Research has concentrated primarily on the benefits of feeding pellets versus meal. Pellet quality has become more important in the swine and poultry industries as integrators continue to expand and recognise the value of feeding quality pellets.
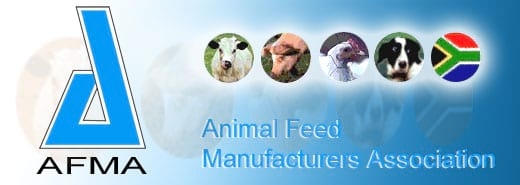
Effects in pigs
Research studies conducted in Europe and the United States have shown pelleted nursery diets will increase ADG and G/F by 9 to 10%. Pelleted grow-finish diets result in a 3 to 5% increase in ADG and 7 to 10% in G/F (Table 1). Research on the effect of pellet fines is limited and is generally confined to observations of poor quality pellets failing to result in improved animal performance. Gill and Oldfield (1965) and Tribble et al. (1979) reported poor animal performance when the feed contained significant levels of fines. However, when pellet quality was improved by changing the pelleting operation (i.e. thicker dies), animal performance was improved. Hanrahan (1984) reported no difference in finishing pig performance between pigs restricted fed a 69% or 62% PDI (Pellet Durability Index) pellet. Stark (1994) conducted swine feeding experiments demonstrating that feed containing a high quality pellet (no fines) resulted in greater efficiency of gain than feed containing 30% fines.
Improvement in poultry
Pelleted broiler diets improve growth performance and feed conversion. Hussar and Robblee (1962) reported reground pellets did not affect early bird performance. However, as the birds matured, birds fed whole pellets had better growth and feed conversion. Hull et al. (1968) reported birds fed pelleted diets had a 5% better feed conversion, but regrinding the pellets resulted in lower feed conversion than the meal diet. A field study conducted by Scheideler (1991) indicated birds fed 75% whole pellets as compared to 25% whole pellets had better feed conversion (F/G 2.08 vs 2.13). This result was likely due to selective feeding on the part of the broilers.
Turkeys appear to be more sensitive to pellet quality and fines than broilers. Several studies indicate pellet fines decrease turkey performance. Proudfoot and Hulan (1982) reported pelleted diets improved feed conversions. However, as pellet fines increased from 0% to 60%, performance decreased. Moran (1989) showed a decrease in growth and performance when re-ground pellets were fed. Salmon (1985) reported no difference in bird performance when high quality pellets were fed. This may explain why feed manufacturers place pellet quality as a high priority. It is also an area in which the industry is continually trying to make improvements.
Pellet quality testing
If one assumes that pellet quality has some influence on animal performance, then an accurate, precise, and objective assay is necessary to document that influence. Pellet quality can be measured using several methods. Indirect methods such as the Stoke's® Tablet Hardness Tester (Britsol, PA) (developed for the tablet industry) was one of the first tests used in the feed industry (McCormick and Shellenberger, 1960).
Indirect testing methods allow feed manufacturers to make predictions of pellet quality immediately after the pellet mill and therefore make adjustments accordingly. Young (1970) developed the tumbling box test, which has become an industry standard for measuring pellet quality.
The pellet durability index (PDI) (ASAE S269.3) was developed as a predictor of pellet fines produced during mechanical handling. Young (abid) reported a correlation of R=0.967 and 0.949 for hot pellets and pellets cooled for 24 hr. respectively, using the tumbling can as a predictor of pellet fines. Methods which measure individual pellets resulted in the lowest correlation (Stokes, R=0.78; Shear test R=0.72).
The Holman Pellet Tester (Holman Chemical Ltd, United Kingdom) is a pneumatic, rather than mechanical, method of measuring the durability of pellets. Pellets are transferred through tubes with high velocity air to model the handling process (MacMahon and Payne, 1981). McEllhiney (1988) reported the Holman Pellet Tester gave consistent results, however, pellet durability results were lower than the values obtained from the tumbling can method (ASAE, 1987). The use of indirect methods for predicting pellet quality may be useful at the feed plant for adjusting equipment. However, livestock producers are concerned with the direct measurement of fines at the feeders. Fines in feeders can result in feed wastage, animal refusals, and increased feeder management.
Adhesion in pellets
Adhesion is the process by which materials are held together by a physical to chemical interaction of the material. This is accomplished by joining the surfaces of the material by melting the materials together or by applying an adhesive between them. An adhesive is defined as a material which, when applied to surfaces, can join them together and resist separation (Wake, 1976). It should be obvious that in pelleting, we seldom "apply" an adhesive; however, we do try, through temperature and moisture control, to activate the natural adhesives that are typically found in the feed ingredients.
