In a negative pressure-ventilated poultry house, the amount of air entering through each side wall inlet depends primarily on the level of negative pressure generated by the house exhaust fans, the size of the inlet opening, and the air inlet design. The higher the static pressure, the faster the air will enter the house and the greater the amount of air that will enter through an inlet. Not surprisingly, the larger the inlet opening, the greater the amount of air that will enter through an inlet, and finally, European-style inlets tend to have a higher air-moving capacity at the same opening than traditional galvanized door inlets.
In a negative pressure ventilation system it can be estimated that 750 cubic feet of air will enter through each square foot of inlet opening each minute (cfm/ft2) at a negative pressure of 0.10". Accordingly, if the typical 44" X 7" galvanized door inlet (actual opening 42.75" X 5.75") is fully opened and the exhaust fans in a poultry house are generating a negative pressure of 0.10", we can expect that 1,280 cubic feet of air will flow through the inlet each minute (Equations 1 and 2). If the inlet opening were only two inches wide, we would expect the amount of air entering through the inlet to be approximately 445 cfm. Again, this is only an estimate and only pertains to a 0.10" static pressure.
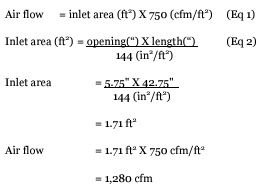
So, just how accurate is this method of determining how much air is entering through an air inlet, and how does the amount of air entering through an inlet change at other levels of negative pressure? To answer these questions, the performance of typical 44" X 7" (42.75" X 5.75') and 44" X 14" (42" X 10.75") galvanized door inlet were evaluated in a fan/inlet test chamber*.
The opening of the 44" X 7" air inlet was varied from one inch to fully opened (5.5") at static pressures of 0.05", 0.10", 0.15" and 0.20" and the capacity of the inlet was measured. Testing found that at a static pressure of 0.10", that 1,360 cfm flowed through the inlet when it was fully opened, which is only six percent greater than the estimated value of 1,280 cfm (Table 1). As the inlet opening decreased, the difference between the measured inlet flow rate and the estimated inlet flow rate increased. When the inlet openings were decreased to two inches and one inch, the difference between the measured and estimated inlet air flow rates increased to 41% and 61%, respectively.
The test was repeated for the 44" X 14" galvanized door inlet. Chamber testing found that at a static pressure of 0.10", 2,550 cfm flowed through the inlet when it was fully opened, which is only eight percent greater than the estimated value of 2,250 cfm (Table 2). Again, as the inlet opening was reduced, the difference between the measured flow rates and the estimated flow rates increased. When the inlet opening was decreased to two inches and one inch, the difference increased to 64% and 71%, respectively, which is fairly similar to what was documented with the smaller galvanized door inlet.
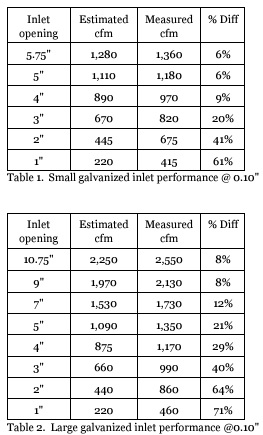
Though the inlets were of similar length, when opened the same amount (i.e., 1", 2", 3", 4", 5"), the amount of air flow through the taller inlet was greater than it was through the shorter inlet. The higher air flow rates are attributable to the longer sides of the taller side wall inlet which provided additional inlet opening when compared to the shorter inlet. This is an important distinction. The taller the inlet, the greater the amount of air that will exit through the sides of the inlet, which during cold weather will tend to quickly drop to the floor near the sidewalls of a house.
The testing of the two galvanized air inlets indicates that the air inlet air-moving capacity estimate of 750 cfm per square foot of inlet opening is most accurate for use with fully opened inlets. One example of where the 750 cfm per square foot of inlet opening estimate could be successfully used is determining the number of inlets a house requires. For instance, if a grower wanted to be able to operate five tunnel fans that move a total of 120,000 cfm @ 0.10" using a house’s air inlets before transitioning to tunnel ventilation, they would divide the 120,000 cfm by the estimated capacity of each of the two galvanized inlets when they are fully opened (Smaller inlet = 1,280 cfm. Taller inlets = 2,250 cfm) to determine the total number of inlets required.
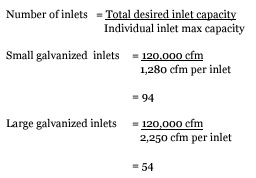
For other sizes of galvanized inlets, the maximum capacity of the inlet can be easily estimated by using Equation 2 and then dividing the total amount of fan capacity by the air-moving capacity of an individual inlet using Equation 1. Keep in mind this is an estimation; it is always preferred when determining the number of inlets to install in a house where actual inlet capacity test data is used, such as that shown in Tables 1 and 2.
*Thanks to Georgia Poultry for allowing us the use of their Fan/Inlet test chamber to conduct this study.
You can read Part II by clicking here.
This article was originally published in Poultry Housing Tips, Volume 36, Number 9, 2024. University of Georgia, College of Agricultural and Environmental Sciences Cooperative Extension (https://www.poultryventilation.com/).