The application of steam once brought on industrial revolution, now it is an indispensable part of industrial production. And so is for feed industry because of its irreplaceable role, as a large amount of high quality steam is required for conditioning, pelletizing, ripening, extrusion cooking and drying etc.
Therefore, in a feed mill the design and the application of the steam system will directly influence the product quality and the production cost as well. At present, in China the average energy efficiency of industries is about 30%~40%, 15%~20% lower than the developed western countries. The continuously growing energy price all over the world makes it important for the feed mill to save energy from steam system.
Hereby we'd like to have a discussion about the composition of steam system and its rational application for readers' reference.
1. Steam features and application requirements1.1 Classification
Wet steam: steam which contains water held in suspension.
Saturated steam: steam in which gaseous water and liquid water are balanced under a certain pressure.
Superheated steam: steam which is the further heated saturated steam, it is of a higher enthalpy (i.e. contains more energy) and excellent. This kind of steam is not easy to be turned into water when releasing energy.
Generally, feed processing needs to work with a saturated steam. The quality of saturated steam plays an important role on the successful of production. A high quality steam should be capable of providing steam in proper amount and with proper temperature and pressure whenever needed, and it should be clean and dry without any air and water in suspension state.
For instance, wet steam will worsen the steam conditioning and pelletizing efficiency. As for pelletizing, steam quality would be the major factor that infuence the quality of pellet feed. According to production experience, the well adjusted steam system is able to improve the pellet feed quality dramatically, and the output as well as the energy efficiency is possible to be increased at least by 10%~20%, furthermore, benefiting from the reduced friction, the service life of the ring die can be prolonged greatly.
Besides, wet steam with suspended water will cause many damages to the steam system, such as generating water hammer, reducing the thermal efficiency of the equipments, reducing thermal energy in the steam, consuming more steam, polluting the steam system and the relevant equipments, increasing fuel and power consumption of the boiler etc. Therefore, it is essential to eliminate the source generating wet steam in production practice.
1.2 Features
Steam is compressible, so its features are related to pressure. As for the features of the saturated steam under different pressures, see Table 1.
Specific volume: the volume occupied by 1kg of steam under a certain pressure. It can be seen from the above table, as for certain mass of steam, the larger the pressure, the smaller the volume and the higher the density.
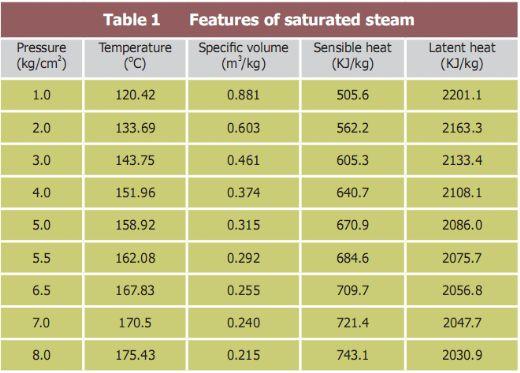
Sensible heat: the thermal energy that contained in 1kg of liquid water that changed from saturated steam under the same temperature and pressure.
Latent heat: the amount of thermal energy released from 1kg of saturated steam during the conversion of vapor into liquid under the same temperature and pressure.
Total heat: includes sensible heat and latent heat. From Table 1, we can see that the sensible heat is directly related to steam temperature while latent heat is related to steam pressure. As the pressure rising up, the steam temperature as well as sensible heat are increased, while the latent heat is decreased; [1]
As for the total heat, it is increased slowly as the steam pressure enlarged. Since the pressure of steam applied in a feed mill usually is from 2kg/cm2 to 8kg/cm, the change of the total heat is not so obvious.
2. A proper configuration of steam system
2.1 Steam application principle: delivering under a high pressure and applying under a low pressure the application of steam provides a controllable method for conveying energy from the concentrative, automatic, highly efficient boiler room to the jobsite.
Delivering steam under a high pressure It can be seen from the specific volume shown in Table 1, high pressure delivery has the following advantages:
- The reducible pipeline contributes to a fast flowing speed, little thermal loss, low pipeline cost, low maintenance cost and low labor cost;
- Low cost for heat pipeline isolation;
- Much drier steam obtained at the application point through depressurizing;
- The boiler will be more efficient when running under a high pressure;
- As the thermal storage ability of the boiler becomes stronger, it is easier to handle the load variability and to reduce the possibility of priming and carryover of suspended water.
