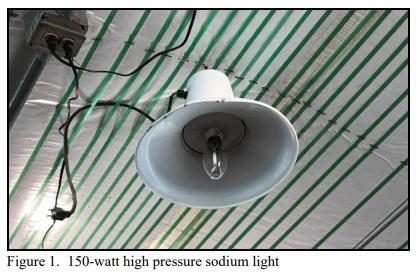
High pressure sodium (HPS) lights have been used in broiler-breeder houses for decades due to their very high lumen output. The typical 150-watt HPS fixture produces approximately 16,000 lumens of light which is 16 times the amount of light produced by a 75-watt incandescent light bulb. The downside of HPS lighting systems is that in order to produce the relatively high house light intensities sought by broiler-breeder producers, the systems will use a substantial amount of power. For example, in the typical broiler-breeder house, HPS light fixtures are installed approximately 20 feet on center along the ceiling peak. In a 500' long house the 25 HPS fixtures would consume nearly 4,000 watts (or 4 kilowatts of power). To put this in perspective, the typical tunnel fans uses between 0.9 and 1.3 kilowatts of power, which means that a breeder house’s HPS lighting system can use roughly the same amount of power as three or four tunnel fans. Unlike tunnel fans, whose operation varies dramatically with time of day and season, a houses lighting system will typically operate a consistent 16 hours a day, seven days, for the entire flock. As a result, it is not uncommon to find that over the course of a flock, the power consumed by a HPS lighting system can be similar to that used by the house’s tunnel fans.
It is important to realize that though a HPS lighting system uses a substantial amount of power, the fixtures themselves are actually very energy efficient when it comes to producing light. For every watt of power, a HPS light produces roughly 100 lumens of light. To put this in perspective, a 100-watt incandescent light bulb produces only 15 lumens per watt and a 23 watt compact fluorescent light produces 60 lumens per watt. It is interesting to note that a HPS fixture is actually more energy efficient than the typical LED. For instance, a 10-watt LED produces 80 lumens per watt, better than incandescent and fluorescent lights, but not quite as efficient as a HPS light’s 100 lumens per watt. A HPS lighting system’s high power usage is related to the level of light producers are often seeking and the system’s inability to distribute the light evenly across the width of a house. A single row of lights at the peak of ceiling tends to flood the center of the house with an excess of light while delivering a fifth or less of its light to the floor/slats near the side walls. As a result, to get an adequate amount of light at the side wall, there will be an excessive level of light in the center of the house. This reduces the overall efficiency of the system. If there were a much smaller version of the typical poultry house HPS light that could be installed in two or three rows, ten feet on center, it could be an energy efficient method of lighting a breeder house. The problem is that if such a system did exist it would be very likely impractical due to the relatively high cost associated with HPS fixtures.
Recently a study was conducted comparing the power usage and lighting uniformity of three different LED lighting system configurations to that of a HPS lighting system. The objective of the study was to reduce the power required to light a broiler-breeder house as well as improve light intensity uniformity. The study was conducted on a two-house broiler-breeder farm in North Georgia. Prior to the study, the lighting system in the two 40' X 500', curtain-sided, tunnel-ventilated houses consisted of a single row of 150-watt HPS fixtures, 20 feet on center, installed along the peak of the dropped ceiling.
To minimize the overall cost of the light system retrofit, it was decided to study a LED light system that, for the most part, could be installed by a producer. In one of the houses the HPS lights were replaced with a row of 40-watt LEDs (8,000 lumens - 3000 K). The screw base LEDs were hung from a standard light socket attached to a 10 feet cord which was plugged into the 120 volt receptacle which previously supplied power to the HPS lights (Figure 2). In addition, a series of five 100 feet long prewired, light cords with sockets (10 feet on center) were installed over each nest row (Figure 3, 4). The light cords were attached to the ceiling at each truss (4 feet) and 10 watt LEDs (800 lumens - 2700 K) were installed into each socket (Figure 5).
