INTRODUCTION TO PELLETING
The Purpose of Pelleting
Pelleted feeds have been defined as “agglomerated feeds formed by extruding individual ingredients or mixtures by compacting and forcing through die openings by any mechanical process”. Basically, the purpose of pelleting is to take a finely divided, sometimes dusty, unpalatable and difficult-to-handle feed material and, by using heat, moisture and pressure, form it into larger particles. These larger particles are easier to handle, more palatable and usually result in improved feeding results when compared to the unpelleted feed.
Pellets are generally formed with diameters from 10/64” to 48/64” and will be somewhat longer than the diameter. A small part of the production of large pellets, 32/64” and above in diameter, is produced in other than cylindrical shapes; they may be triangular, square or oval and, in some cases, may exceed the maximum dimension indicated above. The largest diameter usually found is rarely greater than 1-1/4” to 1-3/8”. In most cases where particle sizes smaller than 10/64” are desired, it has been found to be more satisfactory from the standpoint of economics to produce a 10/64” or 12/64” pellet and reduce it into the desired particle size by means of crumbling.
Almost all livestock feeders agree that animals make better gains on pelleted feed than a meal ration. The most logical reasons are that (a) the heat generated in conditioning and pelleting make the feedstuffs more digestible by breaking down the starches, (b) the pellet simply puts the feed in a concentrated form, and (c) pelleting minimizes waste during the eating process. When pelleted feed is fed, each animal receives a well-balanced diet by preventing the animal from picking and choosing between ingredients. Tests have shown that most animals, if given the choice between the same feed in pellet or mash form will prefer the pellets. By combining moisture, heat and pressure on feed ingredients, a degree of gelatinization is produced which allows animals and poultry to better utilize the nutrients in these ingredients.
Feed conversion will be improved. These advantages are particularly noticeable in the broiler industry.
The feeding merits of pelleted feeds over the mash form have been repeatedly demonstrated in the feeding of swine. One state college reported the results of an eight week swine feeding test in which pelleted feed performance was compared against the same feed in mash form. This test gave the following results:
All animals, on the average, consumed the same amount of feed (5.06 lb. per day of pellets vs. 5.02 lb. per day of mash), yet the pellet fed pigs gained a quarter of a pound per day more weight than did the mash fed animals (1.76 lb. vs. 1.54 lb. of gain per day). Since the pellet fed hogs gained more while eating the same amount, it is evident that pelleting causes the feed to be utilized more efficiently by these animals. This is shown in the comparison of the average amount of feed required for each pound of gain. The pellet fed hogs consumed 2.87 lb. of feed per pound of gain while the mash fed hogs needed 3.27 lb. to make a pound of weight gain. Pellet fed hogs not only gain faster but they do it with less feed for each pound of weight increase.
Pelleting prevents the segregation of ingredients in a mixing, handling or feeding process. By feeding a pelleted feed, the animal is more apt to receive a totally mixed ration than one that has separated through these processes. It also prevents waste. Bulk density is increased, which enhances storage capabilities of most bulk facilities. Shipping facilities are also increased, thereby reducing transportation costs. This is particularly evident in such fibrous ingredients as alfalfa, gluten feed, oat hulls, rice, bran, etc.. A better flow and handling characteristic of pellets is one of the least mentioned advantages but probably the most important, particularly as it relates to dairy farmers.
In 1978, there were 9,977 feed mills registered with FDA producing 78.2 million tons of feed annually; about 60% is pelleted. Not all feed mills, of course, are equipped to pellet feeds. In 1958, these mills produced 40 million tons of feed and about 55% was pelleted. In 1968, about 70% of all commercial poultry feed produced in the United States was pelleted. In the Midwest, almost 80% of all manufactured feed is pelleted, crumblized or cubed. The process of producing feed pellets can roughly be described as a plastic molding operation of the extrusion type. Feed ingredients are made up of various compounds such as proteins, acids, sugars, fibers, and minerals. These products can be softened (conditioned) by the addition of heat and water. When sufficiently controlled compression is applied to the “conditioned” feed ingredients, they will form a dense mass, shaped to conform to the die against which they are pressed. When the heat and moisture is again withdrawn (dried and cooled) as to withstand moderately rough handling without excessive breakage and has retained or enhanced its nutritive value.
In modern feed mills, the ingredients are usually stored in bins above a weighing system composed of one or more scales. Those ingredients which are of coarse texture, such as whole grains and other fibrous materials, are ground into a fine meal to facilitate the pelleting and mixing process. Weighted quantities of each ingredient (either as a batch or continuously) are thoroughly mixed (either in a batch mixer of a continuous flow mixing unit) and then conveyed to a bin above the pellet mill. Some manufacturers have installed systems to grind all of their premixed materials prior to entering the pellet mill. Data is not available which indicates this has been an advantage or disadvantage on a consistent basis as far as durability is concerned.
Terms Used in Pelleting
The following terms are often used to measure the efficiency and quality of pellet mill operation.
Friction is the difference in temperature of the feed entering the pellet mill die and the pellet being discharged from the die. The difference reflects the mechanical energy required to produce a pellet. There are several inherent factors that can affect friction:
1. Moisture addition to the feed ingredients (refer to Graph #1). The amount of moisture (steam and/or wet molasses and/or water) added should cease when the friction plateaus. Moisture added beyond this point will cause the pellets to disintegrate and not increase production or quality.
2. Conditioning.
3. Ground screen size of feed ingredients.
4. Physical properties of the feed ingredients, such as minerals, water soluble ingredients, fiber content.
Other factors relating to friction are die size in terms of hole diameter and thickness. High friction (over 30°F) results in reduced die and roller life, as well as increased bearing and gear maintenance. Fines are the materials that result from pellets disintegrating due to poor quality or mechanical attrition. Fines are a function of moisture and high friction (see Graph #1) or oversized feed ingredient particles or poor conditioning.
Graph 1 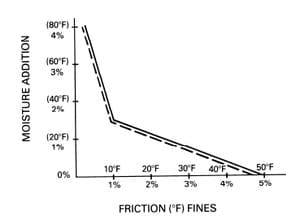
Die Size
3/16” x 2”
Die Speed - 316 RPM
Shrinkage is the loss of weight of the original feed ingredient after pelleting. This loss is basically due to lack of moisture addition and high friction (refer to Graph #2). High levels of friction due to lack of moisture addition results in higher pellet temperature entering the cooler; and thus, more moisture is “flashed off”. (This will be discussed in greater detail in the section on “Evaporating Cooling”.)
Graph 2
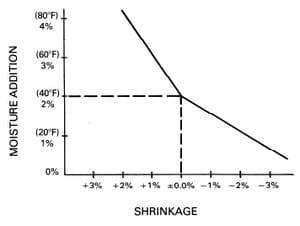
Basically, the break-even point is 2% moisture addition; therefore, anything less than 2% moisture addition results in shrink. On the other hand, over 2% moisture addition will result in a gain. Normally, of the gain exceeds 1.5% of the pellets will disintegrate. Other factors that enhance gain are wet molasses and water additions.
Die Selection is a function of the feeds to be pelleted. A typical selection of a feed plant follows:
•Water soluble ingredients - 5/32” x 1-1/2”
•Corn - 5/32” x 1-3/4” - 2”
•Grain and Grain By-products - 5/32” x 1-3/4” - 2”
•Cubes - 3/4” x 5”
This is based on production rate, die friction, and quality. In this particular case, corn and grain and grain by-products pelleted on a 5/32” x 1-3/4” operated at friction of 2-10°F and the mill operated 60-70% mill load, at rates of 8-22 ton; the quality was 5-10% fines. Die selection is a function of quality and production rate.
