I decided to write this article following a concrete case, in which I was asked to give an opinion regarding the purchase of fans to cool the cows along the feed line of a certain dairy farm. This manager was 240 meters long and was used to feed (and cool) 320 cows.
The dairy owner had two proposals for fans to be installed in the feeding area. The first fan was 50″ in diameter with a 1.5 hp motor and belt drive, with a power consumption of 1.1 kWh. In order to achieve the desired wind speed of 3 meters per second, the fans had to be installed 9 meters apart. The price of this fan was $500. The second fan was 63″ in diameter, with a 1 hp motor and direct motor operation, with power consumption of 0.75 kWh and recommendations for installation at a distance of 12 meters between one fan and the other to achieve the desired wind speed. The price of this fan was $1,200.
The large difference in price between the two fans led the farm owner to prefer purchasing the cheaper fans. Although to ventilate the manger with the cheaper fans, 27 fans are required, but at a price of $500 per fan. This is an investment of $13,500. Choosing the more expensive fans would require the purchase of only 20 fans, but the investment is $24,000. A gap of $10,500 is significant and there are many things a farm owner can do with this amount of money.
Before making a final decision, the farm owner decided to consult with me on the matter. I explained to him that the gap in investment is large, but the decision should be made only after we calculate the total cost of cooling, which includes on the one hand the cost of investing in the cooling equipment (in our case the fans), but also the cost of operating the equipment over time. Sometimes there are surprises, I told him, and we went to calculate it together.
In the first stage, we defined the duration of the cooling operation on the farm, which is 180 days a year. In the second stage, we calculated the duration of the operation of the fans in the manger area throughout the day, and this was 10 hours. Hence, each fan operates 1800 hours a year. At this stage, we moved on to calculating the electricity consumption for cooling cows along the given manger with each of the fans for the first year of operation, and subsequently for each of the following six years (when we estimate seven years of existence for the fan). The comparison results are presented in the following table.
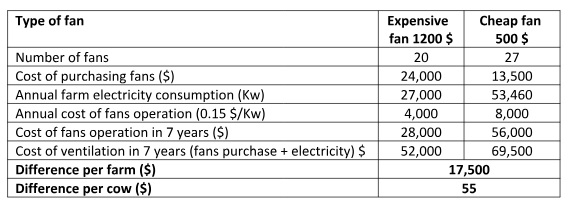
From the table, it can be seen that, despite the cheap price of the fan, what is more important is its ventilation intensity (spacing between fans), as well as the energy efficiency of the motor (electricity consumption per hour of operation). In our case, the more expensive fans had greater ventilation power, which allowed us to achieve the desired wind speed with fewer fans, and no less, more efficient motors (direct operation versus belt operation), which allowed us to achieve the result of spending less electricity.
This calculation should be done for the number of years the fan will operate. If we were to compare the result at the end of the first and second year, we would see an advantage for the cheaper fans, since the price of the fan as part of the total expense was relatively large. Starting from the third year, and until the end of the seven years, the trend reverses and the expensive becomes cheaper.
So, the cheapest fan is not always the most economically viable.