Introduction
During the feed pelleting process conditioned feed mash is passing through the pellet press die where animal feed pellets are formed by rheological properties of the mash and different mechanical forces applied on that mash.
Different sized animals eat different sized feed, therefore cutting, thus uniformity of feed pellets is essential procedure for feed producers. In the end of the pelleting process pellet press knives have role to cut the feed pellets (figure 1). Bearing in mind that worn knives usually have randomized cutting area, feed pellets are more randomly stressed, therefore new abrasions would be formed hence more dust in the end product obtained. All that leads to reduced physical quality of feed pellets and non-satisfaction from customers.
Information insufficiency related to standardized feed uniforming procedure led to this research. Research based on possibility that pellet press knives condition influence physical properties of feed pellets has been accomplished at Fôrtek - Center for Feed Technology, Norwegian University of Life Science.
The research showed that knives condition (worn or sharp) can affect physical quality of feed pellets.
Materials and Methods
Research has been based on two types of ingredient composition (table 1). Hypothetically, superior and poor for physical properties of feed pellets.
Feed mash conditioning was performed by pellet press conditioning chamber with 75 C° preset temperature in both, test and its replica for both ingredient compositions. Samples taken after the conditioner have been analyzed for moistures. Moisture showed to be similar in both tests and diets (+/- 1%). Finished feed samples were taken immediately after pellet press to avoid any stress (breakage) due to the transport to packaging line. Cooling was performed for 6 hours at the ambient temperature of 26 C° and relative humidity of 50% to avoid any forced moisture removal, thus more likely larger crack formation.
Two different knife conditions (figure 2 & 3) have been used as well as the new technique of pushing pellets thus breaking them where the sheer stress is most likely to be lowest, have been performed by pusher (figure 4).
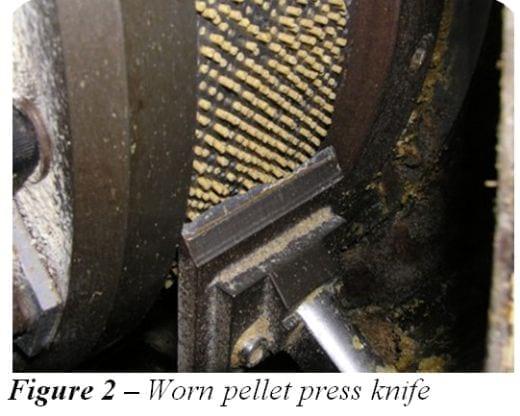
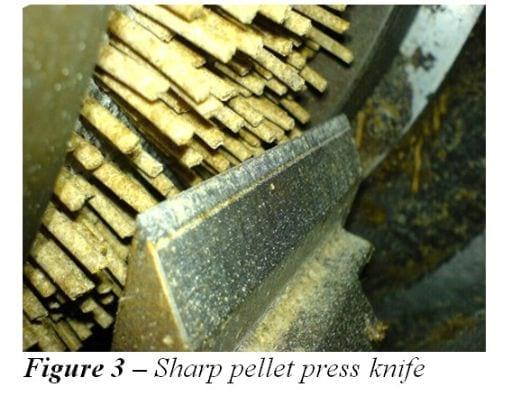
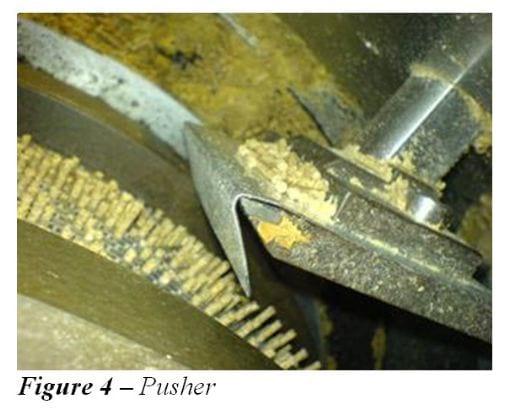
In order to have better overview of this research, two different pellet lengths have been exercised (10 and 20mm), which means that different distances of knifes from pellet press die surface have been set.
Durability test was performed by Holmen Pellet Durability tester for both, test and its replica according to UMB-PQP procedures*.