Die speed (RPM) is a function of the feeds to be pelleted, for example, feeds containing fat or 50-60% corn. Perhaps it is more judicious to refer to peripheral speed of a die rather than RPM. An exaggerated example is producing a 3/4” cube at 317 RPM with a 22” die vs. 171 RPM with the same die. Also, comparatively poorer quality pellets would be adversely affected at higher peripheral speeds.
Generally speaking, a peripheral speed of 1800 fpm is ideal under normal circumstances. This is measured at the outside diameter of the die.
EQUIPMENT USED IN THE PELLETING PROCESS
The Pelleting System
The pelleting system is composed of several different machines designed to most efficiently accomplish the pelleting task. A typical system arrangement with equipment names is shown in Figure 1. While we will give more detailed information relative to the function of each machine later, it would be advisable to first learn the names and relationships of these major processes.
After the feed has been mixed and before going to the pellet mill it should go through a scalper. This removes everything such as metal (ferrous and non-ferrous), stones, string, paper, wood, feed lumps and gives a dressed feed into the bin above the pellet mill. A pellet mill is not designed to pellet these materials, let alone the animal stomach to digest them.
The pelleting process starts with a bin (Figure 1, Item 1) in which the mixture of mash is stored. From there, the mash will flow by gravity into the pellet mill (Figure 1, Item 2). This machine is usually located on the ground or main work floor level. The hot, extruded mash (pellets) flows by gravity into a cooler (Figure 1, Item 3) where it is held for three to six minutes while being cooled and dried by a flow of air. The air is drawn through the mass of pellets and passed into a dust collecting device, such as a cyclone collector (Figure 1, Item 7). The dust from the outlet of the collector (Figure 1, Item 8) is returned to the pellet mill to again be compacted into a pellet.
From the cooler (Figure 1, Item 3), the product flows through or around a pair of crumble rolls (Figure 1, Item 4). If we wish to produce a relatively fine product, about the size of cracked corn, then the pellets are passed between the crumble rolls to be crushed (cracked) to a smaller size. If we wish to retain the full pellet size then we flow around the crumble rolls. From the crumble rolls the product flows into a bucket elevator (Figure 1, Item 5) to be raised to a higher point in the structure where the shaker (Figure 1, Item 6) is located.
The shaker separates the product into various sizes by passing the material over several screens. Each screen is of a different opening size. This separation permits the desired product to be separated from the larger or smaller particles while being delivered to the finished product bin. The “overs” can be returned to the pellet mill for repelleting or, in the case of crumbles, to the cooler, and in turn through the crumble rolls for recrumbling. The fines or smaller material can be routed directly back to the pellet premix bin and reprocessed through the pelleting system.
Supply Bins
The supply bin or bins must be adequate to store a sufficient quantity of feed immediately ahead of the pellet mill to provide not only continuous operation of the pelleting unit but also continuous operation of the mixer which provides mash to the pelleting unit. Other factors in the feed mill design may dictate a need for greater available tonnage ahead of the pellet mill than will be discussed here.
Generally speaking, the bin supply immediately ahead of the pellet mill should consist of at least two bins, each of a capacity not less than three times the capacity of the batch mixer used to supply feed to the pelleting unit. A bin installation of this type will usually result in an efficient operation, both from a mixing and pelleting standpoint, and is the minimum. The maximum will be determined by factors other than the pelleting installation. These supply bins should be constructed so that there will be no bridging or surging. Variations in the feed cause objectionable variations in the operation of the pellet mill. Generally, these bins can best be constructed of sheet metal. Rectangular or square construction lends itself to the best installation, however, round bins may also be used.
While several pages might be devoted to the subject of hopper design, it is sufficient to say that the slope of the hopper sides should never be less than 60°. As many vertical sides as possible should be incorporated into the design. Many feed mill engineers have used the excellent, though more costly, design of having a small feed supply bin fed by start-and-stop conveyors from the main supply bins. The small supply bin may have a capacity of less than 1,000 lb. and should be equipped with bin level controls.
Pellet Mills
Thoroughly mixed ingredients, now called “mash” or “meal”, are allowed to flow by gravity into a flow rate regulator called a “feeder” (Figure 2, Item 1).
Figure 2 - Component Parts of a Conventional Pellet Mill
The feeder is generally a screw-type with some variation in flight arrangement, such as single flight, double flight, full pitch or one-half pitch to accommodate varying conditions. It is equipped with some type of speed control, such as a variable speed electric drive. The purpose of the feeder is to provide a constant, controlled and even flow of feed to the mixing and pelleting operation. Any variation in this flow results in poor conditioning and a variable product.
This feeder delivers a constant and prescribed amount of the “meal” to a “conditioning” chamber (Figure 2, Item 2). Here the mash is thoroughly mixed with steam (heat and water) and other desirable liquids, such as molasses.
A mixer is provided in order to properly condition the feed. Conditioning is almost universally accomplished by the addition of controlled amounts of steam. Addition of steam supplies moisture for lubrication, liberates natural oils and, in some cases, results in partial gelatinzation of starches. Uniform conditions at this point are extremely important for optimum results. Further, this mixer can be used for the addition of up to 6-8% molasses without special attachments when properly equipped. Mixers are supplied in low speed (up to 125 RPM) and high speed (125-500 RPM) models.
The conditioned mash then flows by gravity into the pellet mill die chamber (Figure 2, Item 3) where rollers press the softened mash (Figure 3, Item 1) through the holes in a circular die (Figure 3, Item 2).Stationary knives (Figure 3, Item 3) located outside the circular, rotating die cut off the shaped, dense pellet at the proper length.
Figure 3 - Typical Die & Roller Assembly used for Producing Pellets
Most modern pellet mills used a ring type die turning about two fixed rollers, with the die and rollers mounted in a vertical plane. A few mills are built with the dies and rollers in a horizontal plane with the rollers turning within the stationary die. Obviously there are advantages to each type of construction but more mills made today are of the vertical type. In the pelleting unit, the conditioned mash is forced through holes in the die by roller pressure. Die thickness is a factor in the production of high quality pellets and must be accurately balanced with the formulation and conditioning. Starting with 24/64” pellets and above, some variation in the amount and depth of taper incorporated into the entry of the holes in the die may be necessary. Numerous other special entries are used in instances where satisfactory pellets cannot be produced with standard entry and taper.
All pellet mills incorporate some type of speed reduction device, since die speeds are always less than the conventional motor speeds. In some cases variation in die speed is desirable to produce optimum results on individual groups of feeds. Speed reduction devices in use today include direct coupled gear trains, V-belts, cog belts and combinations of belts and gear trains. Currently, mills are being built with speed change mechanisms. Usually these speed change mechanisms are in the form of gear shifts or two-speed motors. This provides two die speeds to secure optimum results when a wide range of feeds is produced.
Most pellet mills are installed with an electric motor as the prime mover; however, internal combustion engines are sometimes used. When internal combustion engines are used the horsepower rating should be at least twice that of the electric motor normally used. The pellet mill and motor are usually mounted on a common base to maintain alignment of the pellet mill and motor and to provide a rapid, simple and efficient method of installing the equipment. Although it is not a part of the pellet mill, an ammeter should be included as part of the electrical system. This will allow the operator to adjust the feed rate to secure the maximum capacity of the mill without overloading the motor.