Several theories on the mechanism of adhesion at the interface between particles have been proposed. The theories with application in the pelleting process include: + Mechanical interlocking + Diffusion + Adsorption Kinlock (1987) described the basic concepts of each theory and the mechanisms by which adhesion occurs. Mechanical interlocking is based on the fact that adhesives flow into rough surfaces, become rigid, and hold the materials together. The theory also suggests that rough surfaces will improve the contact area and thus improve bond strength. The diffusion theory is based on the diffusion of polymers at the interface between material surfaces. Diffusion occurs when materials are heated and allowed to diffuse across the interface between materials.
This phenomenon can occur only when the temperature of the polymer is above the glass transition temperature of the polymer. Adsorption adhesion occurs due to interatomic and intermolecular forces established between atoms and/or molecules at the surface of the adhesive and the substrate. The attractive forces are ionic, covalent, hydrogen bonding dipole interactions, and Van der Waal forces. The bond energies of the forces and effective ranges have been summarized by Allen (1990).
Rheological characteristics of feed ingredients
The rheological and functional characteristics of feed ingredients vary depending on their physical structure (crystalline vs amorphous) and chemical composition. Materials that are heated go through either a first or second order glass transition or a combination of first and second order transitions. First order transitions involve the melting of crystals, whereas second order transitions are a relaxation of polymers. Crystalline materials (e.g. sugar) go only through a first order transition. Partially crystalline materials (e.g. starch) go through a second order transition prior to the first order transition. Amorphous materials (e.g. cellulose, lignin) exhibit only a second order transition. The temperature at which the amorphous regions of a polymer begin to relax or become mobile is defined as the glass transition temperature.
Glass transition temperatures have been reported for starch (Zeleznak and Hoseney, 1987); wheat gluten (Slade, 1984; Hoseney et al., 1986), and for corn gluten (Lawton, 1992). Glass transition temperature is inversely related to moisture content. As the moisture in the system is increased, the temperature at which the material becomes mobile decreases. Feed ingredients have glass transition temperatures below the temperatures normally associated with the conditioning process (70-90° C) when the moisture content is between 15 and 18%. This suggests that feed ingredients begin to flow during the conditioning and pelleting process, and the amount and location of material flow depends on the temperature and location of the water (surface or intra-particle).
The level of total pellet starch gelatinisation and starch damage has been reported to be negatively correlated with pellet quality (Stevens, 1987; Lopez, 1993). Starch damage was found to be greater at the outer surface of the pellet at lower conditioning temperatures. However, starch damage decreased as the conditioning temperature increased, indicating that the damage was primarily due to mechanical shear between the die surface and the starch and not due to hydrothermal elevation alone.
Woods (1987) examined the functional role of starch and protein in the pelleting process. The addition of raw soybean flakes increased pellet quality as compared to heat treated denatured soybean meal. In addition, pre-gelatinised starch improved pellet quality compared to native starch. Woods concluded that protein had a greater influence on pellet quality than starch. This finding has been recently confirmed by Briggs et al. (1999).
The data suggests that the level of starch gelatinisation may not be as important as the location of the gelatinised starch. It is apparent that the gelatinisation at the surface of the feed particles is critical to the formation of intra-particle bonds necessary for the formation of strong, durable pellets. Starch gelatinisation at the particle interface in conjunction with protein plasticisation would result in polymer diffusion between starch granules and protein molecules, resulting in adhesion to the particles.
Effect of formulation
Least-cost formulation is designed to meet the nutritional parameters required by the target animal. However, the effect of formulation on processing, specifically pelleting, is seldom considered by most nutritionists. Ingredients currently used by the feed industry have been used as adhesives for over 100 years. The addition of fat to the mash pre-pellet usually results in decreased pellet quality (Richardson and Day, 1976; Headly and Kershner, 1968). However, the addition of protein and fibrous materials increase pellet quality. Fahrenholz (1989) reported an increase in the pellet durability of swine diet pellets and the level of wheat middlings increased from 0 to 45%. McKee (1988) increased pellet quality and water stability of catfish diets by increasing the level of wheat gluten from 0% to 10%. Lopez (1993) also reported the addition of vital wheat gluten resulted in a positive affect on pellet quality and water stability, but the addition of cassava meal had a negative effect. Lawton (1989) reported a linear increase in tensile strength as the amount of protein in a tablet increased at the expense of starch.
Effect of particle size
Decreasing the particle size of ingredients results in a greater surface area to volume ratio. Smaller particles will have a greater number of contact points within a pellet matrix as compared to larger particles. Anand (1970) demonstrated contact points between polystyrene beads increased 3 to 4 to 7 as bead size decreased to allow 3, 4, or 7 particles per unit area, respectively.
