Introduction
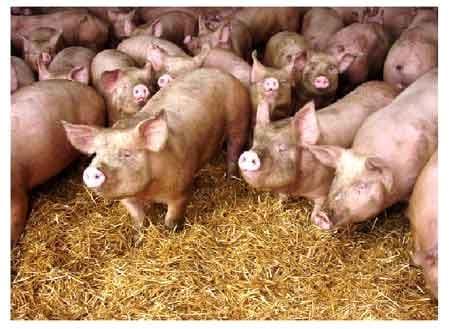
Composting hog manure has not been considered a viable alternative manure management practice until recent years, and even now the practice is thought to be more labour intensive and more expensive than conventional liquid manure handling practices. While it is true that composting is not a great fit with conventional rearing systems, it can have a place in hog production. Where dry sows and grower/finisher hogs are housed in facilities with straw or shavings as bedding or absorbent, composting is a natural solution to manure handling problems.
There are new challenges in manure handling that may be more easily managed by on-farm composting of animal manure. In the last decade, the non-farm population has increased in the rural areas. That has brought them into closer contact with farming activities and they are sometimes shocked at the scale and the odours associated with some modern livestock operations. This has led to lawsuits and protests taken to local governments seeking redress or restriction of farming activities. While Manitoba does have a law that protects farmers from "nuisance" lawsuits if they are following good management practices, most farmers would undoubtedly prefer a less confrontational relationship with their neighbors. While not completely odour-free, composting does not generate the same kind of manure odours typical of manure collected and stored in pits or earthen storages under anaerobic conditions. Although liquid manure handling systems can be managed in ways that satisfy the rules against liquid manure runoff, they are inherently riskier systems, and many farmers will undoubtedly want to avoid those risks. Composting fits easily into manure handling systems that generate manure with low levels of added water.
Many farms, especially the larger ones, will be required to have comprehensive nutrient management plans. These plans must address how farmers intend to apply manure at rates that do not exceed the soil's capacity to absorb manure nutrients, especially phosphorus, or the capacity of crops to remove them. This means hauling manure further, and that is more easily done with compost. Larger hog production units may want to take advantage of the opportunity to sell or broker this nutrient to crop farmers by changing the manure into a form that can be hauled greater distances.
All of these constraints to conventional systems present new incentives for composting livestock waste and in the process, generating a product that is more acceptable to the public for the material that it really is – a rich nutrient that maintains soil quality in a way that chemical fertilizers cannot.
Swine Production Systems and Composting
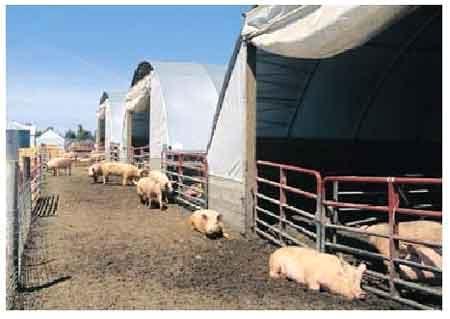
Deep bedding is critical to the success of hoop shelters (Biotech shelters) (Richard and Smits, 1998). Alternative bedding sources that have been used include baled cornstalks, grass hay, ground corn cobs, or baled newsprint. But on the prairies where wheat straw is plentiful, good quality straw free from molds is the most suitable bedding for Canadian climatic conditions. The heat from the decomposing manure pack may cause problems in Manitoba’s hot humid summers.
Additional bedding may be needed to insulate the pigs from the pack and access to an outdoor shady area helps keep the pigs cool in the summer.
Shortly after populating the shelter, the pigs develop dunging patterns such that the sleeping area is kept relatively clean. However, there are enough nutrients distributed in the shelter to cause warming of the bedding pack providing a comfortable sleeping area. When the finished hogs leave the shelter, cleanout can be performed with a skid-loader. Since the shelter may be filled 2 to 3 times per year, the manure is usually stockpiled until conditions are suitable for application.
Stockpiling may cause excessive loss of nutrients and present runoff, odour and fly problems as well as being visually unpleasant. Since the pigs do not tend to dung where they sleep, nutrients are not evenly distributed in the shelter so the straw manure mixture is not a homogeneous mixture and nutrients tend to be over- or under-applied in the field. Planning is required to approximately combine the wetter material with the drier material in a windrow. Turning of the windrow using manufactured equipment to mix and aerate the material will ensure a uniform, well-degraded product.
In the past few years, several High-Rise™ swine barns have been built in Ohio, USA and one near Exeter, Ontario (Fleming and MacAlpine, 2001). The High-Rise™ barn is a two-storey hog barn where the pigs are raised on a slatted floor in the top storey. Manure and urine falls through the slats and is absorbed by the shavings or chopped straw below. Air is used to dry the manure so that it can be removed as “solid” manure after a period of up to a full year. All room ventilation air is drawn down through the slats to exhaust through wall fans in the lower floor. In addition, aeration air is forced up through the straw/manure or shavings/manure mixture. This air is blown through pipes buried in the floor and upwards into the manured material via holes drilled through the concrete floor of the manure storage area.
