Introduction
The animal feed manufacturing industry’s main purpose is to recombine different flows of nutrients into safe, nutritious, attractive and handleable feeds which are efficiently converted in animal-sourced food products (meat, eggs, milk). The raw materials harboring these nutrients vary greatly in composition and origin. Raw materials may be co-products sourced more locally from food or biofuel industries whereas others may travel large distances on the globe, depleting nutrients in one region, and leaving excreted components like nitrogen and phosphorus in animal-dense regions resulting in profound challenges for, and negative impact on the environment at a global scale (IPC, 2022). The capacity of the feed manufacturing industry to transform the great diversity of raw materials into quality animal feed is crucial for the efficiency of our food system. For this, manufacturers have implemented various processing technologies to assure feed quality (Thomas and Van der Poel., 1996; Thomas et al., 1997; Van der Poel et al., 2018). Each unit-operation entails a processing step that requires energy and resources, and it is of interest to improve processes, where possible, to minimize costs and environmental impact while also assuring feed quality. Piecemeal engineering brought such improvements in feed manufacturing technology in terms of enhancing process performance and feed quality. Examples are the appearance of expanders in the ‘90s, Post Pelleting Applications of liquid additives, the appearance of new types of mixers (twin- and single shaft paddle mixers) which slowly replace the ribbon mixer as the mixing work horse in the industry, and improvements/enhancements/additions to this equipment to make production of animal feed better suited to the requirements of the feed manufacturer. To further enhance and optimize future feed production Van der Poel et al. (2020) indicated several relevant areas such as accurate and fast testing technologies to determine variability in ingredients and use of (big) data to understand and optimize feed production. The objective of this paper is to expand on this and more specifically investigate on a technical level where progress in the main feed unit-operations (milling, mixing and pelleting) may lead to reductions in operational costs (energy) while maintaining the possibility to manufacture feed with its great diversity in raw materials and coproducts. We will also look into technologies that may rework co-products or ingredients into components of an animal’s ration without the use of standard feed manufacturing unitoperations. To do so it classifies technology into ‘mitigating’ and ‘adaptive’ technology. Mitigating technology in feed manufacturing, in this paper’s context, is related to improvements in our current understanding of feed manufacturing unit operations (milling, grinding, pelleting) with the aim of improving one or more aspects of the production process such as reduction in energy consumption per tonne of feed produced, optimizing physical or nutritional quality or increasing the capacity of a production line. Adaptive technology takes into account novel ingredients and novel processing methods. In case of co-products derived from human food production, food waste, or fodder by-products, this may require additional processing steps to make nutrients more available or to assure food safety.
Mitigating technology in feed manufacturing
Milling
Milling, or grinding, together with mixing and the pelleting process, is one of the key unitoperations in feed manufacturing. Milling requires energy for breaking raw materials into smaller particles. Reasons for milling are rooted in facilitating nutrient digestion and supporting gastrointestinal functioning and health in animals whilst at the same time preparing the ingredients to obtain a more homogeneous feed mix and improving the pelleting process. The optimum particle size of feeds in terms of processing costs and animal performance and health has been evaluated for pigs (Patience 2012) and reviewed for pigs and poultry (Kiari and Mills 2019). The high relevance of particle size with respect to animal performance and feed manufacture operations warrants the question how current milling operations can be improved and what research is required to support these operations.
Within feed manufacture there are two strategies to grind raw materials, i.e. pre-milling and post-milling. In pre-milling, raw materials are ground upon entry into the factory and stored as ground materials. In principle, this permits more stringent particle size specifications according to nutritionist or feed mill requirements as raw materials can be ground separately with specific and controllable operational settings. Post-milling is the most common adopted strategy in grinding, due to lower capital costs for additional storage bins and transporting equipment compared to pre-milling. Raw materials are weighed and dosed according to recipe after which the entire batch is transported to the milling bin, up-stream of the grinding system. At this point, the mill starts working on a segregated set of raw materials entering the mill depending on dosing order. Although, in principle, the order of raw materials arriving at the mill could be estimated by the dosing order, this is not common practice. Controlling a hammer mill or roller mill consists of decreasing or increasing the flow of raw material to a pre-set motor load. With many ingredients regularly making up an animal feed, it is not uncommon in the Netherlands to have between 10 and 20 different raw materials in one batch, it means the mill is continuously adapting to the flow of the new raw material entering the mill in which case very rarely a steady state grinding situation is obtained. The fluctuation in mass flow and constant adaptation to the desired load of the motor will affect the degree of fill of the hammer mill, the flow pattern through the mill and therefore affect particle-size and nutrient distribution in ways that hitherto have not been investigated in the feed manufacturing industry.
As reducing particle size requires energy and the particle size distribution impacts the pelleting process, it is important to have a deeper understanding of how particles break under set conditions. The machine parameters (design), process parameters (operational settings) and the characteristics of the raw materials ultimately define how particle size is reduced into a specific distribution. A comparison between the amount of energy required to comminute wheat, maize and soybeans by three different mill types (roller mill, hammer mill and multicracker) using various operational settings relevant to the specific mill type, showed that energy requirements are the lowest for the crushing type of mills (e.g. roller mill and multicracker) as compared to the impact mill (hammer mill) to obtain the same mean particle size (Table 1). The total Specific Mechanical Energy load (SME) is the total amount of energy consumed including air exhaust for the hammer mill and idle-load of the motors. Effective SME is corrected for both idle running and air exhaust and is on average 35% lower than Total SME with the largest reduction in SME for the hammer mill (43.8%), multicracker (32.8%) and roller mill (27.7%), respectively. This shows that changes in mill type or comminution principle can reduce energy requirements in grinding. Thomas et al. (2018) also showed Kick’s constant values for these three different mill types and three different feed raw materials. The development of breakage equations for single feed raw materials would be instrumental for tailoring particle size requirement to animals and optimisation on lowering the energy input in milling. This would also be of benefit for post-mill grinding applications as the raw materials arrive as individual components to the mill. For a limited number of feed ingredients breakage equations have been established. For the roller milling of wheat such a breakage equation has been established by Fang and Campbell (2003a ), where the breakage equation included shape, size, moisture, and hardness values of the wheat kernels.
