Almost every miller in the world has considered introducing some degree of automation to the cleaning houses, mills and packing plants at some stage and many have been very successful. Sadly though, I also hear stories of things that went wrong, mainly because the automation projects were inappropriate for the mill in question.
Not every mill lends itself to full automation. It is fruitless, for example, to attempt to fully automate an old, outdated mill, built before automation was available, since the machinery, particularly the rollermills, does not lend itself to the modifications needed for the application of “hands free” technology. Automatic engagement and disengagement, for instance, can be applied to old rollermills but these modifications require a great deal of precise engineering work and reconfiguration of parts, possibly the introduction of pneumatics and hydraulics depending on the supplier, and when this is done in situ instead of in a specialist workshop, the end result can be unreliable and the desired objective cannot be achieved.
Clearly it is better to apply new technology to new equipment. When we buy new equipment, we expect to get the best on offer - and there is a lot on offer these days.
The principal milling engineers have their own bespoke automation packages that are now well tried and tested. Buhler, as one would expect, has an excellent package. Their “Wincos” system has various levels of control that can be applied to any area of a plant - intake, wheat blending and cleaning, milling and finished product routing. The system incorporates extraction monitoring, mill start up and shut down sequencing and the usual automatic suspend and report procedures when alarm conditions arise. This is a robust and excellent package which can be applied in almost any environment, even where labour skills are low and where mills run manless for long periods.
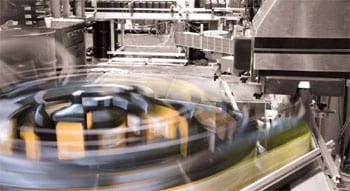
Satake, for example, has its own system and can write the software to be specific to each individual mill, an option that some millers prefer over more rigid systems. Particularly where the project is small or independent of the main milling section, this bespoke approach has distinct advantages. However, it is not always the pioneer who reaps the rewards of new developments and while these systems can be very flexible, access to a good site engineer for software maintenance is necessary. Satake provides excellent back up for its systems and with today’s telecommunications and software access by modem, help is only a phonecall away.
Before considering introduction of any automation, either in the mill, cleaning house or packing department, there are several items to consider. First, why do you want to automate? The answer invariably involves labour issues or raw material costs.
Personally, I do not categorize simple extraction monitoring as automation, although I know several millers who do. I strongly recommend every miller to have such a facility, on condition that they do not just install it and look at the statistics, without doing anything with the data. I have seen many millers admire their extraction monitoring facilities when they would do better by getting out in the mill, spending time on the rollermill floor and improving their results rather than admiring a graph on the wall.
Introduce automation to reduce labour
We invariably want to introduce automation to reduce labour and this is easily achievable in many mills. There comes a point, however, where the desire to become a manless operation becomes a move too far which is disproportionately expensive. I believe we shall always need at least one miller at each site, to monitor operations. An automated system will run the plant but it will not always pick up on minor plant operation details. It can only operate your mill as you tell it to. Each harvest presents new challenges and without the input of an experienced miller to adjust operating systems and parameters, results can be severely affected. I therefore advocate at least one miller present at each location.
Automation from a raw material perspective offers, in my opinion, more to be gained financially than from the labour savings that most millers focus on. Raw materials are the most expensive of all mill inputs and proper control of blending, monitoring of protein levels and controlled, accurate addition of gluten and other additives are all areas that can impact the bottom line significantly and quickly.
Most of the milling engineers have recently developed their own systems for monitoring parameters such as protein and moisture, mainly by online sampling and near infrared testing. These facilities, linked to loss in weight feeders in both the wheat blending and flour additives areas, can really produce big dividends, particularly in mills where the main product lines are high protein, high value flour types.
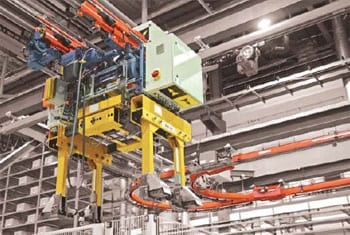
Today’s systems are very reliable and accurate
Calibration of these systems was an issue when the online analysers first became available but those problems have now been eradicated and today’s systems are very reliable and accurate. Where a wide range of flour types are produced from a wide range of different wheats, then the results are clearly not as accurate as, for example, in a soft wheat facility milling a single variety.
As raw materials rise in price, the importance of extraction is more than ever prominent. An increase in ash or colour can be tolerated if extraction can be increased proportionately. The importance of thoroughly cleaning wheat and removing all broken grains is tending to diminish in many mills. Trieur indented cylinders and disc separators are often being bypassed and screenrooms now comprise just a separator, dry stoner and scourer prior to the tempering equipment. Tempering stations are fully automated in almost every mill and the accuracy of tempering, invariably tied to moisture monitoring equipment, is as reliable and accurate as it has ever been.