Pelleting Dies
Considerable attention must also be given to the various types of dies used by the feed manufacturing industry. Die thickness and hole size varies with the type of product to be pelleted as stated previously. Relieved dies have an enlarged diameter on the discharge side of the hole. Relief length is the distance of the die hole which has a greater diameter than the rest of the hole.
There are basically four types of dies available:
•Standard Die All the holes have the same effective thickness
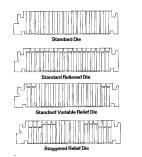
•Standard Relieved Die All holes have the same effective thickness, but the discharge side of the hole is enlarged to a depth of 1/4” (relieved). The primary purpose for this die is to add strength to the die without making the hole depth thicker.
•Standard Variable Relief Die All holes are the same except the two or three outside rows of the die, which are relieved by 1/4”. The number of rows to be relieved vary by die manufacturer. Certain products to be pelleted will have a tendency to squeeze out to the side of the die. When this happens the two or three outside rows become plugged and as much as 25% of the die effectiveness is lost.
•Staggered Relief Die This die basically serves the function as the standard variable relief die except that the two or three outside rows are relieved 1/2” and the next two or three rows are relieved 1/4”.
Coolers
From the pellet mill chamber, the pellets normally flow by gravity into a device for cooling and drying the pellets. Pellets will leave the pellet mill at temperatures as high as 190°F and moisture contents are high as 17-18%. For proper storage and handling of the pellets, their moisture content must be reduced to 10-12% and their temperature to about 15°F above atmospheric temperature. This is to be accomplished by passing a stream of air through a bed of pellets. This evaporates the excess moisture, causing cooling both by the evaporation of water and by contact with the air. Air doubles its capacity to hold water with every 20° rise in temperature. In other words, the warmer the air the more moisture it should remove from the processed pellets.
Most coolers fall into two classes: vertical and horizontal. The vertical cooler is made up of two columns of pellets, side by side, held in position by wire mesh on both sides. Air is drawn through the column of pellets by means of a fan.
Figure 4 - Component Parts of a Vertical Pellet Cooler
1. Hopper and level sensing device to maintain a supply of pellets ahead of cooling columns
2. Cooling columns
3. Air chamber
4. Discharge drive gate motor and controls
5. Discharge gates
6. Centrifugal fan
7. Fan drive motor
The operation and construction of a typical vertical cooler is simple. The pellets flow (usually by gravity) from the pellet mill to fill the columns (Figure 4, Item 2) and the hopper (Figure 4, Item 1) above the columns up to the level sensing device near the top of the funnelshaped hopper. Pellets resting in this hopper act as an air seal that forces the cooling air to pass through the column of pellets to reach the fan (Figure 4, Item 6). When the amount of pellets in the hopper reaches the level sensing device it starts the discharge gate drive motor (Figure 4, Item 4) which turns the discharge gates (Figure 4, Item 5) at the bottom of each column, thereby lowering the level of pellets in the cooler to accommodate the continuous flow of hot pellets from the pellet mill. While the flow of pellets through the columns is being automatically related to exactly the production rate of the pellet mill, the fan (Figure 4, Item 6) is drawing air through the columns of pellets into the air plenum chamber (Figure 4, Item 3), discharging this feed dust laden air to a cyclone “dust” collector.
During a production run, an accumulation of feed dust may build up in the plenum chamber. Therefore, before the next run the dust accumulation should be cleaned out to prevent contamination.
The horizontal cooler is similar in operation to the vertical cooler even though its construction (shape) is significantly different. Where the vertical cooler uses two columns of pellets moving down, the horizontal cooler has a “bed” of pellets resting on a perforated steel or solid pan moving belt which is slowly being passed through the cooling air stream. The major advantage of the horizontal cooler over the vertical cooler is that the horizontal cooler, with its moving bed, will mechanically move and discharge the pellets. This provides the positive flow action which is needed when processing pellets which, for some reason, may be prone to congeal (stick together). In a vertical cooler, pellets which are “sticky”, such as those with a high molasses content, are likely to be “glued” together during or due to the drying and cooling action, preventing their normal flow through the unit.
Figure 5 is an illustration of a typical horizontal cooler. These units are often found to be two high. The purpose of this is to conserve floor space by utilizing two short units rather than one unit which is twice as long. The pellets normally flow by gravity into a device which spreads the pellets to a uniform bed depth across the belt (Figure 5, Item 3). This spreading device can be an oscillating feeder (Figure 5, Item 1) or it can be a surge hopper with a discharge gate having a fixed opening to allow the belt to be filled with pellets to a specific depth. A level control on the inlet hopper is used to sense the accumulation of pellets, starting and stopping the cooling belt drive (Figure 5, Item 5). This type of control is similar to the operating control on the vertical coolers. As the product is conveyed by the perforated belt, a suction fan draws cooling air through the air inlets (Figure 5, Item 4) which are holes cut into an airtight housing to direct the air to a point under the bed of pellets. The air travels up through the bed and into the air plenum chamber (Figure 5,Item 3) and then to the fan and/or a “dust” recovery system. The length of the horizontal cooler and the speed of the belt drive determines the duration time of the cooling cycle. The width of the cooler and depth of the pellet bed determine the production rate (capacity). The depth of the bed, the width of the cooler, the size and length of air pipe, and the size and type of dust collection equipment determine the fan requirement.
Figure 5 - Component Parts of a Horizontal Pellet Cooler
Crumble Rolls
For the production of pelleted feed particles smaller than 10/64”, it is generally considered desirable to use a crumbling process. In this process, small pellets are broken between two corrugated rolls. The set of powered corrugated rolls is usually placed directly below the cooler as this eliminates the need for an additional rate controller.
The components of a typical crumbling roll are illustrated in Figure 6. It is composed of a heavy steel frame and housing (Figure 6, Item 1). The corrugated rolls (Figure 6, Item 2) are usually 8-12” in diameter and are up to 72” long. The corrugations are normally spaced at 6-12 per inch. Figure 6, Item 3 shows the roll spacing adjustment. This controls the sizing or degree of crumbling of the product. Figure 6, Item 4 is the by-pass valve which directs the pellets around the outside of the rolls when one prefers not to crumbles the product.
Figure 6 - A Typical Crumbling Roll
Shaker
From the crumbling device, the product (either whole or crumblized) is delivered to a screening device (shaker). This is used to extract the undesirable undersized portions of the product from the correctly sized material. The undersized product is returned to the pellet mill for repelleting and is referred to as “recycle” or “fines”.
When a crumblized product is being made, it is likely that some pellets would not be properly broken to a specific size. These oversized particles are also removed by screening and returned to the original crumbler roll for reprocessing and again they are screened. Approximately 25-30% of fine materials will be returned through the crumbling process for reworking.
The majority of the screening devices used today are oscillating, vibrating, or gyrating wire or metal screens having the appropriate opening sizes. An example of an oscillating pellet screen (or scalper) is illustrated in Figure 7. These units are composed of a steel or wood frame (Figure 7, Item 1) from which the screen (Figure 7, Items 4 and 5) are supported or suspended. The screen frames are being oscillated by an eccentrically-weighted drive unit (Figure 7, Item 2) powered by an electric motor (Figure 7, Item 3).
