In the year 2000, U.S. commercial feed mills averaged 20.3 tons per hour per pellet mill line. The average pellet durability index (PDI) of the final pelleted products was 92.7 and average processing cost per ton was $9.03. These figures do not include data from integrated operations where the average PDI is 25 to 40 percent and processing costs per ton may be as low as $3 per ton. Integrators usually operate the mills at full capacity and outputs rather than trying to obtain the optimum pellet quality. Quality of feed (measured in PDI) and production costs (dollars per ton) have shown gradual improvements and this is believed due to improved processing techniques – especially in the preconditioning phases1. Thereported benefits of enhanced preconditioning are as follows:
Operational Principals Conditioners “precondition” the mash before pelleting by accomplishing three unit operations: heating, hydrating, and mixing. Mill operators focus on the heating factor as it is easy to monitor and control. Thermal energy is occasionally added through “dry heating” methods by jacketing or plating equipment with insulation or heating elements. Exhaust streams of hot air or steam from other processes have alsobeen used to provide heat.
Heating is accomplished most commonly and efficiently through direct steam injection,and this is theprinciple energy source in Wenger systems. Conditioning devices often includea sensor and controlsystem to maintain set-point temperatures at the discharge of the preconditioner.The addition of 4 to 5percent steam is usually sufficient to achieve desired discharge preconditionertemperatures of 93°C(200°F). Research has proven that with the excellent mixing imparted by WengerDDC systems, producttemperature at the discharge of the DDC need to only reach 75°C (165°F)to achieve pasteurization.
Moisture addition and hydration are very critical in pelleting operations, sincemost pellet mills can handlea maximum of 18 percent moisture in the preconditioned mash. This low moisturerequirement meansthat little or no water can be added as steam usually provides sufficient moisture.However, this is very dependent on the raw mash moisture and the industry isawaking to the fact that water addition cangreatly improve pellet quality as long as the maximum level is not exceeded.Moisture transfer into feedis much slower than heat transfer. However, because the operating parametersdictate low moistures,preconditioning occurs in a “moisture-starved” environment. As longas mixing is sufficient to get uniformmoisture distribution, actual retention times in DDC/pellet mills may not beas critical as extrusionprocesses where moisture levels are usually in the 25 to 28 percent range.
Mixing is a very critical parameter inpreconditioning. Much of the newconditioning technology that blossomedin the last few years has included longretention times (as much as 3 to 5minutes). The Wenger DDC technologyis able to meet or exceed theperformance of these systems becauseof excellent mixing. Typical retentiontimes have been two minutes or lesswith some mills running as short as 30seconds. Throughputs and installationarea are the major criteria for selectingthe proper size.
Process FlowRecipes are blended in batch mixers and then conveyed to the pelleting process.Often the grains areground while many of the ingredients in meal or powder form are not ground. However,improved feedconversion has caused the feed millers to look at post grinding systems wherethe complete recipes areground to an average of 600 microns.Grinding systems are fitted with screensand magnets to remove tramp metaland other foreign objects. The groundmash is transported to a bin/feedingsystem which serves to meter the mashinto the preconditioner. Steam, water,and other additives can be added in thepreconditioner. The conditioned mashgravity-flows out of the preconditionerinto the rolls area of the pellet mill(Figure 1).
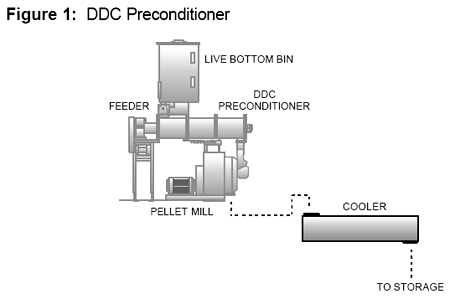
As an option, Wenger has developed aconstant discharge/self-emptyingpreconditioner by designing the DDC toact as a loss-in-weight system. By mounting the DDC on load cells and attachinga “choke” feeder at thedischarge of the preconditioner, several benefits are realized:
This feature (Figure 2) may not be necessary for many operations but provides excellent control of thepreconditioning process when these requirements exist.