Applying steam under a low pressure by reducing pressure, the higher latent heat contained in steam can be obtained, while the heat energy in condensate as well as the secondary steam will be reduced. The pressure released steam is of a higher dryness.
2.2 Pipe specificationsThe diameter of the pipeline in the steam system should be selected reasonably according to the pressure as well as flow rate of the steam to be applied (see Table 2). [2]
The steam flow rate is optional in the range of 15~40 m/s. It is recommended to select the flow rate of 25 m/s. Too big a pipe diameter will increase the installation cost, the thermal loss during conveying and the condensate generated, resulting in requiring more drainage devices or reinforcing the condensate draining capacity.
While too small a pipe diameter will increase the risk potential generated by the dramatically reduced pressure and the insufficient steam amount. It also acquires a faster flowing rate, which will cause higher noise and is more liable to generate water hammer and corrosion, and will damage the hardware.
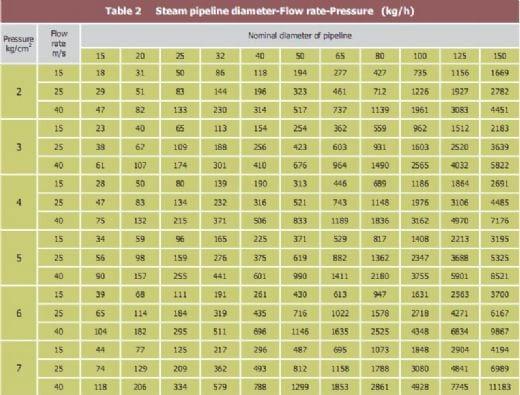
3. The control of steam pressure and temperatureSince different equipments need to work with steam of different pressures, pressure-relief valve is the indispensable element in light of the principle of high pressure conveying and low pressure application. The pressure-relief valves in common use are self-acting pressure-relief valve and pneumatic pressure-relief valve. The control range, precision as well as stability of the pressure are decided by the pressure-relief valve selected.
Generally, the self-acting pressure-relief valve is applied in a steam system which requires a large pressure difference, a large flow rate difference and a high precision of pressure control before and after pressure relief. It is widely used in feed mills. Pay attention to the following points when installing the pressure-relief valve because of its importance:
(1) Make sure the installation of pressure-relief valve is level, the steam flowing direction is in accordance with that arrow indicated on the valve body.
(2) The installation of the devices before pressure-relief valve: The pressure-relief valve should be protected from water and impurities, therefore, a filter with a 100 mesh screen and a steam-water separator and a steam trap unit should be installed before the pressure-relief valve; when changing the pipeline diameter, a connecting reducer should be installed to avoid generating condensate.
(3) The installation of the devices after pressure-relief valve: The size of the pressure-relief valve connector usually is larger than the pipeline before it while smaller than the pipeline after it. In order to avoid blockage in the pipeline, the pipeline before it and that after it should be selected properly according to the required flow rate and pressure.
(4) Too large a size of pressure-relief valve will cause troubles such as fluid erosion and "concussion" of the piping.
(5) If the pressure turndown ratio is larger than 10:1, two series-connected pressure-relief valves should be used.
(6)It is suggested to use two parallel-connected pressure-relief valves if the minimum flow rate is lower than 10% of the maximum flow rate.
4. Steam trap systemAs a key part of the steam system, the steam trap can drain condensate, air and non-condensable gas off the steam system, so as to ensure a high thermal efficiency and reliability of the system. A steam trap needs to be installed wherever condensate is generated, including the draining points of the main pipeline, the steam-water separator, the pressure-relief valve and the flow control valve etc.
The steam trap in common use can be divided into three types i.e. hot-static force type, hot-motive force type and mechanic type based on working principle. Each of the steam traps has its own suitable operation and working section in the steam system. In order to obtain the best separating and draining efficiency, it is very important to select the right type and size for the steam trap and then to install it correctly. For instance, a mechanical float ball valve with a high displacement is suitable to be installed behind the heat exchanger of a dryer, since it can continuously drain out condensate under a saturated temperature.