Figure 7 - Component Parts of an Oscillating Pellet Scalper
Pellet Elevating Systems
The correct sized product from the shaker is now in its finished form and ready for packaging or shipment. In many mills the pellet shaker is placed on the upper floors of the structure to permit the screened product, the oversize crumbles and the fines to flow by gravity to their correct destination. This requires that the unscreened pellets be conveyed vertically (elevated) from the cooler to the shaker. In other cases the shaker is placed below the cooler and the sized finished product is conveyed to the packaging or bulk shipping point. In either case, an elevating system (vertical conveyor) is usually required. This can be done mechanically by means of a bucket elevator (also called a “leg) or it can be done pneumatically by an air conveying system. Air systems are sometimes used to convey hot pellets because they are not as subject to the buildup of hot, wet material as is a bucket elevator. Usually bucket elevators are used because they are less expensive to install, maintain and operate.
FEED INGREDIENT CHARACTERISTICS
Various ingredients have characteristics that require different forms and levels of treatment during pelleting. Familiarity with these characteristics allows the operator to know in advance what effect moisture, pressure and heat will have upon individual feed formulas and anticipate what he can do to pellet the feed in the most efficient way.
Feed and ingredient characteristics are determined by the following factors:
1. Protein
2. Density
3. Fat
4. Fiber
5. Texture
6. Starch or carbohydrates
7. Moisture
Each feed or ingredient has a unique characteristic depending upon the variance of one or more of these factors. Each factor has a certain latitude of variance before the characteristic of a feed or ingredient is changed. For example, change the protein of 48% soybean meal by 0.2 of one per cent and it is still considered 48% soybean meal. But, if the protein was analyzed as 46%, or 2% less, the ingredient would not be considered 48% soybean meal.
While ingredient suppliers are, at times, striving to keep these ingredient factors constant so that their quality will not vary, they have also, through modern technology, been able to reduce the amount of starches, fats and oils from these products. While these improvements normally enhance the supplier’s primary products, we in the feed industry find it increasingly difficult to pellet these ever-changing products.
The quality of pelleted feed will vary as the factors of ingredients vary. In order to keep pellet quality constant, ingredient characteristics or quality must be consistent, or compensating adjustments made. Figure 8, called the Pelletabilty Chart, lists common ingredients used in feed. The chart can be used to help predict the rate that each ingredient will pellet. The column headed “abrasiveness” will give an indication on how this ingredient will affect die life. Each feed formula can be analyzed using this chart to give an indication of its pelletability.
Many times pelleting rates and pellet quality are reduced, because it is not always possible to control the ingredients that make up a formula or make compensating adjustments. While some least cost formulation programs do set standards for pellet quality specifications, ingredient costs continue to be an overriding factor when formulating the final product.
Protein & Density
Normally, the production rate or pellet quality of a formula can be predicted when the factors of protein and density are considered. Ingredients with high natural protein will plasticize under heat, which will cause good quality pellets. Ingredients or feeds with high density have high production rates.
If an ingredient or feed is both high in natural protein and density, the high production rates and good pellet quality can be expected. When low protein and high density are the factors, high production rates and poor pellet quality can be expected. One example of this type of ingredient is ground corn. At the other end of the spectrum, an ingredient or feed that has low protein and low density should produce a good quality pellet with a poor production rate. Some examples of this type of ingredient are alfalfa meal, ground corn cobs, cottonseed hulls and corn gluten feed.
The bulk density of a formula is an important factor in determining the rates a pellet mill will produce. You will get less production of a light fibrous material, such as alfalfa meal which has a bulk density of 17 lb. per cubic foot, as opposed to cottonseed meal which has a bulk density of 40 lb. per cubic foot off the same 100 HP pellet mill (Figure 9).
Figure 9 - Small Particles Increase Bulk Density of Light, Fibrous Materials, reduces work of pellet mill in densifying lighter materials and permits faster running.
If you can reduce your particle size for pelleting, the small particles, fine grind will result in:
1. Improved quality
2. Increased production rate
3. Increased bulk density
4. Greater horsepower efficiency
5. Longer die life
A better quality and higher rate results from particle size reduction because the steam penetrates the smaller particles through to the core, making them soft and pliable. However, due to the retention time in the conditioner, the steam is unable to penetrate the larger particles completely, leaving the center dry (Figure 10).
Figure 10 - Better Quality and Rate
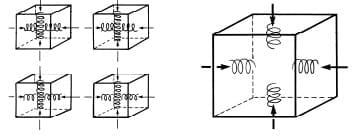
Large particles of your formulation will cause cracks and fractures in pellets. It is recommended that the hammermill screens for grinding do not exceed 1/8” diameter. Better results can be achieved from use of a #7 (7/64”) screen (Figure 11).
Figure 11 - Large Particles Cause Fractures
The smaller particles will increase your horsepower efficiency by increasing the throughput of material through the die holes with less horsepower (4). The finer grind also extends the die life as it decreases the “grinding” or milling of material on the solid land between the holes on the die face (5), (Figure 12).
Figure 12 - Small Particles
Increase horsepower efficiency - increases throughput of material through die holes with less HP Extend die life - decreases “grinding” or milling on solid land between holes on die face
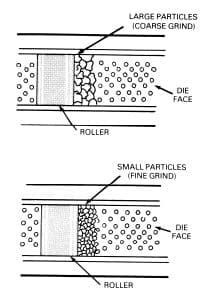
Fat
The fat content of an ingredient or feed can mean either natural fat or fat added. Both are an aid in increasing production rates. The pellet quality could be seriously affected with the addition of too much fat, normally 2% or more. The added fat can be of two kinds - animal fat or vegetable fat. Animal fats are presently the most commonly used in commercial feeds.
Fiber
High fiber creates production rate problems, as fiber is hard to compress into a pellet. Because of the natural binders inherent to fiber, a good quality pellet results.
Texture
When referring to texture, three general areas need to be considered: coarse, medium and fine. Fine or medium ground materials provide greater surface area for absorption of moisture from steam, resulting in better lubrication and increased production rates. Also, more particles are exposed to steam, resulting in possible chemical changes that may be needed for quality. The starting density can be increased when it includes a mix of medium and fine ground material. Very coarse grinds or large particle sizes provide natural breaking points in pellets, creating more fines.
Starch
High starch formulations or ingredients are difficult to produce a tough, durable pellet. The natural agglutenments can be activated only with high temperatures and moisture. The gelatinized material acts as a binder to produce the desired pellet quality. If, for some reason, the natural starches in a feed have been gelatinized before pelleting, poor pellet quality can be predicted. An example would be the drying of corn at high temperatures, which would cause pregelatinzation.
Moisture
Sufficient inbound moisture added prior to pelleting can be desirable in reaching good pellet durability. As stated earlier, many of today’s ingredients, such as brewer’s grains, are of a very dry nature and added moisture will supplement the pellet mill stream additions if it has an opportunity to soak in prior to reaching the pellet conditioning chamber. A binder may be added to the feed if adequate pellet quality is not obtained through proper steam conditioning and die selection. Two of the most widely used are bentonite and lignin sulfonate. The artificial binders add to the cost of a feed and are only used when all other means are exhausted.
STEAM CONDITIONING
Once the ingredients are mixed and transferred to the bin, the feed flows into a feeder which moves the feed at the desired rate into the conditioning chamber. This is where steam and molasses are added. Molasses is added according to the level specified by the feed formula. Steam conditioning is the most important element in achieving high quality pellets at high production rates at a low cost.
Reasons for Conditioning
The four basic reasons why we condition are:
1. To lubricate for faster production rate.
2. To lubricate to extend die life.
3. To lubricate to reduce energy costs.
4. To gelatinize starch for nutritional value.
The use of steam can increase the production of a pellet mill on most all feeds. There are a few exceptions, such as urea, mineral feeds and others that contain a lot of dried milk, whey and sugar (
Figure 13).
