Let us start at the beginning in the wheat silos where we see an intake separator, often much maligned and rarely maintained since it is such a simple piece of equipment which rarely breaks down or goes wrong.
I don't class the intake separator as a peripheral machine but I do class the magnet in the silo as being peripheral to the process.
Magnets, wherever they may be, in the intake house, the wheat cleaning plant, scattered around the mill or in the bulk flour silo should have the material they collect examined regularly and for me that means at least once every eight hours unless there is a large quantity of product passing over them in which case twice a shift would be more acceptable.
Looking at what has been collected on a magnet can often give warning of a disaster about to happen elsewhere. If a large quantity of sifter bolts starts to appear then further examination is required at the sifter since one or more is clearly about to fall apart.
New items appearingIn the wheat cleaning house the principal machine are all familiar to us but there are some new items appearing which need our attention.
Colour sorters are common place now and often can be seen replacing cylinders and disc separators in the older, more established mills. In the new mills they are now the accepted norm and often just a separator and a colour sorter is all that is required to provide a clean wheat stream to first break.
However, colour sorters come under my heading of peripheral devices and they do require regular servicing, bulb changes and nozzle checks. The compressor which supplies air to these machines is definitely on my list of peripheral machines and needs good servicing if it is to work efficiently.
We have a great dependence on clean dry air for many functions in our mills and I see many mills where the compressor is stretched to its limit due to the air supply having ever increasing demands placed upon it as additional machines are added.
In my strongly advocated daily walk round the mill I recommend turning on the compressed air supply when the mill is not running. It is much easier to hear air leaks and track them down when plant is stopped and you would be surprised just how many traps and water separators jam open, costing you money when it is unnecessary.
The principle of colour sorting is to use the diffused light to make the wheat grains "disappear" into the background which then allows impurities to be much more easily identified. If bulbs are not maintained then the wheat remains visible and the colour sorter will reject it. A good maintenance contract will pay dividends ... literally.
The importance of calibrationDamping systems are important and when operating accurately can improve the condition of wheat to first break to such an extent as to allow the mill operative to set his mill up properly and optimize extraction rates.
Calibration is required regularly and records of "as found" conditions should be kept to identify seasonal trends. For example if the local vegetable processing factory uses high levels of water in the season then you will need to make adjustments to allow for that.
As we move on into the mill I would class the scales as peripheral machines, since they do not change the nature of the product as it passes through.
Scales do however play an enormously important part in the running of the mill since all our information about mill efficiency, extraction rates, throughput rates etc comes from the scales, more often than not these days linked to a central processor that gives a continuous read out of the scale readings and the calculations which we would otherwise do long hand at the end of each shift.
It goes really without saying that proper calibration is required on all scales and their proximity to blowing lies should be checked for any adverse effects on scale operations.
The use of flake disruptors on the head reductions, detachers on the lower reductions and other similar devices, either positioned in the basement, on the top floor or mounted directly in the pneumatic lift all have an impact on extraction and ash.
Keeping rotors in good order is of paramount importance and I believe it pays to change pins once a year ideally just prior to harvest. The number of rollermills in a mill has now drastically reduced since the mid 1950s when mills often had two rollerfloors.
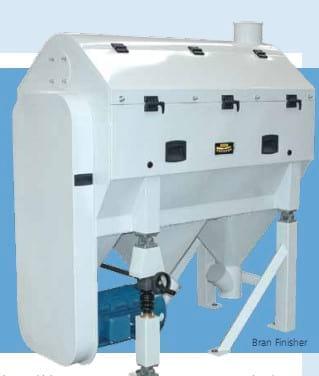
The fact that if a roll was set to grind too hard then flakes were produced which were scalped off and lost down the coarse reduction side of the mill was apparent to most millers and engineers and hence the flake disrupter was introduced so that hard grinds could be achieved and any flakes could be broken down before they reached the scalping covers. Similar maintenance tasks should be carried out periodically on disruptors and blades should be kept sharp by running an angle grinder over them to maintain the leading edge.
I also class sieve cleaners, throughs tray cleaners and other devices on purifiers and in sifters as peripheral devices and I believe that regular inspection of these and replacement of worn ones will give you a handsome return for very little expenditure.
Recognizing odoursRegular strip down of sifters will reveal the tell tale signs of bug urine which has a very pungent and unique odour. So unique is the smell that many operatives do not recognize it and it goes unattended to. It pays to train all staff correctly to recognize this odour and also in the accepted practices for dealing with insects.