Compared to large equipments like boiler etc., the steam trap is too small to be looked at, that's why the type selecting is carried out in a disregardful way, which often brings about errors. For instance, some users choose and arrange their steam traps just according to the drain-pipe diameter of the steam using equipment but not the practical pressure difference and the condensate amount to be drained, thus resulting in that the drainage capacity of the steam trap is too large or to small, or such wastes in steam leakage or bypass that has to be provided, etc. [3]
The selected steam trap is related to the energy-saving efficiency of the steam system. Generally, the phenomenon like the temperature of heat exchanger cannot rise up or the working efficiency of the equipment declined indicates that the steam trap is blocked. And if there is any leakage of the steam trap, steam will flow into the condensate pipeline As what is researched, if there is a leakage hole as small as φ7.5mm in the steam trap, 110 kg of steam will be wasted in an hour under a 6-kg pressure, that will be a waste of 110 t of coal or 60 t of oil based on 8400 working hours a year averagely. [4]
A filter must be provided before the steam trap so as to prevent the steam trap from being damaged by impurities.
The steam trap should be installed in these places: every low point along the pipeline; tail ends of the main pipeline and the manifolds. There should be a certain slope on the pipeline before the valve which is closable and along the steam flowing direction. The selection of the water collecting tank should be correct. Make sure to use the eccentric reducer pipeline but not the concentric pipeline.
Steam should be supplied to the manifolds from the top side of the main pipe.
Install the filter at the side.
The steam-water separator should be installed in the boiler room and before the steam inlet of steam appliances, the pressure-relief valve, other control valves and flow meter. And all main pipelines should be heat insulated effectively.
5. Pipeline fittingsSteam pipeline, especially the main pipeline, should be in a proper size. To avoid generating water hammer, a pipeline system convenient for draining condensate is needed, that's the main reason for optimizing the pipeline layout. It is suggested to install the main pipeline with a gradient not less than 1% in the steam flow direction, thus the condensate can quickly move towards the drainage points under the combined effects of gravity and steam velocity.
The distance between two drainage points should be 30~50m, and a set of water collecting devices should be furnished for draining water.
In case a length of main pipeline cannot be installed as required (with a gradient of 1:100 in steam flow direction) or it must be installed overhead a height, it is a must to guide the condensate in a downward direction reverse to the steam flow. In this case, it is suggested to install the pipeline as follows:
(1) Adopt a pipeline with a little bit larger diameter to reduce the steam fow rate not higher than 15 m/s;
(2) The installed gradient of ascent pipeline should not be less than 1:40;
(3) The distance between drainage points arranged in this pipeline should not be larger than 15 m.
The branch pipeline should join the main pipeline from the top, so as to prevent condensate from flowing into the branch pipeline. It is not right to connect the branch pipe at the side of or under the main pipeline, that will bring condensation as well as solid particles, if any, into the branch pipe.
If it is necessary to reduce the diameter of steam pipeline, the section of the junction should not be a concentric circle but an eccentric circle, which the fat side faces downwards. As for the installation of steam-water separator, which can not only drain condensate off the pipeline but also separate the suspending scattered water drops from steam and diminish water hammer and its effect, a steam trap must be installed under it for filtering condensate.
6. Effective management of condensateUsually, only latent heat can be used by the steam appliances. After releasing latent heat, the steam will restore to saturated water in a same temperature, i.e. the condensate only has sensible heat. The higher the steam pressure, the more heat in the condensate drained. As for 1 kg of steam after completely condensing, 1 kg of water will be generated under the same pressure and temperature. A highly efficient steam system is able to reuse this condensate, otherwise, it will neither be able to save cost nor protect environment.