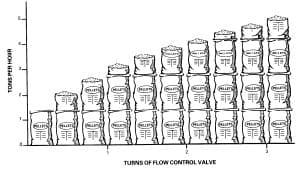
Increased Production
The graph shows that when we started this pellet mill (30 HP) with no steam we were running about 1200 lb./hour. By simply opening up the flow control valve and increasing the feed rate we finally got the unit to a rate of 5,000 lb./hour. This is now an illustration of where a pellet mill operator was running the pellet mill at 160°F.
Working the pellet mill up to 200°F, the pellets became more uniform in length, a little darker in color and had a gummy texture off the die. When we went to 205°F we plugged the pellet mill. Since the plug condition point is now known, set the pellet mill to run at 200°F and you can make a good quality product with higher production rates. The pellet mill operator should challenge the pellet mill daily to find out where the choke point is going to be, as it will vary daily. When increasing the production rates of the pellet mill by giving it more steam, this also reduces the fines at the pellet mill. The highest level of fines are made with no steam. This is because material was dry but when steam is added materials become soft and pliable and stick together (Figure 14).
Why Amount of Steam Added VariesAs we learned in the last section, different ingredients require different treatment in the pelleting process. Pellet mill operators must learn that the amount of steam that can be added will vary for each run, because of formulation, moisture, temperature, etc.. Due to the variables, they cannot pre-determine the amount of steam to add for any run. The existing conditions must dictate how much steam can be added.
Formulas can be classified into six broad categories. The categories should be well understood because each requires a different steam application. They are:
•Heat Sensitive Feeds: Feeds in this group contain high percentages of dried milk, whey and sugar. These materials will start to caramelize at about 140°F. Thin dies (to reduce frictional heat) and fat added to the formula (lubrication) can aid in reducing choke-ups. Normally low pressure steam will be used.
•Urea Feeds Little or no steam should be added to this group of feeds. Urea becomes more soluble as the temperature rises. Steam supplies the heat and moisture to dissolve the urea. When this occurs, the meal is wetter than meal without urea because the urea is acting as a liquid. The hot pellet temperature should be no higher than 150°F. Thin dies (reduce frictional heat) should be used to keep the temperature low. Fat (lubrication) added to the formula will help. Too much steam causes choke-ups as well as severe bin hang-up problems. Normally high pressure steam will be used.
•Molasses Feeds The amount of steam that can be added to this group is directly proportional to the per cent of molasses in the formula. Since molasses is approximately 26% water, the quantity of steam that can be added must be reduced or the meal will become too wet. This condition will result in choke-ups. Adding live steam into the molasses line will raise the molasses temperature to 200°F. Under these conditions, higher meal temperature can be achieved without exceeding the maximum moisture level. Normally high pressure steam is used.
•High Natural Protein Feeds This group includes supplements, concentrates and some steer and dairy feeds. Heat is more important than moisture to plasticize the protein. These feeds require more steam than the urea and heat sensitive feeds but less than high starch formulas. Normally high pressure steam is used.
•High Grain Feeds (High Starch) Poultry, broiler, hog and turkey feeds are in this group. High temperatures and high moistures are necessary to gelatinize the starches in the grain. The gelatinized material acts as a binder to produce tough pellets. To partially gelatinize the starches, the meal moisture must approach 17-18% moisture and the temperature must be at least 180°F. The hotter the meal, the greater the degree of gelatinization. Normally low pressure steam is used.
•Complete Dairy Feeds This group is usually between 12-16% in protein. Another characteristic of this group is that they contain large amounts of fluffy, roughage-type ingredients and are also low in grain content. These ingredients have a low ability to accept moisture. Steam addition should be low to keep the meal temperature below 140°F and the maximum moisture level at 12-13%. If above levels are exceeded pellets expand and crack after leaving the die.
You can increase your die life by reducing the frictional heat. In this graph (Figure 15) we illustrate that when material goes into the die at a cooler temperature, 120°F, it will come out of the die round 160°F, or a pick up of 40°F by friction or 33-1/3% increase in heat by friction. But if you raise your mash temperature up to 175°F, your pellet temperature out of the die will be 180°F, or a rise of 5°F, or a pick up of 3% heat from friction.
Figure 15 - Increased Die Life
Frictional heat can be determined by measuring the feed temperature as it leaves the conditioner and again after it leaves the die. The difference between the temperatures measures the friction of the feed through the die. High temperature difference (high friction) reduces die life and increases energy costs. Some pellet mills, however, do not have a thermometer within the conditioner.
A good pellet system needs to have a regulated supply of steam essential to a good pelleting operation. Poor systems can cause headaches both to the pellet mill operator and to the company management. There are three areas that must be considered in applying or adding steam. You must have good steam quantity, good steam quality and adequate steam pressure. High pressure boilers are preferable because they allow for smaller piping control valves, pressure regulators, etc., which can keep the cost down. The main consideration is the distance between the boiler and the pelleting operation and the system’s ability to deliver steam in a highly gaseous state when entering the pellet mill conditioner. The lower the pressure the lower the temperature and, consequently, the quicker the steam turns to water.
The steam harness must be of adequate size to provide a constant flow of steam without pressure variation. It must have the capability to provide a range between 20 PSI (low pressure) and 100 PSI (high pressure) steam. Pressure gauges and thermometers are essential to monitor the supply and flow of the steam.
In poultry or other high grain formulas, we try to achieve the starting of a process called gelatinization. This process starts when you reach mash temperatures of 175°F and the moisture level in the formula is around 17%. This is bound moisture (moisture that is contained in the ingredients) and added moisture (added by steam). Most all of the moisture added by steam is removed in the cooler. Gelatinization is defined as “The complete rupture of the starch granule, brought about by a combination of moisture, heat and pressure and (in some instances) a mechanical shear”. Basically, the gelatinization of starch has two results important to digestion:
1. Gelatinization enhances the ability of starches to absorb large quantities of water and this leads to improved digestibility in almost all cases and improved feed conversion in many cases.
2. Gelatinization increases the speed at which enzymes (amylases) can break down the linkages of starch, thus converting starch into simpler and more soluble carbohydrates.
Temperature & Moisture Relationship
Operators can be taught the fundamentals of steam application for the six broad formula categories but, until they completely understand the meal moisture and temperature relationship to steam addition, maximum results cannot be achieved. Bound moisture is that moisture in the ingredients before the meal arrives at the pellet mill. Added moisture is the moisture added at the pellet mill in the form of steam and molasses. Total moisture of the meal is the sum of the bound and added moisture. The choke point of a pellet mill is approximately 18% total meal moisture. Considering the formula groups that can utilize moderate to high steam addition, the quantity of steam that can be added at the pellet mill is dependent upon the bound moisture content and the dry meal temperature.
Greater quantities of steam can be added when the meal bound moisture is low (see Chart I). This condition allows a larger quantity of steam to be reached (choke point 18%). As the bound moisture level increases, the amount of added moisture (steam) must be reduced. This condition results in not achieving the high meal temperature before reaching the choke point. A rule of thumb: for each 1% of moisture added in the form of steam, the meal temperature is increased 20°F.