Penetration of heat and moisture to the core of a particle can be achieved in a shorter amount of time with small particles and a large surface area per unit of weight. Stevens (1987) reported no difference in pellet quality when the mean particle size of corn and wheat was reduced from 1023 to 551 microns (Ý) and from 802 to 365 Ý, respectively. Martin (1983) reported similar results using corn and grain sorghum. However, Wondra et al (1995) reported an increase in pellet durability as particle size was reduced from 1000 to 400 Ý. The aquaculture feed industry will typical grind ingredients to less the 250 Ý for greater pellet water stability. The combination of small particle size and long term, high temperature conditioning produces pellets that have the greatest water stability.
Conditioning
The importance of steam conditioning was quantified by Skoch et al (1981) in an experiment comparing dry pelleting with pelleting using steam conditioning. The results of this study indicated that steam conditioning improved pellet durability and production rates and decreased the amount of fines generated and energy consumption. From this, it was concluded that steam acted as a lubricant to reduce friction during pelleting.
Mash entering the conditioner may be comprised of a wide variety of ingredients that make up the diet formulation. The nutritional, as well as physical properties of this mash have an effect on conditioning and eventual pellet quality. According to Reimer (1992), pellet quality is proportionally dependent on the following factors: 40% diet formulation, 20% particle size, 20% conditioning, 15% die specifications, and 5% cooling and drying (Figure 1). If this is correct, 60% of pellet quality is determined before the mash enters the conditioner. This increases to 80% after conditioning, but before mash has even entered the die chamber of a pellet mill.
There has been some research conducted looking at the effects of the first two of these variables, diet formulation and particle size, on pellet quality. Studies by Stevens (1987) and Winowiski (1998) have compared the pellet durability of diets containing corn with those where some or all of the corn was replaced with wheat. In both instances, pellet durability was higher for the diets containing wheat. It can be reasoned that this is due to the higher crude protein content of wheat (at 13%) as compared to corn (at 9%). This finding is in agreement with a study conducted by Briggs et al. (1999) which found that increasing the protein content in a poultry diet from 16.3% to 21% increased the average pellet durability from 75.8 to 88.8%.
Particle size is the second factor that Reimer (1992) proposed would dictate about 20% of pellet quality. Decreasing particle size from a coarse to a fine grind exposes more surface area per unit volume for absorption of condensing steam and increases the surface area available for bonding. MacBain (1966) indicated that a variation in particle size produces a better pellet than a homogeneous particle size. Work by Stevens (1987) when pelleting corn or wheat based diets, however, found that particle size had no effect on pellet durability index (PDI) as determined by the tumbling can method.
Conclusion
After reviewing the body of published scientific literature as well as reports from field studies and skilled practitioners of pelleting, it is easy to conclude that there is still a great deal of art in the science of pelleting. There is truly a great deal that we don't understand or, perhaps, that we misunderstand about pelleting. Reimer (1992) indicated that the factors that affect pellet quality can be identified as: formulation, particle size, conditioning, die specification, and cooling and drying. If his hypothesis is true, these allocations provide a useful roadmap to solving many of the quality problems associated with pelleting.
Dr. Keith C. Behnke, Department of Grain Science and Industry, Kansas State University, Manhattan, Kansas, USA
Literature cited
ASAE. 1987. ASAE Standard S269.3, Agricultural Engineers Yearbook of Standards. p 318. American Society Agricultural Engineers.
Allen, K.W. 1990. In: Industrial Packing Adhesives. Ed. K.S. Booth. CRC Press Inc. Boca Raton, FL.
Anand, J.N. 1970. Adhesion and the formulation of adhesives. Ed. Wake, W.C. Applied Science Publishers Ltd. London.
Behnke, K.C. 1994. Maryland Nutrition Conference. Dept. of Poultry Science and Animal Science, College of Agriculture, University of Maryland, College Park.
Briggs, J.L., et al. 1999. Poultry Sci. 78:1464-1471.
Fahrenholz, C.F. 1989. PhD. Dissertation, Kansas State University, Manhattan.
Falk, D. 1985. Feed Manufacturing Technology III. Ed. R.R. McEllhiney. American Feed Industry Assn. Arlington, VA.
Gill, D.R. and J.E. Oldfield. 1965. J. Anim. Sci. 24:599 (Abstr.).
Hanrahan, T.J. 1984. Anim. Feed Sci. Technol. 10:277.
Headly, V. and R. Kershner. 1968. Feedstuffs 40(30).
Hoseney, R.C., K. Zeleznak, and C.S. Lai. 1986. Cereal Chem. 63:285.
Hull, S.J., et al. 1968. Poultry Sci. 47:1115.
Hussar, N. and A.R. Robblee. 1962. Poultry Sci. 41:1489.
Kinlock, A.J. 1987. Adhesion and Adhesives Science and Technology. Chapmand and Hall. New York, NY.
Lawton, J.W. Jr. 1990. Ph.D. Dissertation. Kansas State University, Manhattan.
