Introduction
Good quality air will provide a healthier environment for pigs and people. Improved health will
mean improved profits and an easier production system to work with.
There has been a literal explosion of new products and technologies in the swine industry
ventilation equipment industry over the last 15 years. In the midst of all this, it is worth
reflecting on the original goal of a ventilation system to maintain indoor air quality (IAQ):
1) In the winter provide fresh air (oxygen) uniformly and draft free, while exhausting
stale, moisture-laden air.
2) In the summer, provide and direct enough air to flush out hot air to provide cooling.
Fresh air consists primarily of Oxygen (at about 21%) and Nitrogen. Once inside the barn, the
fresh air will achieve many purposes:
1) Oxygen for respiration and life,
2) A source to transfer CO2 and H2O, the byproducts of respiration,
3) Removal of moisture from manure and water spillage, etc.,
4) Removals of gases from manure, primarily NH3, are absorbed (See Table 1),
5) Removal of dust and other particulate matter from flooring, dander etc.,
6) If direct-fired heaters are used, then oxygen is used up and the air absorbs the by-products
of combustion; CO2, H2O, CO and other partially burned combustion by-products,
7) A medium to transfer heat in the case of convective heat (forced air or hot water pipes)
systems.
There are many different ventilation systems available to achieve the goal of good IAQ; natural
ventilation; mechanical (fan) with inlets and fans in walls, ceilings or both; pit exhaust; use of a
variety of heat systems; electronic controls with relative humidity sensing and control.
All systems require good design, maintenance and management to ensure the system can
perform. What checks can be made to ensure the fundamentals are being met, ensuring proper
IAQ for both pigs and management?
The following are basic management steps:
1) The temperature must be reasonable for the pig. In many cases, particularly in winter,
rooms for pigs tend to be too cool to start and too hot after a short time. Since the pig is a
homoeothermic animal, it will choose a poor environment over a cool or hot temperature.
Anyone with partial slat barns can testify to this particular problem.
2) Check that the fan system has been designed and is controlled to maintain continuous
winter ventilation to maintain adequate oxygen, CO2, RH and other gas levels. In many
cases, the cold weather means a certain amount of heat is required, otherwise an adequate
barn temperature will not be achievable.
3) Check to ensure minimum air flow requirements for hot weather are available to ensure
adequate cooling. In many cases, the fan system may be sized but restrictions occur at the soffit, the air inlet or preheat duct openings.
4) To further verify that temperature and fan setting s are correct, a system performance
analysis and Standard Operations Manual is required.
5) Check that the fresh air supply, from the outside to the inside air inlet, is adequate. Bird
screens may be too small at ¼" x ¼", when at least ¾" x ¾" to 1" x 1" is required to
prevent clogging, choking air supply. Space between the underside of the roof to the
insulation is sometimes 'squeezed.' Also, where the side wall fans exhaust air close to
soffit openings, some stale air will cause frost build-up on soffit openings and starve the
barn. This also creates the problem of stale air back into the barn.
6) Install a static pressure monitor, high to the outside, low to inside. Check pressures for
0.06" to 0.08" water column static pressure for all but hot weather, when the target is an
energy efficient 0.04".
7) Check for drafts and obstructions that interfere with air patterns. Any problems result in
drafts on some pigs and stale air in other areas.
8) Check that air does not 'short circuit' from intake to exhaust fans. This air has little value
to the pigs.
9) Set controls to match the season's requirements. Too rapid changes in fans turning on or
off may appear to maintain close temperature control, but the effect of higher air speeds
may cause the pig to feel chilled from the 'wind chill effect'. Proper controls settings are
the second most common problem found on many farms.
10) Monitor the air quality with your nose as well as other equipment. An accurate relative
humidity gauge, CO2 measuring devices, fast response hi/lo digital thermometers; and
other gas checks including NH3 and CO (for direct fired gas heat systems) should be part
of the regular monitoring and data collection procedures.
11) Air distribution and movement are very important components. The single weakest link
in most ventilation systems is the air distribution (inlet) systems. They typically
experience the following deficiencies:
1) Undersized for summer air flow.