Chart I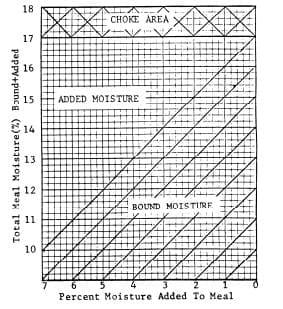
Effect of Bound Moisture plus Added
Moisture on Choke Point of Pellet Mill
The dry meal temperature influences the quantity of steam that can be added to achieve maximum moisture and temperature levels (see Chart II). Larger quantities of steam can be added when the dry meal temperature is high. This condition permits the operator to reach the necessary high wet meal temperature without exceeding the maximum moisture level. When the dry meal temperature is colder, more steam is required to raise the meal temperature to the desired level. Under these conditions, the maximum moisture level is reached before the desired wet meal temperature is obtained. Therefore, high bound moistures and cold meal temperatures prevent the running of pellet mills at maximum temperatures at all times.
Chart IIMoisture and Temperature Increase by Steam Addition at the Pellet Mill
Meal Moisture 12%
Operators must be trained to observe the moisture and temperature differentials in order to run safely at high wet meal temperature. To achieve accurate steam conditioning, machine attention and operator initiative is essential. Running at less than optimum temperatures and moistures will result in lower production and poorer quality pellets. Recent research indicates that there are more benefits if water is added at the batch or line mixer areas and the premix is allowed to absorb that water prior to pelleting. Moisture added in this way is less expensive than steam. This increases the inbound level of moisture and limits the steam to be used as an external or lubricant factor which results in both increased production and reduced energy costs. Many manufacturers are now using this method with good success.
Conditioning of Feed Ingredients
The purpose of conditioning a mixture of feed ingredients is to uniformly penetrate each particle with the same amount of moisture and heat, in other words, homogenization. This is accomplished by mixing. The principles of mixing are time, temperature and turbulence.
Time: Regardless of the shape or size of the particle, it requires time for moisture and heat to thoroughly penetrate the particles.
Temperature: Many chemical and physical reactions increase twofold with each 10°F rise. In the case of wet molasses, the viscosity decreases twofold for every 10°F rise.
Turbulence: A physical force produced by a paddle shaft rotating at a given speed so that liquids and solids repeatedly contact each other.
If these principles are applied, the surface of each particle will be void of excess moisture, and/or molasses and/or fat. This can easily be observed by inspecting the conditioning chamber. If it is clean, mixing is efficient. On the other hand, if it is coated mixing is not taking place. The appropriate question for the above is “Why?”. Upon adding liquids to the mixed feed ingredients, the liquid does not completely penetrate the ingredient particle and, thus, the surface is coated. As these particles are mixed, they adhere to each other, forming balls (snowball effect) and these balls coat the conditioning chamber. The net result is that a mixture of dry, semi-dry and wet particles enters the pellet mill die. This creates erratic production and quality. For example, an actual experience in a feedmill with two 100 HP pelleting systems with similar die size and speed, but with one variance, which was the size of the conditioner. One conditioner was 9”x42” and the other was 12” x54”. Wet molasses was added at the conditioner to the same feed. The 9” diameter conditioner repeatedly produced molasses balls and plugged the mill, whereas the 12” diameter comparatively produced smaller molasses balls and produced pellets. Basically, the 12” had more holding time than the 9” conditioner.
OPERATING PROCEDURES
Start Up
The operator must know the bin and valving arrangements for the bins over the pellet mill, as well as the bin and valving arrangements after the shaker to bulk or packer bins. A check list may be provided for pellet mill operators to reduce costly errors and also to get the pellet mill on stream as fast as possible. A check list may contain items as listed below.
1. Name of Feed
A. Die information. Hole size and thickness.
B. Pellets or crumbles?
2. Bin Management
A. Bin number from which meal will be drawn. California Pellet Mill Co.
B. Bin number for finished product. Is bin empty?
3. Equipment Inspection
A. All motors running?
B. Varispeed on pellet mill feeder turned back to minimum setting?
4. Contamination Prevention
A. Run first of the run on floor to purge pellet mill feeder, conditioner and die before running to cooler.
5. Run Conditions for Maximum Capacity and Quality
A. Check thermometer to get maximum temperature.
B. Check hot pellets for correct moisture addition by catching a pellet as it has been made right off the die and squeezing it between the thumb and forefinger to see if it has the consistency of putty or gum (steam and/or molasses).
C. Check ammeter for motor load information.
D. Check hot pellets for correct knife adjustment.
E. Check cooler. On vertical coolers make sure both columns are discharging. On horizontal coolers make sure belt speed is adjusted to get desired depth of burden and that the burden depth is level.
F. Check crumbler. Make adjustment on rolls for correct product sizing. Make sure rolls are in parallel adjustment.
G. Readjustment of steam and feed rate when fines begin to return. Make same check as in A, B, and C.
H. Make capacity check.
I. Record data on production sheet.
NOTE: When starting a pellet mill on subsequent runs never start the mill with the feeder setting from previous run. Reset feeder to the lower range of the feeder adjustment. After you have operated the machine on a specific product several times, you will be able to start at higher settings without fear of plugging. You will be able to bring the pellet mill to full production in a very short time by experience with the feeder setting and regulation of the steam valve.
Starting a New Die
A pellet mill with a new die installed should be started slowly. Set feeder variable speed drive at lowest setting to allow a minimum rate of feed flowing through the conditioner and to the die.
Drain condensate from steam supply line to eliminate slugs of water from entering conditioning chamber. Start motors, main drive motor, conditioner motor and feeder motor. Do not add steam when first starting the die; allow die holes to fill with dry material. Check ammeter for load on main drive motor. If not pulling full load, increase feeder setting until it shows full load. Open steam valve slightly at this point and in a few seconds the amperage should drop back. If amperage drops, increase feeder setting and repeat until you have approximately 80-90% of maximum load. Remember, the ammeter will not drop immediately when you open the steam valve, for it takes a few seconds for the material to reach the die to have any effect on the power required to pellet.
Operate the pellet mill at this reduced load setting for two hours to allow the die holes to become highly polished, then adjust your mill to full load. Keep in mind that the advancement of the feeder and steam valve setting should be slight when starting a new die.
Pelleting
The real heart of the pelleting process is the nip point or the area where the wedge of feed is between the roll and the die. Most all other equipment in the pelleting process is supportive equipment to this, the most crucial part of pelleting. There are three points of pressure: (1) the roll acting upon the material compresses the material into the die, (2) the die itself has a resistance that can hold back the flow of the material through the holes in that die, and (3) the pressure exerted by the rolls combined with the frictional pressures of the formulation itself. This pressure keeps the material compressed together and keeps it from squirting along the face of the die in front of the roll. When we increase the variable speed drive or control and increase the amount of feed into the pellet mill, the amount of feed thickens in direct proportion just in front of the roll. In other words, there is greater force pushing the feed into the nip point instead of down into the holes of the die. This is normally what causes a pellet mill to plug. This slug or mat of feed can build up in front of the roll, hindering the roll’s ability to crimp and push the feed into the die holes. Thus, surges of feed should be prevented from entering into the pelleting chamber. Feed distribution is extremely important across the face of the die and into this nip point.
Feed distribution is a problem and can cause the pad to be too deep and, again, limit the ability of the roll to force the product into the die holes. This essentially limits the production. This is why it is critical that the rolls be set on a regular basis, remembering that the feed flow through the die is what causes the die to wear away from the rolls. The rolls should be adjusted to a point so that the roll will be allowed to turn.
Pelleting is a daily exercise in ability and knowledge. While large pieces of equipment are necessary to complete the pelleting process, it should become obvious at this point that the operator is, unquestionably, the most important factor in achieving a good pellet production and good pellet quality. He must understand the pelleting process and be able to adjust many times in a particular day to the ambient temperatures, humidity, formulation changes, conditions of ingredients, and bound or inbound moisture levels of these ingredients. Running a pellet mill can be a trying, difficult process or one of great challenge for the individual. It becomes basically his choice as to which he prefers.
