As a critical part of a pellet feed mill, the ring die is not only directly related to pellet quality, but also to the maintenance cost of a feed mill. According to statistics, the cost of wear and tear of ring dies usually counts for 25% of the plant’s total maintenance expenses. As a result, it seems prudent to offer direction and instruction on the correct usage and maintenance of a ring die.
1 Correct installation
1.1 Requirements of installation position
During the pelletizing process, phenomenon such as nonuniform wearing on the ring die, obtaining non-uniform pellets, or bouncing up and down of the ring die are usually caused by an error in position during installation. These problems also worsen machine performance and pellet quality.
In addition, damage to machine parts (such as the main shaft bearings) is inevitable due to un-balanced stress caused by oblique mounting of the ring die and unstable running. In this connection, when mounting the ring die, the run-out amplitude of the ring die end face should be controlled within 0.2 mm. A dial indicator could be used for measuring the run-out, and an experienced operator is capable of measuring this visually by putting a piece of metal wire on the end surface of the die and then turning the die with his hands. In addition, it is very important to tighten the four bolts connecting the ring die to the pellet mill symmetrically and in pairs, so as to balance the ring die. A torque spanner should be adopted for bolt tightening to ensure that the same torque is applied on all four bolts. The torque applied must be in line with the die manufacturer’s requirement.
1.2 Proper locating pin
During normal operation a certain level of shearing force is placed on the locating pin by the die and vice versa. As a result, only a locating pin with proper strength can protect the die effectively, so the manufacture or purchase of the locating pin must be consistent with the technological requirement provided by the ring die supplier; it must be neither too long nor too short, neither too strong nor too weak.
1.3 Roller gap adjustment
Having correctly installed the die, it is necessary to adjust the gap between the die and roller to a proper range, which is vital for pelletizing production. Usually, proper roller gap is 0.1 mm to 0.3 mm. With an optimal gap, the rollers only hit high spots on the die when the die is turning at a low speed. Generally, for new die and new rollers the gap should be larger than the old gap. For a die with large openings, the gap should be larger than that with small openings, and for a formula with ingredients that are easy to pelletize, the gap ought to be larger than the one that is hard to pelletize. In addition, at the beginning of using a new die, especially one with small openings, a larger gap is favorable for easier running and to avoid rolling press on the die. Consciously accumulating experience for gap adjustment during production practices is good for a pellet mill operator’s professional growth. To increase throughput by minimizing the roller gap to zero or even negative clearance is inadvisable since the ring die may crack as a result of the high amount of stress on it.
2 Correct usage
2.1 Die flushing
When starting to use a new die, on the first run “flush” the die to remove the burr inside the die openings for 10~20 min, especially for those with openings smaller than Φ2.5 mm. However, in some cases, for a die with a rough inner opening surface it is necessary to mix 20~50% fine sand into the oily mixture for polishing.
Flushing a new die can help to achieve stable production and smooth palletizing. It can also improve pellet quality.
2.2 Ensure impurity-free material for pelletizing Matter such as stone, sand, iron and bolt mixed into the material to be pelletized will hasten the wear-out of a die, or even make it crack due to hard collision. In this respect, an effective cleaning process should be applied before pelletizing. In addition, it is necessary to regularly remove the tramp iron from the permanent magnet sleeve and the magnet device on the pellet mill feeder. If there are any hard impurities blocking the die holes, remove them by drilling or punching them out as soon as possible.
2.3 Die turning over For dies with a symmetrical shape such as a conic surface or a straight surface, turn the die over regularly after production for a certain period of time or a certain quantity of products to make wear of the die uniform, and to prolong its service life.
3 Maintenance Reasonable maintenance can ensure stable production and prolong the service life of a ring die. It is recommended that the following routine maintenance work be carried out regularly:
(1)For the sake of preventing acidic residue from blocking and corroding the die holes and to allow the die to start easily when put back into production, it is necessary to feed a non-corrosive oily mixture into the pellet mill to drive out the residues.
(2)After being used for a period of time, the working surface of the ring die will become uneven and the material guide angle of the die hole will become flat because of abrasion. At this time, the bumps on the working surface must be ground smooth and the material guide angle must be re-chamfered. Necessary restoration is important for prolonging the working life of a ring die. Make sure the lowest point of the working surface is 2 mm higher than the lowest point of the grooves cut in the face after restoration, and there should still be enough space for roller adjustment.
If not, then it is time to discard the ring die.
(3)Check the wearing condition of the driving rim and die flange for each die installation. The ideal clearance between die end face and the driving rim end face is 2~4mm
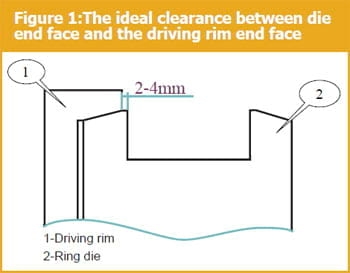
(see Fig.1). It can be measured by a clearance gauge. If there is no clearance between the two end faces or the die is trapped in the driving rim, it is time to replace the driving rim with a new one. Replacement in this case is necessary because the clearance between the driving rim and the ring die is uneven and the driving rim cannot hold the die tightly anymore. In addition, under this condition, the shearing forces that create stress on the bolts is uneven, which may either cause the bolts or the ring die to break. It is also required to have a clearance of 2~4 mm between the die and the die flange. If there isn’t sufficient clearance, the direct contact between the die and die flange will result in wearing at the bolts’ ends and where there is contact with the bolts’ ends.
(4)If the ring die does not discharge material due to blockage, the ring die can be soaked or boiled in oil to soften the material and then the material can be pushed out of the holes when reusing. If the blockage still can not be eliminated, drill out the material with an electric hand drill and then clean the die with oily material mixed with fine sand.
(5)The ring die should be laid in a cool, dry and clean place away from a corrosive medium. Mark the specification on it for easy management. The storing place must be humidity-proof to avoid corrosion and to ensure die performance and life time.
If the ring die is installed correctly, used reasonably and maintained effectively, it will give the pellet mill the best working performance. This, in turn, will result in reduced troubles, reduced production cost, increased product quality and higher profits.