Full automation is not a practical option due to the age of the machinery
While most millers tend to mill hard wheat and soft wheat separately these days, to avoid the compromises that swing milling demands, there are still some older mills, particularly in the USA, that mill extremes of hard and soft wheat. These mills tend to be quite old and full automation is not a practical option due to the age of the machinery.
In such circumstances, there is much to be gained by selective automation. Simple monitoring of plant operations, routing of products to the correct bins, monitoring of individual groups of equipment such as conveyor and rotary airlocks by use of rotation sensors, collective displays of machine loadings, roll amperages, pneumatic fan loadings, blower pressures, et cetera, can all help the miller operate the plant more efficiently, especially in large mills where high volume provides a speedy return on a small investment.
In some cases, a partial investment in new plant can prove beneficial. For example, it may be desirable to avoid break rolls continuing to grind, in order to protect the roll fluting when feed runs off. But it may be unnecessary to disengage slow moving tail end reduction rolls at the same time as the break rolls. Investing just in replacement break rollermills, in conjunction with partial automation, may produce a viable option. Phasing-in automation can enable both operatives and management to become familiar with the technology and its effects before a major plant automation programme is undertaken at great expense. Automating a site by degrees is a choice that can be suitable in many cases, especially in older facilities.
Outside the main milling complex
There are several areas outside the main milling complex that can benefit from automation. Most noticeable is the packing house, where the new- generation packers are now fully automated. Provision of bags, and removal of the finished pallet of flour or bran from the end of the packing line, remain manual when product is to be placed in storage, but all operations in between are now fully automated. This helps to keep things moving at an acceptable rate. When coupled with direct vehicle loading, as in some of the larger African mills, packing rates can be quite outstanding compared to manual operations. So too is the control of inventory, an issue that is significant in many mills in the developing world. Several mills have installed fully automated packing and loading stations simply to eliminate theft of product at the loading stage.
Automated maintenance programmes can also be valuable. Buhler’s WINCOS system as an addition to the “Plant Care” package which provides the maintenance engineer with all he requires to keep the mill operational and well maintained. Other engineers offer similar packages but they tend to be tailored to each mill, compared to Buhler’s easy-to-use standard package. Satake provides an on-site maintenance service in the United Kingdom and Ireland and its maintenance programmes are linked to its own service crews.
Coordinate the operations of an entire organization
At the ultimate level, there are fully integrated automation and management systems that apply to the whole business. Systems such as those offered by SAP, for example, have been adopted by several British flour milling companies. These systems coordinate the operations of an entire organization, from product sourcing through to final customer end use.
In the animal feed industry, where the range of raw materials, the complexity of suppliers and the wide variety of raw material origins, all have to be taken into account during operations, there are many companies offering fully integrated plant management and accounting packages. These systems take inputs from suppliers and customers, as well as from key areas of the plant, and monitor inventory levels at the mill, at the customers’ premises and in transit. The goal is to maximize the use of assets and facilities. The cost of these systems is significant and the purchaser really needs to be sure that his company will benefit from such an installation. Size of operation is critical as there must be sufficient volume passing through the site, at the appropriate and relevant value, to warrant the expense and generate an adequate return. There are few companies outside Europe considering this all-embracing automation and recording technology.
One advantage is that the customer becomes an integral part of the business since co-operation between supplier, miller and customer is needed to take full advantage of these systems. Mills that operate as part of a group, supplying flour to their own bakeries and other end users within the same group, benefit most from this technology.
As raw material prices reach record levels, the cost of maintaining high inventory has become prohibitive. Where control and organization of supply chains is increasingly important for profitability, a simple raw material purchasing package can prove invaluable, especially when it is linked to a transport management system. It is surprising how few millers have computerized their supply chain and transport fleet. Many companies still control these areas of their operations in “long hand” and are missing significant opportunities to improve revenue.
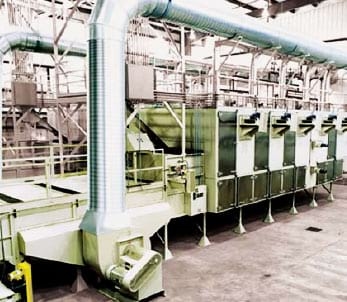
From simple extraction monitoring to full control of large companies
With so many automation systems on offer today, the miller can choose what he wants. There is a system available for all scenarios. From simple extraction monitoring to full control of large companies, anything is possible. But there must be a good reason for automating and sound financial judgement is required. In my own experience, all the suppliers of automation products are cautious to provide only what can be justified, rather than loading up the quote with everything that is available, necessary or not.
It can be difficult decide how fast to depreciate automation technology. Most millers have now settled on five to ten years, whereas three years was the standard when automation projects were popular in the 1980s. The practical application of new technology has tended to slow down in our industry and five years now seems to be an appropriate period before renewal. Millers want to improve on their operations and it is this desire to improve performance that drives technology renewal, not operational failures or unreliability.
In the milling industry we seek to provide an end-product fit for purpose at the best possible value. Automation enables us to do this better than our forefathers but it is easy to get carried away by the possibilities and overlook what is really necessary. Buyer beware!