Shut Down
Since there is as much poor product produced at the end of the run as there is at the beginning of the run, operators must give proper attention to all phases of the pelleting process.
1. Machine Attention - be available when bins begin to empty.
2. Adjustments
A. Reduce steam and molasses addition to compensate for the rerunning of fines.
B. On horizontal coolers reduce belt speed.
C. Return feeder varispeed drive to minimum setting when finished running fines.
D. Shut off feeder and conditioner motors.
E. Purge die with oily material if die is to be changed or will be idle for 8 hours or longer.
F. Shut off mill motor.
Maintaining Optimum Loads
Operators must learn that variables occur during the run and, therefore, machine attention is essential. In theory, there is no final adjustment on a pellet mill. To achieve maximum capacity and produce the highest quality pellets, the ammeter, thermometer and hot pellet temperature must be constantly monitored. Listed below are some of the items that cause variations during the run.
1. Bin hang up
2. Bin separation
3. Return of fines from shaker
4. Steam pressure fluctuation
A. Boiler failure
B. Pressure regulative valve failure
5. Steam quality changes
A. Foaming boiler
B. Steam trap failure
C. Steam separator failure
6. Bound meal moisture variation
7. Heat buildup in die
Adequate control accessories must provided if the operator is expected to run at maximum capacity and high quality. However, when control accessories are provided, a maintenance program should be established to ensure no malfunctioning. Some of the control accessories that can be provided are:
1. Bin level alarm: Light or audible alarm is activated when bin is running empty.
2. Solenoid valves: Installed on steam and molasses lines to shut off liquids if there is an interruption of feed flow.
3. Tachometers: Installed on feeder screw to indicate RPM to check capacity rates.
4. Air operated pressure regulating valves: Installed to allow operator to adjust steam pressure easily.
5. Overload controls: Installed with time delays to shut off liquids, conditioner and feeder motor when main drive motor goes into overload condition. When overload condition no longer exists, time delays will start conditioner motor, feeder motor and liquid addition in proper sequence.
6. Cooler controls: Automatic depth of burden controller to ensure maximum bed depth.
7. Crumbler controls: Installed on rolls to remotely set rolls for various product sizes. Also controls to operate by-pass valves remotely.
8. Valve controls: Installed on spout valves for remote operation.
Housekeeping
The environment that the operator works in will have an influence on his attitude towards production and quality. The work area and machines should be painted, clean and well-lighted. It is the duty of the operator to keep his work area and machines clean.
1. Brush down pellet mill once per day or more often if conditions warrant.
2. Keep area around pellet mills clean. Sweep after each choke. Dispose of waste.
3. Scraper doors and front of gearbox once per day.
4. Clean feed chutes as often as necessary.
5. Conditioner cleaned once per week.
6. Feeder cleaned once per week. California Pellet Mill Co.
7. Check cleanliness of coolers once per shift.
8. Operator to lubricate pellet mill per manufacturer’s recommendations.
9. Check shear pins to make sure they are installed correctly.
10. Clean magnets at least once per day.
11. Check steam traps.
12. Report any machine problems to supervisors.
13. Check knives for sharpness.
14. Check roller adjustment and adjust when necessary.
15. Exercise good die change practices.
Cooling
The exhaust temperature of the cooler, which is governed by the temperature of the pellets, and ambient air determines the amount of moisture removal from the pellets. In turn, the cubic feet per minute of ambient air required must consider the inherent properties of air used at the specific location. Also, as in conditioning feed, holding time becomes important. There is an equilibrium cooled pellet temperature beyond this point, excess air and holding time is superfluous.
Cooling factors can be established based on the classification of feed (water soluble, grain and grain by-products). These factors are as follows:
•Water Soluble Ingredients
1) Relative humidity below 65%
Temperature of cooled pellet = ambient air temperature + 15°F
2) Relative humidity above 65% and above 50°F
Temperature of cooled pellets = ambient air temperature + 22°F
•Cubes
Temperature of cooled cubes = ambient air temperature + 22°F
•Other Classification
Temperature of pellets = ambient air temperature + 15°F
Why 15°F = ambient temperature = cooled product temperature? This is based on a water cooling tower performance. It is an ideal example, as dispersion and mixing occur very efficiently. In this case, water can be cooled within 15°F of the ambient temperature.
Why 22°F for water soluble ingredients? In cases where the air humidity is over 65% and 50°F, the water soluble ingredients will pick up from 1% to 1.25% moisture. This would result in caking and pellet deterioration. In case of cubes, 22°F + ambient air temperature will decrease the fines produced.
In many cases in the production of cubes, if the cooling differential exceeds 22°F the fines increase as high as 10%. Another physical factor should be considered - the first 10-15 minutes production from the cooler. At this time, the cooler and product are not at equilibrium with the cooling air. As a result, the product is warmer by as much as 20-25°F. In the case of water soluble ingredients, they will cake over the holding bin valve. If physically possible, the initial cooler production should be recycled.
The measuring equipment required to accomplish the above functions are a relative humidity gauge and thermometer, located in the air stream entering the cooler. Another thermometer should be located in the product being discharged from the cooler. This thermometer should be encased in a thermometer brass well so that the thermometer sensing stem doesn’t disintegrate from abrasion. In conclusion, the cooling capacity of a cooler determines the quality production capacity of a pellet mill.
Figure 16
Pellets are cooled by passing ambient air through a bed of hot pellets. The principle involved is known as evaporative cooling. The factors that govern are:
1. Temperature of the ambient air
2. Relative humidity of the ambient air
3. Cubic feet of ambient air per minute per pound of hot pellets
Illustration of 1, 2, and 3 is shown in Figure 17.
Figure 17
Moisture Capacity of Air
MECHANICAL ADJUSTMENTS AND MAINTENANCE
Knife Adjustment
Dull knives produce more fines at the die. Knife inspection should be made every shift. The knife adjustment is dependent on the desired length of pellet, die speed, and thickness. One knife is provided for each roller. The upper knife cuts for the left hand roll and the lower knife for the right hand roll. Two knives are used when there is sufficient extrusion at each roller to produce the desired length pellet. When making cubes, the knives will be adjusted away from the die as far as possible or removed. You will then use a special sickle-type cube knife or a breaker bar located above the discharge gate to regulate length. You will be instructed as to the desired length of each pellet or cube by your supervisor.
Roller Adjustment
Accurate roller adjustment is necessary for maximum capacity and long die and roller life. Loose roll adjustment will reduce capacity and cause choke-ups. Tight roll adjustment will result in rolled over dies and excessive roll wear. Die breakage can result because of poor roll setting.
In the heat treating process, a certain amount of distortion occurs which leaves high spots on the face of the die. Both rollers should be adjusted so that when the die is turning at a low RPM, the rolls should hit the high spot only. This type of adjustment prevents excessive metal-to-metal contact between the roller and the die but exerts sufficient pressure to maintain high capacity.
Die Care
By following a few simple rules your die life will be prolonged and you will realize the greatest production from your dies. Never abuse a die by striking it with a hammer or by dropping it on a hard surface. If force is necessary to install the die, use a plastic hammer or piece of wood. The die is keyed to the quill and held in place by the die clamp. Care is necessary to have the surfaces of both the die and quill clean for proper mounting.