PasteurizationThe DDC preconditioner has been shown to pasteurize pelleted feed products. Aspreviously mentionedthe DDC is capable of holding the feedfor up to two minutes and can reachtemperatures of 90º to 95ºC. Thiscombination of temperature andretention time will destroy manymicrobial populations. Table 1illustrates the ability of the DDCpreconditioner to destroy some ofthese microbes.
Product ImprovementThroughout the feed industry feed conversion is used to judge animal performance.Typically, it is justpounds of feed given to the animal per pound of animal weight. For example, ifa flock of birds is given1000 pounds of feed throughout the growing cycle, and 400 pounds of live weightis recorded, the feedconversion for that flock would be 2.50(1000/400). Scheideler (1995) noted theeffect of pellet quality on the feed onversion
ratio (FCR) for several poultry speciesincluding broilers, roasters, and turkeys.Poultry fed pellets with a PDI of 70 percentrequired less feed to reach market weightthan those fed pellets with a PDI of 25 percent (Table 2).
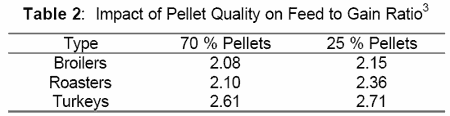
In a recent series of trials the Wenger DDC was compared to a single shaftedcylinder to determine itsadvantage. Starch gelatinization(percent cook) and pellet durabilityindex (PDI) were measured andcompared. The percent cook wasmeasured by determining thesusceptibility of starch to enzymaticdigestion. PDI was determined bytumbling the pellets for five minutes then determining the amount of productthat stayed on a numbereight sieve. The results are shown in Table 3.
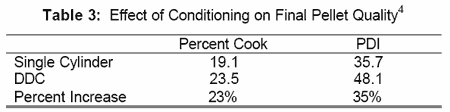
The DDC showed an advantage of 4.4 points of increased cook and 12.4 points ofincreased pelletdurability. Feeding trials showed that the FCR for the broilers fed pellets producedusing the WengerDDC feed was lower than the broilers fed pellets produced on the single shaftpreconditioner. As shownin Table 4, the FCR for the feedproduced on the DDCconditioner was 0.025 (or 2.5points) better than the feedproduced on the single shaftpreconditioner.
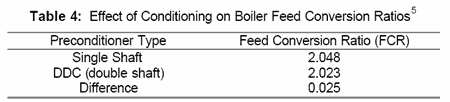
If we assume that one feed conversion point is worth 60 cents per ton of feedproduced, the DDCconditioner could pay for itself very quickly. For example a feed mill producing80 tons of feed per hour,operating 5 days per week, 24 hours per day would see a benefit of $5760 perweek or about $300,000per year if they saw an increase of 2.5 feed conversion points.
The Wenger DDC’s ability to provide longer retention times and more efficientmixing allows a higherquality pellet to be produced. This can lead to many advantages for feed millsthrough lower feed to gainratios and increased PDI.
Prepared by:Wenger Livestock Feed Process Team
Galen Rokey, Manager, Wenger Technical Center
Rob Strathman, Director Technical Service
Brian Plattner, Process Engineer
1 Lobo, Phillip. 2001. How mills are managed: Percent capacity decreases,while production efficiencyincreases in 2000. Feed Management. 52:1. 13-16.
2 Rokey. G. 2001. Pelleting, Conditioning, and Steam Addition. 2001Feed Management Seminar. USEgg and Poultry Association. Nashville TN.
3 Scheideler, S. E. 1995. Is Pelleting Cost Effective? Feed Management. 46:1.21-26.
4 Wenger 2001. Wenger Laboratory Analysis, Reference Number L20010103-001.
5 Rokey, G. J. 2001. Pelleting, Conditioning, and Steam Addition.US Egg and Poultry Association –2001 Feed Mill Management Seminar. Nashville, TN.