Prior to breeder placement four different lighting system configurations were evaluated for light intensity distribution and power usage:
1) 150-watt HPS lights 20 feet on center at ceiling peak
2) 40-watt LEDs 10 feet on center at ceiling peak
3) 40-watt LEDs 10 feet on center at ceiling peak with a row of 10-watt LEDs 10 feet on center over the nests
4) 40-watt LEDs 20 feet on center at ceiling peak with a row of 10-watt LEDs 10 feet on center over the nests
For each of the four lighting system configurations, 96 individual light intensity measurements were taken within a representative 48' X 40' section of the study house. To illustrate the lighting environment created by each lighting system configuration, a topographical image was created from the data collected (Figures 6 - 9). Figure 10 illustrates the average light intensity across the width of the house of the four different lighting system configurations. Pictures were taken on the slats to evaluate the shadows created by each lighting system configuration (11 - 14). The total power usage of each lighting system configuration was measured and estimated monthly power cost was calculated (16 hours a day, power cost of $0.10 per Kw-hr. Figure 15).
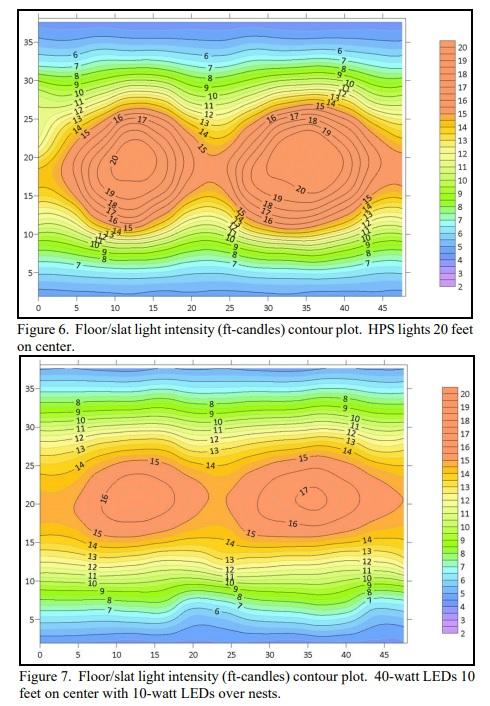
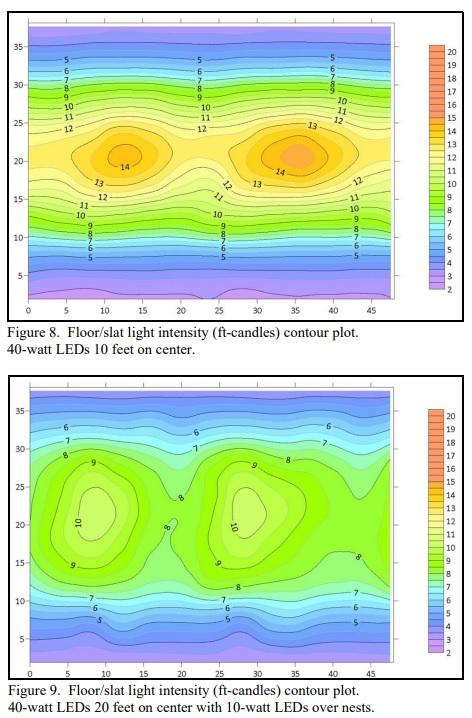
After reviewing the data, the poultry company decided to go with the 40-watt LEDs 20 feet on center with the 10-watt LEDs over the nest boxes. The company felt that this combination provided the adequate light intensity and uniformity, while also providing significant power savings for the producer. The only change to the tested configuration was that in the traditionally darker evaporative cooling pad and tunnel fan areas, the 40-watt LEDs were installed ten foot on center.
Power data loggers were installed to monitor lighting system and tunnel fan power usage on a continuous basis. The house equipped with the LED lighting system had 55 inch variable speed tunnel fans, while the house with HPS lighting system had conventional 48 inch slant wall tunnel fans (Poultry Housing Tips. “Variable Speed Tunnel Fans Can Result in Dramatic Power Savings”. vol 29 no. 6) Both house were operated identically. Power usage data were collected over the course of a flock that began in late August 2019, and ended the last week of April 2020. Operating costs were calculated assuming a power cost of $0.10 per Kw-hr. Production was monitored to determine if there were any detrimental effects related to the use of the LED lighting system.