2) Non-uniform locations due to design, obstructions, etc., causing stale, hot spots.
3) Insufficient maintenance so the inlet no longer closes evenly. This results in cool,
drafty areas, and hot spots for long time periods, negatively affecting performance.
4) No method to direct air into pens during extreme hot weather to provide additional
cooling.
Minimum Air Flow Problems
1) Air is not distributed properly
2) Fans do not draw evenly due to excess spacing and cause non-uniform air distribution
3) Minimum Stage 1 fan is too fast or too slow
4) Minimum Stage 1 fan speed is not adjusted to compensate for the increased respiration and
gases present as pigs grow
5) Compensation for the combusted air from unvented heaters is not made
Many sources now provide design services. The calculations are readily available to estimate minimum and maximum airflow rates and choose equipment to provide the minimum requirements. The design must take into account the facilities layouts to ensure an optimum
system performance.
Locations of stage 1 (minimum ventilation) and stage two fans, air inlets and heaters each have a large affect on winter IAQ. This is exacerbated by the use of solid and semi solid floor systems and pen divider walls, common walls between rooms and reducing the opportunity to locate fans optimally and by installing only one inexpensive heater to heat a large area.
The Indoor Air Environment and Airborne Diseases
Airborne disease organisms that are prevalent include bacteria, viruses, mould, dust and fungi,
all of which can cause respiratory challenges. The number of airborne pathogens present in
outside air is about 100 per cubic meter while inside air can be up to 1,000,000 per cubic meter.
Industry losses from poor IAQ include slower growth and expenses incurred to combat
respiratory infection. Air quality improvements can reduce this loss by up to 80%.
Controlling airborne disease organisms is more easily accomplished if the systems they require
to survive are understood. Disease organisms require moisture (humidity) to remain viable
through airborne transmission. By lowering RH from 90% to 80% will reduce airborne disease
organisms by 50%; the best range of RH for killing airborne pathogens is 50 to 70%. Normally,
a target of 60% when adjusting cold-weather ventilation fans is sufficient to ensure proper
control of air borne contaminants. The use of convenient, accurate instruments for measuring
RH is much easier today with the use of digital temperature/relative humidity devices. Figure 1
shows contaminant concentration survival rates versus humidity for a number of air borne
substances.
Relative humidity in an animal facility is a function of animal activity and numbers, body
weight, manure systems, ventilation rate, and outdoor air relative humidity. Since most of these
elements change from one day to the next, RH needs to be checked and ventilation rate adjusted
accordingly. Weekly is usually frequent enough. Use a digital RH pen to check RH, or consider
a temperature/RH data logger. If RH is above 70%, increase exhaust flow. If RH is below 50%,
decrease fan speed. Note RH will range daily +/- 10% from a mean. Lows occur during night
time and resting, highs during inspection/feed times in mid day.
In extreme cold weather, RH is much harder to maintain at the targeted 60%. Extended cold
snaps may result in consistent RH as low as 35%, assuming adequate heat is available. At this
point, additional monitoring to verify air quality includes CO2.
RH is of little consequence in warm or hot weather since the high ventilation rates required to
keep air temperature under control usually dilute out a great majority of airborne disease
organisms. Regardless of the RH, respiratory problems will be minimal during warm or hot
weather due to simple dilution. Control of air temperature during warm or hot weather should
be a function of exhaust fans on thermostats.
It is important to note that RH in production facilities increases as pigs grow and from daily
changes in outside outdoor weather conditions. Check RH several times a week through cold
weather and speed fans up or down as needed to keep RH between 50 and 70%. With proper
measuring of all the various parameters and correlating these to environment, fine-tuning and
adjustments can be made to further improve performance. Some of the parameters and
relationships to environment control include:
RH - the RH in a building can be maintained at optimum levels. This is dependent,
however, on manure management, dung habits, waterers, outside weather, etc.