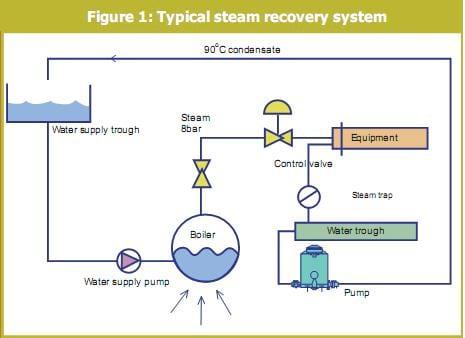
According to statistics, the heat in condensates generated under different pressure is about 15%~30% of the total heat in steam, which is a considerable heat source with excellent quality. If the steam condensate can be recycled effectively, it will save more than 20% fuel for the factory. [4]See Fig.1 Typical steam recovery system.
At present, the condensate reusing rate is very low in our feed mills, the reasons are as follows:
A. Due to incorrect selection or incorrect installation or bad quality of the steam trap, the steam appliances are unable to drain out condensate normally, the heating is impacted, and steam leakage problem is severe.
B. Problems like cavitations, water hammer and aired up etc. in pumping high temperature condensate cannot be well solved. Even if condensate is managed to be collected in an open- cycle way, temperature reduction caused by flash evaporation will take away a lot of heat.
C. Different steam appliances generate the condensate with different pressure, and different pressure in a same steam recovery system will cause problems. To solve the problems, users would like to drain out condensate of each steam appliance independently rather than intensively, which is not beneficial for the large-scale comprehensive utilization of condensate.
For the sake of solving the above problems, great importance has been continuously attached to the condensate recovery technology in recent years. Condensate recovery technology generally can be classified into open-cycle condensate recovery system and close-cycle condensate recovery system. More and more products and equipments related to condensate recovery system are produced. On the whole, however, the condensate recovery technology is developed in a decentralized manner and it is still in its infancy. Its application is not in full-scale and systematic at present.
7. Energy saving in a steam system
As for the energy-saving potential of each section in the steam & condensate system, see Fig.2. Energy saving can be carried out in the following aspects:
A. Check whether the design and the installation of the steam system are reasonable or not, to standardize the design of steam system;
B. Check the steam generating efficiency of boiler (the handling and control of boiler water supply, deoxygenization of feed water, boiler blow-down and heat recycling), examine and approve the fuel cost that used to generate steam, apply energy-saving technology to the boiler.
C. Measure the steam consumption of each process section, like conditioning, pelletizing, extruding and drying, etc., and check whether the condensate is drained normally or not.
D. To control the usage and consumption of steam reasonably and precisely.
E. Check the working conditions of each steam trap, drain out condensate effectively and collect high temperature condensate to the boiler.
F. Check the draining and recycling conditions of the whole factory.
G. Arrange the process flow as well as equipments reasonably, recycle and apply the secondary steam from high-pressure condensate.
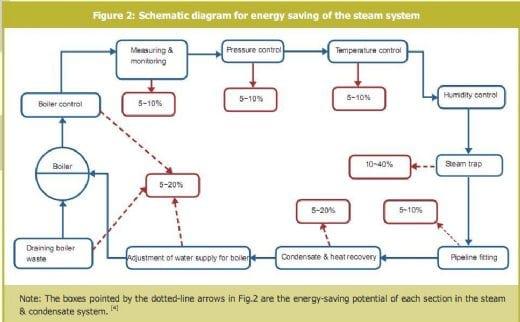
Saving energy from the steam system should not just be a solution for solving problems like "evaporating, emitting, dripping or leaking", but a system project which refers to factory energy management, standard design & installation of the steam system, proper start-up, stopping and operation of the steam appliances, and scientific maintenance etc.
This article provides some specific operating methods and suggestions on steam system and energy-saving, which may be helpful for your feed processing practice.
References:[1] Xie Zhengjun, Yi Bingquan. Steam and Conditioning [J]. Chinese Feed, 2002 (11): 26~29
[2] Yang Shuli, Jiang Weizhong. Factors and equipments affecting conditioning [J]. Feed Review, 2003(6):27~29
[3] Xiong Yiqiang. Steam conditioning in pelletizing operation
[C]. Proceedings of the American Soybean Association, 2005(24):12~24
[4] SPIRAX SARCO ENGINEERING (CHINA) LTD. The Steam and Condensate Loop book [M]. Shanghai, Shanghai Scientific and Technological Literature Publishing House, 2007.