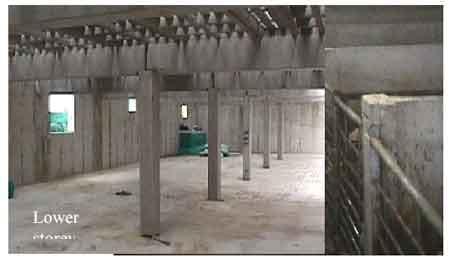
In this system the pigs do not manure uniformly over the floor area, thus some area in the bottom floor will remain quite dry while other areas are saturated. Because the manure does not mix with the straw there is virtually no composting taking place in the bottom area of the building.
Straw and absorbent material must be placed strategically in the manure collection area to
prevent puddling. It is possible that manure and urine will trickle into the aeration plenum under the concrete and accumulate there. It may be necessary to pump the liquid frequently to avoid freezing in the area of the in-floor pipes. A system such as this provides an ideal environment for rodents and flies necessitating a control program for these pests. Since the dryer straw tends to be around the walls of the manure storage area in the bottom storey, extra work is required to mix the wet material with the dry at cleanout. In parts of the USA where this type of barn is used, it is common to move the manure from one zone in the barn to another, a few times during the year. Usually cleanout is timed to coincide with field operations however some stockpiling of manure is required. Composting activities can take place any time during the year except in high snow-fall area and during extremely cold weather. Shaping the windrows into high piles prevents freezing even in the coldest weather.
Separation of manure using mechanical or chemical means or a combination of the two is necessary in liquid manure systems. Screw presses are now available which are capable of separating the fine particles found in liquid swine manure from the liquid effluent. The solids must be combined with a bulking agent such as straw, old hay, chipped corn stalks or shavings to compost effectively.
The Composting Process
Composting is the aerobic (oxygen requiring) decomposition of manure or other organic
materials in the thermophilic temperature range of 104 – 149° F (40 - 65° C). Nature provides an extensive, native population of microorganisms that are generally attached to all organic wastes.
When conditions are right, these microbes grow and multiply by decomposing the material to which they are attached. From a scientific viewpoint, the composting process is started and managed under controlled environmental conditions rather than accepting the results of natural, uncontrolled decomposition. The composted material is odourless, fine-textured, and low-moistured and can be used for non-agricultural and agricultural purposes with little odour or fly breeding potential. When managed properly, composting improves the handling characteristics of any organic residue by reducing its moisture content, volume and weight. The process increases the value of raw manures by destroying pathogens and weed seeds and creating a media for the production and proliferation of beneficial organisms.
The composting process is a biological one that compares somewhat to the raising of plants or animals. The rate of composting, like the rate of plant or animal growth, can be affected by a number of factors.
Four keys factors are:
1. nutrient balance
2. moisture content
3. temperature
4. aeration
Nutrient balance is determined primarily by the ratio of carbon to nitrogen in the compost mixture. The microorganisms require carbon and nitrogen for growth since these elements are the main components of carbohydrates and protein. If nitrogen is in excess, large amounts of ammonia will be released to the atmosphere, if carbon is in excess the composting rate will decrease. The moisture content should ideally be 60 percent after organic wastes have been mixed. Maintaining the correct moisture level during the thermophilic (high temperature) phase of composting can be difficult in an open-air windrow system due to dry or wet climatic conditions. When the moisture content exceeds 60 %, the windrows subside and lose porosity thereby becoming anaerobic. Fermentation will set in and odours will be emitted from the material. If the moisture content decreases below 50 %, the rate of decomposition decreases because nutrients must be in solution to be utilized by microorganisms. As the microorganisms decompose organic matter, heat is generated and the temperature of the compost rises.
Decomposition is a dynamic process, accomplished by a succession of microorganisms, each group reaching its peak population when conditions are optimum to support that particular group.
When one group of microorganisms dies, another group populates the composting material until the next incremental change in nutrition and temperature occurs. Since the release of heat is directly related to the microbial activity, temperature is a good process indicator.
The temperatures of composting materials typically follow a pattern of a rapid increase to 120 – 140° F (49 - 60° C) which is maintained for several weeks, a gradual temperature decrease to 100° F (38° C) as active composting slows due to nutrient consumption, and a final leveling off at ambient air temperature. The temperature pattern is generally described in the following graph.
During the initial days of composting, readily degradable components of the raw material are rapidly metabolized, therefore the need for oxygen is greatest at the early stages and decreases as the process continues. Without sufficient oxygen, the materials become anaerobic. Anaerobic processes are generally slower and less efficient than aerobic processes. Little heat is generated under anaerobic conditions and intermediate compounds such as methane, organic acids, hydrogen sulfide and other odourous compounds are generated. Aeration also removes heat, water vapour and other gases trapped within the composting materials. Rapid composting will occur when conditions approximate those shown in Table 1.
General time-temperature pattern for composting.