The die must be securely held by the die clamp at all times. A worn out die clamp or quill insert will make proper fit and operation impossible. A loose fit at this point will cause flexing and excessive stress on the die, rollers and drive train. The quill insert should be replaced if it becomes worn. When mounting a new die, check the die clamp with the gauge, which is shipped with the new die.
Magnets, scalpers and other cleaning devices are vital to the life of a die - they are to be cleaned and checked regularly to make certain they are doing the job of removing metal and other material from the feed. Periodic inspection of the die for presence of foreign material is advisable. Pieces of tramp metal which have become embedded in the die should be removed by punching or drilling from the outside end of the hole. The care of the die is similar to that of a rifle barrel bore. The holes in the die are carefully machined and highly polished. This hole surface must be preserved if maximum pellet capacity is to be maintained. If the mill is going to be shut down for over one half hour or for a die change, the die should be filled with an oily mixture. When a die is removed from the pellet mill, store in a protected dry area. Also, when you receive a new die store it in this protected dry area to eliminate rust.
Removing the Die
1. Make certain the die has been filled with an oily mixture.
2. Back off cutting knives from die.
3. Open pellet chamber and remove feed cone.
4. Back rollers away from die.
5. Remove die clamp.
6. Remove die by drawing away from mill. If is does not come loose easily, pry in the slots between the die and the quill.
7. Store in a dry place.
NOTE: For a more detailed procedure for adjusting knives and rolls and removal of die and rolls, refer to manufacturer’s manual for your model pellet mill.
Maintenance of Pellet Mill Equipment
Feeders: Lubrication of feeder - check oil level in variable speed drive weekly and oil roller chain sparingly. Grease front feeder bushing daily. Feeder flight bearings grease monthly.
Conditioner: A clean out panel is located on the side of the conditioner chamber to permit inspection and cleaning of the mixer without removing the mixer shaft.
Lubrication: Grease the bearing at each end of the mixer monthly.
Feed Chute: The feed chute carries feed from the conditioning mixer to the die cavity by gravity flow. To do this job efficiently, the chute must be kept clean and free of dents. If a magnet is located in the feed chute, clean it after each run to remove metal buildup.
Deflector: The purpose of the deflector is to maintain a clean surface on the cone and assure uniform distribution of feed to the die. Keep clear of caked on material which will restrict flow to the die.
Mainshaft and Drive Assembly: Most models have the entire drive running in oil and needs only the oil changed twice yearly. On new models the front main shaft bearing needs to be greased each eight (8) hours of operation.
Operator Lubrication Summary
1. Lubricate rollers at least once every four hours of continuous operation. Smaller amounts every one hour are also recommended (Grease rolls at end of runs to keep out feed material. The grease in the rolls will contract when allowed to cool and will draw feed material into bearings.).
2. Lubricate main shaft bearing every eight hours.
3. Change gearbox oil every 2,000 hours or every six months.
4. Check oil level in feeder drive weekly and oil roller chain drive sparingly.
5. Grease conditioner and feeder shaft bearings monthly.
6. Grease knife brackets daily and work manually to keep free.
Keep machine clean. Blow off dust, wipe up excess oil or grease accumulations.
QUALITY CONTROL
The quality of a pellet will be based largely on the following factors:
•Fines
•Color
•Size
•Appearance
Fines are a major factor in determining consumer satisfaction with pelleted feed quality. Producing a tough pellet will eliminate most fines complaints. The section on conditioning has dealt with producing a tough pellet.
A rule of thumb for the industry has been a maximum of 10-20% fines in pelleted feed. The per cent of fines can be determined by the use of sieves. Normally, color is a very important part of determining the quality of pelleted feed. If there has been no formula change it is a good check on mixing and the addition of liquids, such as molasses and fat.
The size of pellet also helps determine quality. The length of a pellet varies from two to three times the hole size of a die. For example, a 3/16” diameter pellet will have a length of approximately 1/2”. The shape of the cross-section of a pellet can vary, with the majority being either round or square.
The appearance of the outer surface of a pellet will give an indication of the pellet quality. A rough exterior, not a shiny glazed surface, is desired and will indicate that a tough, durable pellet has been produced.
Quality Tests
Operators should be instructed to make quality checks at the pellet mill and at the cooler of the finished product.
At the Pellet Mill
Thermometers should be used to check the wet meal temperature. The thermometers should be used only as a guide. The reading will give a general indication because, on some days, a given formula can be run hotter than on other days. Hot pellet temperatures should be checked if heat sensitive feeds and urea feeds are being run. A physical test of the hot pellets is necessary to determine the amount of moisture in the product. A hot pellet should be placed between the thumb and forefinger and mashed into the shape of a wafer. It should be the consistency of putty and should not crumble. If the wafer is mealy and dry, more steam should be added until the putty consistency is achieved.
At the Cooler and/or Packer
Portable hardness testers should be used to determine the pellet hardness for each run. If a minimum hardness standard is not reached, the operator should shut down and consult with his supervisor. Checking cool pellet temperatures will detect any malfunctioning of the cooling system.
SAFETY
As with all modern machines, equipment for the production of pelleted feed has been housed and guarded so as to virtually eliminate all opportunities for injury to personnel during normal operation. Yet injuries continue to occur. The great majority of these injuries are due to abnormal conditions causing, or coupled with, some hazardous action by the operator. Many times these hazardous actions are an attempt on the part of the operator to correct the abnormal situation more quickly to return to normal operations sooner. We can admire any operator for his diligence in these cases but we must censure him for his carelessness. An example of this is the maintenance man who was greasing the crumble rolls and noticed that a bolt too large to enter the rolls was rolling between the rolls. In an attempt to pick the bolt out, his fingers were caught, resulting in the loss of two fingers. This accident occurred because he failed to shut off the machine.
Cleaning equipment while it is running, or starting equipment while it is being serviced, is a very common cause of injury and must be guarded against. One of the better methods of preventing this type of accident is to disconnect the power to that equipment and either padlock or hang a red danger tag on the switch.
The opportunity for this kind of accident to happen is very great in the pelleting area. We find much need for cleaning and servicing this high power equipment. In addition to the crumble rolls, the conditioner, the die chamber, the cooler, the elevator, and the screen all require servicing and cleaning. All of these have sufficient power and machinery motion to cause severe injury.
Pellet mill operators, as well as all mill employees, are constantly exposing themselves to other common safety hazards. For instance, electrical shock, through the use of worn drop cords or damaged electrical conduits, is a constant danger. One must be watchful for the signs of these opportunities for electrical failure. Usually they are easily detected by a simple visual inspection. Another common injury sustained by pellet mill operators is falls. The size of his equipment sometimes requires him to climb to inspect or service some part. He must take care that the ladder he uses is safe to use on the job he is doing and then he must work with care.
A pellet mill operator finds his machinery on many floors of his mill. This necessitates a great deal of movement from one place to another. Many times it may be desirable to move hurriedly. Care must be taken in these movements, even though he maintains a clean and non-slippery floor surface.
Each man is expected to carry the prime responsibility for his own safety and the safety of his fellow employees. This responsibility not only requires that he work carefully and safely but also that he insist:
1. The company should provide the proper, safe tools and work area.
2. The machines should be shut off and “locked out” before being serviced.
3. The use of machine guards, protective equipment and other safety devices should be mandatory.
4. His fellow employees must practice good safety procedures.
5. Everyone should be safety conscious, giving safety the attention it deserves
Inspection and Maintenance Instruction Sheet
Initial each block for every time you check the following:
Things to Do Daily
Things to Check Weekly
Things to Check Monthly
Things to Check When the Die is off the Pellet Mill
Things to Do Every 2000 Hours