Results and discussion
Abrasion formation, thus percentage of fines or physical property of feed pellets defined as PDI (%) showed to depend on pellet press knife condition (Figure 5).
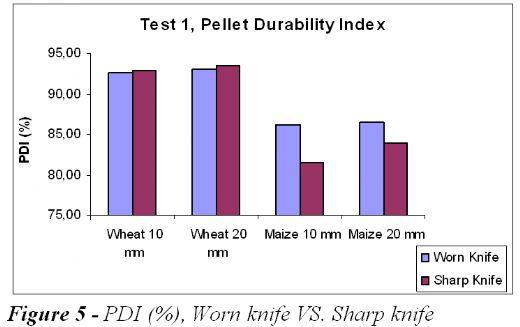
When pellet length is shorter or when knifes are adjusted closer to the pellet press die, in this case 10mm, wheat based pellets demonstrate slight decrease of the physical properties while cut with worn knifes. Opposite was observed in feed pellets based on maize, where the worn knifes have even influenced on better PDI (%) values (p < 0,01). With increasing the pellet length on 20mm by cutting with worn knife physical property of wheat based feed pellets has not significantly changed, compared to sharp knife. On maize based pellets opposite effect was observed.
Feed pellets, compressed and formed in the pellet press die at the die outlet are experiencing sheer stress formed by knife. Wheat based pellets did not show to be influenced by different knife conditions as sharp neither worn.
When knife is worn, theoretically impact of revolved pellets is let by chance, thus additional abrasions on pellets are likely to be formed. Opposite from the theoretical hypothesis was observed on maize based feed pellets, where worn knife or wider cutting area has derived better physical properties (figure 5).
Cutting technique by pushing the maize based feed pellets by angled and widen flat surface (figure 4) illustrated increasing the physical properties of maize based pellets compared to cutting the same pellets with the sharp knifes (figure 6). Explanation for demonstrated results is that "pusher" is simply pressing on feed pellets which are occurring after the pellet die holes, consequently forcing pellet to brake where natural crack already exist without additional sheer stress onto the other cracks of feed pellet. When pellets are extruded through the pellet die holes, some abrasions are possible to form due to different compression and adhesive properties of neighboured particles. Longer pellets would be pushed by pusher and weakest abrasion is likely to crack, while that opportunity is reduced when pellets are set to be shorter. Difference (p<0,01) for "pushing technique" for maize based feed pellets with different lengths is illustrated in figure 6.
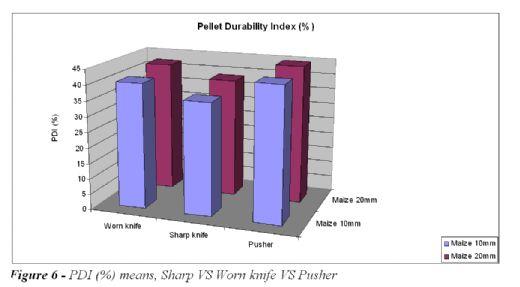
Conclusion
Dependable on factory's own needs and estimation of binding properties of feed formulation cutting technique has to be chosen carefully. Results from this research outcomes that feed pellets made of raw materials expected as good for physical properties (in this case, wheat based) can be cut with the sharp and maintained knifes, but if knifes are worn, additional maintenance investment is not necessary. Whereas pellets manufactured of raw materials assumed as bad for physical quality of feed pellets (our case, maize based) should be pushed. Hence pellet is forced to break where its natural weakest crack exist with obvious increase of PDI and reduction of additional cracks formed by knife sheer stress.
* UMB-PQP pellet durability test procedure -Before the durability test, all samples are weight out as 120g representative sample and cleaned from any dust with the Retch, AS 200 sieving machine. After sieving 3mm in diameter pellets through 2,6mm sieve, each sample was weigh as 100g sample. Holmen pellet durability tester was run for 60 seconds and then 30 additional seconds to collect remained feed pellets. Considered durability test results - PDI % (Pellet Durability Index) are presented from weight remained from pellets in the 2,6mm sieve, sieved for 30 seconds by Retch, AS 200 sieving machine on 1.5 mm shaking amplitude to avoid any human error.