Pheromone traps can help identify insects on the wing and also give warning that a fumigation should be performed. Pheromone traps should be logged and should not be placed anywhere where they are likely to be dislodged or fall off into the process. If you are not careful you could cause yourself more of a problem than you bargained for.
Several sifter sections are prone to sweating if not exhausted properly and careful attention should be paid to establish which sections are prone to this since when sweating or condensation does occur the sifter cannot perform properly and flour covers will simply blind over gradually.
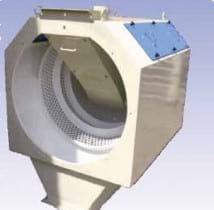
Spouts should be checked regularly under sifters that sweat to ensure mothfrasse and webbing does not build up. If it does then spouts should be cleaned by "dragging". Fortunately such evidence of insect activity is rarely seen these days.
Definitely classed as a peripheral machine in my book but with a very important role to play is the bran finisher.
Now fully recognized by most engineers, Satake in particular, this machine not only removes the last remnants of flour from bran but is also marshalls coarse stocks into a recognizable stream. Given the use of inclination in the new Satake machine the bran finisher can be used to great effect, especially as far as extraction levels are concerned.
The last ‘policeman'Redress sifters are all important since they are the last ‘policeman' in the mill.
I am seeing more mills using level probes under redress sifters to tell the mill operative when the bag is full of excess overtails, indicative of a burst cover back up the mill somewhere. Drawing samples will quickly identify where the burst cover lies.
As well as sieve cleaners being important then so too are roll brushes and other roll cleaners, criterion cleaners and similar These, when working correctly will enable the miller to set a good grind but if they are damaged or ill fitting the miller will struggle all day trying to set a good grind.
Screw conveyors collecting flour and being used to mix in additives should have the additives feeders positioned as far away from the discharge point as possible in order to attain a good mix.
Additive feeders should be equipped with level alarms so that flour cannot be produced without the correct additives. It varies from country to country as to whether the miller or the baker adds the bakery improvers but it is becoming the norm for the miller to do it, hence it is vitally important for there to be good indication of low levels in all the feeders. In the case of mills who have an automated mill control system the mill will be sent into suspend mode whenever low levels of additives are reached rather than produce any flour that is not acceptable to the baker.
Health and safety has precluded the use of gas to bleach flour but several mills still maintain agitators through which different flour streams may pass. Whilst this is somewhat over the top for most operations, I see no reason not to maintain agitators to assist with blending of flour additives.
In the bulk flour silos and through to the packing plant there is usually a liberal use of magnets. My earlier notes about magnets applies just as much here as earlier in the flow.
Making a large investmentPacking houses have changed beyond all recognition since the mid 20th Century.
High speed packing using carousels has led to direct loading onto vehicles, occasionally with very few, if any operatives at all. Such highly efficient items of equipment obviously require a sizeable investment and a large volume is needed to justify the expense. Well worth it however in the larger mills around the world.
In these larger mills it is quite common to pellet the bran produced and in mills where there is a low demand for bran it is common to place the bran in the wheat silos as they are emptied and then transship the bran back to the origin of the wheat on the next available grain vessel.
Occasionally larger mills will have their own feed mill and will use the bran as part of the diet for local livestock. In such cases they may bring in mixed cargoes of commodities such as wheat, maize, soy, etc to make up a balanced diet often using local ingredients such a guinea corn where available.
And, finally, I include in peripheral machinery such items as generators, laboratories and vehicles used for transporting finished products locally.
All of these need to be maintained, particularly generator sets. Where they are installed to supply power as an alternative to the main supply company it is done for reasons of continuity of supply and to maintain a constant voltage, not often achievable from the local power company. Using fuel from the incoming grain vessel to power the generators can show some economies, but there is little need to justify the expense of a generator set when the alternative is invariably no power supply at all.
As a last comment, it is attention to detail that keeps all these peripheral and ancillary machines performing satisfactorily and daily walks around the mill and other processes will pay handsome returns come the days of reckoning.
A simple check list of functions that should be examined daily is well worth keeping especially of the operations that are being monitored. It pays to know your mill and screenroom but we must not forget the ancillary machines, they all have a role to play.
ACKNOWLEDGEMENT