive effect of decreased diameter on PDI values (figure 6). This effect was obvious even if diet composition changed.
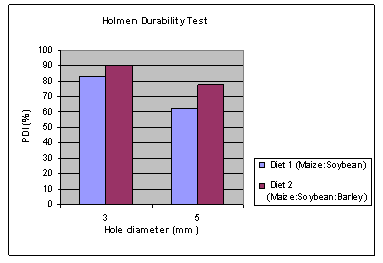
Figure 5. Influence of die-hole diameter on PDI values of two different diets
In addition to the tale of the results presented above themselves, these results also show how important pellet press settings are for the technical quality of the pellets, and thus for the profitability of the pelleting process.