Table 1. Recommended conditions for rapid compostinga. 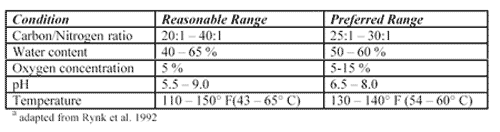
Turning the windrows restores porosity to the piles and reduces the particle size increasing the surface area of bulking material like straw. During the turning process oxygen is introduced into the windrow but it normally is rapidly consumed by microorganisms often within a matter of hours. However, restoring porosity enhances the passive movement of air into the windrow and accelerates decomposition. Excessive turning of the material can accelerate nitrogen loss, water loss and result in cooling of the compost. Generally turning the manure/straw mixture once a week for the first 4 weeks (with initial moisture levels of 70%) then once every 2 weeks for the next 8 weeks, under the normal moisture conditions found in Manitoba, has been found to yield an excellent composted product without the addition of water. It is critical to maintain the moisture level in the range of 60% in the initial 4 weeks of composting. If the moisture levels falls below 50% composting activity will slow and eventually cease as the material continues to dry.
Equipment for Composting
There are a variety of compost turners available for small farm operations and larger selfpropelled turners for custom composting operation. Most of the equipment is manufactured in the United States although there are a few Canadian manufacturers and distributors. Some styles of turners require that the tractor have a hydrostatic drive or have a creep gear. Some of the newer models are self driven and will pull the tractor when it is in neutral.
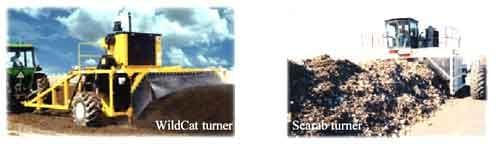
Although compost can be turned using a loader, production of quality compost requires the proper equipment. The improper sizing of equipment to perform the function can result in higher cost per tonne of finished compost. A quick search of the “internet” will provide a list of dealers.
Compost Site DevelopmentComposting ventures on any scale are doomed to failure without preparation of a site for
carrying out the process. The location of the composting site should allow easy access, a
minimum of travel and materials handling and a firm surface to support vehicles under varying weather conditions. The convenience of a particular site must be weighed against factors such as area, proximity to neighbours, visibility, and drainage and runoff control. Start designing your composting site by making a preliminary sketch of the compost facility showing all key areas, Show the prevailing wind direction, traffic flow pattern, the land slope, runoff patterns, surrounding land uses and pertinent environmental information such as location of wetlands or water bodies. For ground water protection consider the vertical distance from the compost pad surface to the seasonal high water table.
Good drainage is very important. Poor site drainage leads to ponding of water saturated
composting materials, muddy site conditions and excessive run-off and leachate from the site. A muddy composting pad is perhaps the most common site-related complaint of composting operators. It is important that the composting operation not be interrupted by rainfall.
Consult a soil scientist and an agricultural engineer for a site investigation before establishing a composting site. Run-off control beyond planting a grassed infiltration strip may be necessary to avoid polluting surface or ground water.
Composting – Summary of Pros and Cons
Benefits
- production of an excellent soil conditioner that adds organic matter, improves soil structure, improves water-holding capacity, reduces fertilizer requirements and reduces potential of soil erosion.
- potential market for the composted product i.e. home gardeners, landscapers, vegetable
farmers, turf growers, golf courses and ornamental growers. Compost can also be used as
bedding for poultry. - reduction in weight and mass, and improvement in handling characteristics.
- product can be stored and applied at convenient times of the year since organic N is less
susceptible to leaching and further ammonia losses - reduction of the C/N ratio to levels than are more suitable for land application compared to raw manure mixed with straw.
- destruction of pathogens and weed seeds.
- elimination of odours and flies.
- reduction of soilborne pathogens without the use of chemical controls
- potential income from tipping fees for organic waste. Note: composting off-farm wastes
must be considered cautiously.
Disadvantages
- a suitable site must be developed for composting activities to prevent runoff and leaching of nutrients. The composting site, storage of raw materials and finished compost can occupy a considerable area of land.
- cost of equipment, labour and management.
- potential odours from stockpiled materials collected for composting.
- climatic limitations may require a higher capital investment. Snow and rain can also interfere with composting and building compost piles or windrows.
- development of a marketing plan for excess compost.
- diversion of nutrients from agricultural land to other uses.
- potential loss of nitrogen.
- slow release of nutrients due to the higher concentrations of organic nitrogen in compost
compared to manure (this could be considered a benefit on soils with poor nutrient retention capacity).
Swine Seminar
January 29-30, 2003
Brandon, Manitoba
Katherine E. Buckley, PhD, PAg
Agriculture & Agri-Food Canada
Brandon Research Centre, Brandon, MB R7A 5Y3
References
Fleming, R. and MacAlpine, M. 2001. Evaluation of a 1000-head “Environmentally friendly facility” swine finishing barn. Final report for Ontario Pork.
http://www.ridgetownc.on.ca/research/Subject/manure.cfm PDF file.
Richard, T.L. and Smits, S. 1998. Management of bedded-pack manure from swine hoop
structures. Paper No. 984127 in the Proceedings of the ASAE Annual International Meeting, July 12-16, 1998, Orlando, FL.
Rynk, R. et al. 1992. On-Farm Composting Handbook. NRAES. Ithaca, NY.