Lawton, J.W. 1992. Cereal Chem. 69:351.
Lopez, J.G. 1993. Ph.D. Dissertation. Kansas State University, Manhattan.
MacBain, R. 1966. American Feed Manufacturers Association. Arlington, VA., pp. 1-28.
MacMahon, M.J. and J.D. Payne. 1981. The Holmen Pelleting Handbook. Bradley and Sons Ltd. Berkshire, England.
Martin, S.A. 1983. First International Symposium on Particle Size Reduction in the Feed Industry. Kansas State University, Manhattan.
McCormick F.J. and J.A. Shellenberger. 1960. Feedstuffs 32(11).
McEllhiney, R.R. 1988. Feed Management 39(6):37.
McKee, J.W. 1988. M.S. Thesis. Kansas State University, Manhattan.
Moran, E.T. 1989. Recent Advances in Animal Nutrition. Butterworths, London.
Proudfoot, F.G. and A.E. Sefton. 1978. Poultry Sci. 57:408.
Proudfoot, F.G. and H.W. Hulan. 1982. Poultry Sci. 61:408.
Reimer, L. 1992. Proc. Northern Crops Institute Feed Mill Management and Feed Manufacturing Technol. Short Course. p.7. California Pellet Mill Co. Crawfordsville, IN.
Reimer, L.L. and W.A. Beggs. 1993. Feed Management. 44(1):22.
Richardson, W. and E.J. Day. 1976. Feedstuffs 48(20):24.
Salmon, R.E. 1985. Anim. Feed Sci. Tech. 12:223.
Scheideler, S.E. 1991. Proc. of the Carolina Poultry Nutrition Conf., Carolina Feed Industry Assn., Sanford, NC.
Schoeff, R.W. 1994. History of the Formula Feed Industry. In: R.R. McEllhiney, Ed. Feed Manufacturing Technology IV. American Feed Industry Association. Arlington, Virginia: 7.
Skoch, E.R., et al. 1981. Anim. Feed Sci. Tech. 6:83.
Slade, L. 1984. American Association of Cereal Chemists. 69th Annual Meeting, Minneapolis, MN. (abstr.).
Stark, C.R. 1994. Ph.D Dissertation. Kansas State University. Manhattan.
Stevens, C.A. 1987. Ph.D. Dissertation. Kansas State University. Manhattan.
Tribble, L.F., et al. 1979. Proceedings of the 27th Annual Swine Short Course. Texas Tech University, Lubbock.
Wake, W.C. 1976. Adhesion and the Formulation of Adhesives. Applied Science Publishers Ltd. London.
Winowiski, T. 1998. Proc. Kansas State University/American Feed Industry Assoc. Pellet Conference. Manhattan, KS. July 11-13.
Wondra, K.J., et al. 1995. J. Anim. Sci. 73:757-763.
Woods, J.F. 1987. Anim. Feed Sci. Tech. 18:1.
Young, L.R. 1970. M.S. Thesis. Kansas State University, Manhattan.
Zeleznak, H.J. and R.C. Hoseney. 1987.. Cereal Chem. 64:121.
PhasePigsADGADFIG/FADGADFIG/FCommentGill and Oldfield(1965)Grow/Finish320.983.130.311.022.920.35Poor quality pellets did notimprove performanceJensen and Becker(1965)Nursery960.270.440.620.240.370.65Pelleted diet NCR 42 (1969) Swinenutrition (1969)Grow/Finish5560.77 0.310.78 0.323% ^G/FHanke et al. (1972)Grow/Finish3790.752.520.290.80 0.316%^ADG&G/FBraid (1973)Nursery/Finish1200.69 0.270.722.430.304%^ADG, 7%^G/FTribble et al. (1979)Grow/Finish1920.662.540.270.68 0.293%^ADG, 7%^G/FTribble et al. (1980)Grow/Finish1440.622.350.240.702.60.2712%^ADG&G/FHarris et al. (1980)Grow/Finish950.61 0.260.662.180.30Quality pellets, 8%^ADG, 15%^G/F 2.28 0.662.510.26Poor quality pellets8%^ADGTribble et al. (1980)Grow/Finish1200.67 0.290.712.100.34Pellets, 6%^ADG, 17%^G/F 1.35 0.732.160.34Pellets plus binderSkoch et al. (1983)Nursery480.612.790.450.671.360.499%^ADG &G/F Grow/Finish480.75 0.270.792.890.275%^ADGHanrahan (1984)Grow/Finish680 0.4861.940.25Pellet durability, 69% 0.4921.940.25Pellet durability, 62%Walker et al. (1989)Nursery 0.310.66 0.550.7311%^G/FWondra et al. (1994)Finish1600.963.220.301.003.160.324%^ADG, 6%^G/F