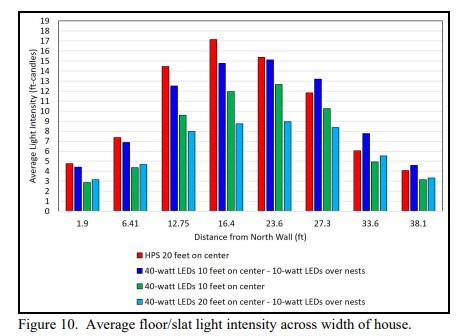
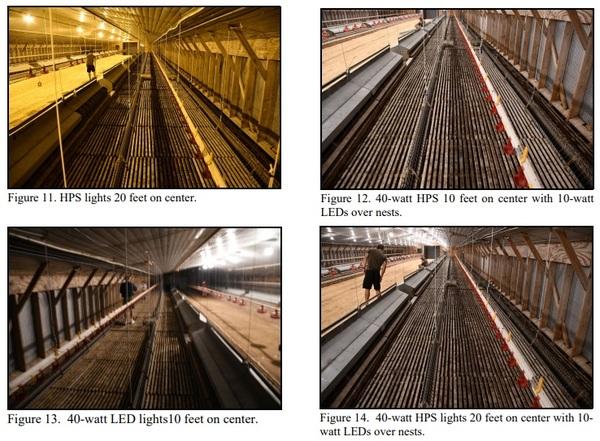
The cost of operating the lighting system as well as the tunnel fans in the two houses is illustrated in Figure 16. As projected, the LED lighting system cut lighting costs essentially in half. Interestingly, it cost approximately 30% more to operate the HPS lighting system than it did to operate the tunnel fans over the course of the flock. This is likely due to the fact that the flock was sold prior to hot weather and as a result tunnel fan usage was relatively limited. The savings provided by the variable speed tunnel fans were higher than normal also due to the fact that the houses were depopulated prior to hot weather. The variable speed tunnel fans were operating at their lowest speeds, which resulted in maximum power savings (+60% reduction). Had they been operating at the higher speeds, typically required during hot weather, the savings would have likely been closer to the 50% seen in previous flocks (Poultry Housing Tips. “Variable-Speed Tunnel Fan Study – Broiler-Breeder Flock #1 Results”. vol 30 no.7). It is also important to note that total flock operating costs for the lights and tunnel fans would have been higher had the flock not been caught roughly eight weeks sooner than normal. No differences in production between the two houses were observed by the farm manager.
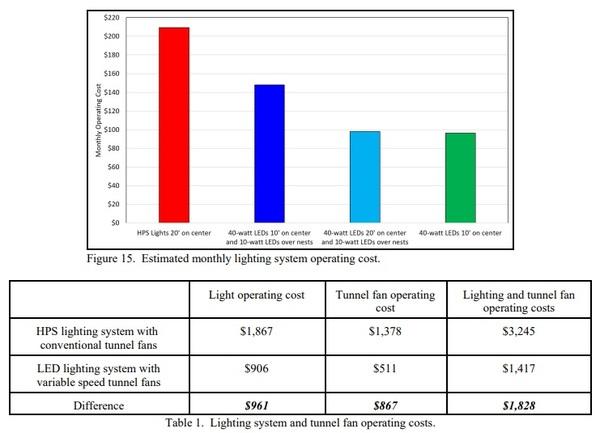
The cost of the components for the LED lighting system evaluated was approximately $2,800. If a farm owner performed most of the installation work themself, the cost of an LED lighting system such as the one tested could be recovered in a just couple of flocks. In other areas where power costs are significantly higher, the return on investment would be significantly faster and in a short period of time a breeder producer with multiple houses could see their income increase by thousands of dollars a year.
This article was originally published in Poultry Housing Tips, Volume 32, Number 6, 2020. University of Georgia, College of Agricultural and Environmental Sciences Cooperative Extension (https://www.poultryventilation.com/).