Temperature- all pigs perform best between a minimum and maximum temperature,
termed 'Upper' and 'Lower Critical Temperature'. The actual temperature will depend on
many factors
Air Speed/Drafts - as pigs grow and outside air temperatures rise, the effect of higher air
speeds decreases. However, too high an air speed can cause large drops in performance.
A properly designed and operated ventilation system and controller can ensure that
drafting potential is eliminated for very young pigs and increase drafts for older pigs.
Radiation - This describes the heat the pig may gain or lose from his surroundings.
These surroundings in include how many other pigs are in the pen, space available,
insulation levels in building, etc.
Floor Type - the flooring has an enormous effect on pig comfort. Cold concrete is much
cooler, at least initially, than plastic. However, concrete, once warm, will remain warm.
Other Gases (NH3, CO, CO2, etc.) - Many gases have an effect on the pigs health and
comfort level.
Threshold Limit Values-Time Weighted Averages (TLV-TWA)
The time-weighted average is the concentration for a normal 8-hour period and 40 hour
workweek, to which workers may be continuously exposed, without adverse affect. The
research for continued exposure affects on pigs is limited, but when available shows that there
is negative effects. Table 1 shows some common gases and the effects on pigs and humans.
The major gases of concern include ammonia, hydrogen sulfide, carbon dioxide, methane and
carbon monoxide (when unvented heaters are used). The goal is to ensure that adequate fresh air
is provided to animals for respiration; that gases and other contaminants are removed; and that
the fresh air is provided in a way that does not cause drafts or other negative events.
Changes in Recommended Ventilation Rates
As pigs grow, the need for higher ventilation rates increases. An example would be a 500-head
nursery:
Minimum ventilation 650 CFM @ 8 kg
Minimum ventilation 2000 CFM @ 30 kg
If the minimum fan is not set to provide the desired airflow, then problems begin to arise:
Too high an exhaust flow wastes energy and dries air out while running the risk of heat
shortages; too low an exhaust airflow rate and air quality suffers.
Figure 2 indicates the changing requirements for a typical 500-head nursery facility over an 8-
week time period. Failure to adjust the minimum airflow will result in poor air quality. The
effect on equipment life can be negative as well.
Where to set the minimum fan as pigs grow poses a problem. Most controllers read out in %.
This % actually refers to a percentage of the amount of voltage being supplied to the fan motor.
The fan motor uses the supplied voltage to turn the fan blade. Different fan and motor
combinations then create different amounts of exhaust flow rate.
Figure 3 is from an actual Stage 1 variable speed fan/controller test. As can be seen, the fan response to changes in % settings indicate a very non-linear response, that can produce erratic control.
Also, by adjusting the % setting to change the desired CFM can have varying effects, depending
on where it was initially and where it is set to. For example, changing from 30 to 40% can
double the CFM output. Changing from 50-60 % will only increase CFM 11%.
Figure 1.-
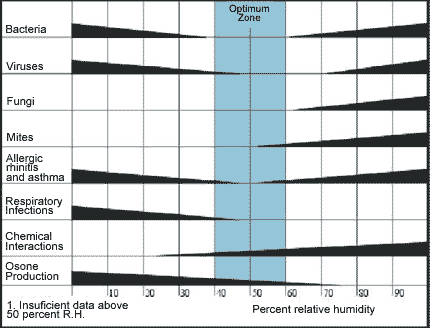
Figure 2.-

Figure 3.-
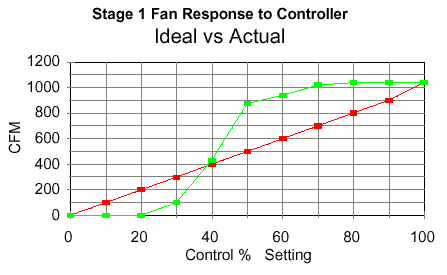
Conclusions
Minimum airflow management and indoor air quality have a large impact on pig and human
health. Performance alone justifies the costs of properly designing, calibrating, setting and
reviewing adequate air to the facility. Longer-range implications include human factors as well.
An understanding of the fundamentals of indoor air quality is necessary for producers. Proper
IAQ pays for both pigs and producers short and long term health and production efficiency.