Table 1. Energy requirements (Kick’s constants: kJ/kg) for three different mill types (hammer mill, roller mill and multicracker) in grinding of maize, soybeans and wheat (Adapted from Thomas et al., 2018).
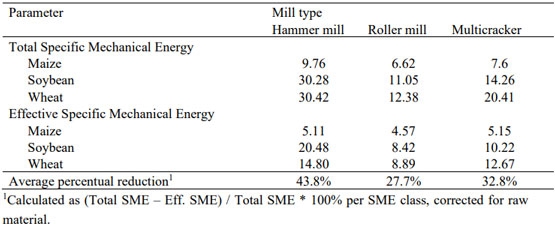
Mass Population Balance Models (MPBM) predict the particle size distribution of the ground material as a function of the incoming raw materials particle size distribution and a breakage equation. This breakage equation estimates the redistribution of comminuted particles over the smaller size classes (Lyu, 2021). Most preferable these breakage equations contain information on breakage behaviour of the raw materials and the equipment being used. The use of MPBM in milling is well established in pharmaceuticals (Diemer, 2021) and chemical industry (Vogel and Peukert, 2005) to predict the particle size distribution of the ground material as a function of the incoming raw materials particle size and in many cases to obtain an estimate on the amount of grinding energy involved. The use of MPBM in milling operations in feed manufacturing on mixtures or batches of feed ingredients has not been done. However, grinding of individual raw materials which are used in the feed industry have been analysed. MPBM have been described for maize in hammer mills (Cotabarren et al. 2020), for wheat in roller mills (Fang and Campbell, 2002, 2003a , 2003b ; Fistes and Tanovic, 2006; Galindeze-Najera, 2014; GalindezeNajera et al., 2016), the latter because of the large interest in the topic from the flour milling industry. Cotabarren et al. (2020) uses a more general approach in which required parameters in the breakage function are fitted from experimental data to predict breakage of maize in a hammer mill.
Finally, multistage grinding in which a combination of classification and (re-)grinding is used may further enhance required particle size distribution in the feed mash whilst reducing energy consumption (Lucht, 2011).
Mixing
Mixing, together with milling is the main unit-operation in a feed plant. Mixing as a unit-operation has been well described, usually in association with the problem of demixing/segregation occurring after mixing (Poux et al., 1991; Ottino and Khakhar, 2000; Mosby et al., 1996). In terms of energy use, mixing requires less energy compared to milling and pelleting, and it is of interest to minimize mixing time to increase the capacity of a production line. Furthermore, it is evident that mixing is crucial as heterogenous and unbalanced feeds can depress animal performance and health, reduce nutrient utilization efficiency and, consequently, increase spillage of nutrients to the environment. Physical factors that affect blending or segregation of feed particles have been described by Axe (1995) and Tang and Puri (2004) and contain particle associated factors and dynamic factors. Examples of dynamic factors include rise or fall of particles due to vibration, elutriation of small particles due to upward air displacement, and tribocharging.
Issues in dry mixing of feed materials are usually associated with inhomogeneous distribution of particles or nutrients during mixing. Even though a homogeneous mix can be achieved in the mixing stage, subsequent transport and storage operations will lead to segregation of the dry mix. Root causes responsible for demixing are, in order of relevance – most relevant factor first: i.) differences in particle size, ii.) density differences between particles, iii.) interactions between specific components or iv.) degree of agglomeration (Deveswaran et al., 2009). In the feed industry a large variety of particle size ratios, density between particles, chemical or physical interactions, and agglomeration between feed mash particles is present, which originates from both the large number of feed raw materials used and the wide range of particle size characteristics (size and shape) emanating from the milling process. Reducing problems in mixing, therefore, requires similar particle size, a high particle number, similar shape and density, a minimal amount of dust, and good flowability (Axe, 1995). Based on the large differences in these traits in both heterogenous raw materials and premixes, these conditions will never be met in feed manufacturing. Free flowing mixtures are easy to mix but suffer from post mixing processing, where these same properties promote segregation. Cohesive mixtures are more difficult to mix, but once mixed have a lower tendency towards segregation (Deveswaran et al., 2009). Ordered mixing is the process in which mechanical, adhesion, electrostatic or coating forces are used to prepare ordered units (Saharan et al., 2008) which after mixing show a lower tendency to segregate. The process involves breaking up of the finer or smaller component and binding these fine components to the coarser carrier (Figure 1).
Figure 1. Various steps in the process of ordered mixing (Saharan et al., 2008).
In addition, the order of mixing may influence the mixing process and ease of particle dispersion as a function of particle size and cohesive properties of the particles. This has been shown for a pharmaceutical three component system containing Avicel, aspirin and povidone 90, where required mixing time was shorter if povidone was added before the aspirin, as measured using a Near Infra-Red (NIR) system (Bellamy, 2008). A simulation of two discrete sized particle types showed that dosing the larger particles after the smaller particles led to reduced mixing times and better mixing (Xiao et al. 2015). To what extent these results are transferable to formulations with multiple raw materials in a feed manufacturing system is currently not known.
We, the feed industry, need to improve our understanding of obtaining a homogeneous mix in terms of nutrients whilst reducing energy use in the mixing process and reduce processing times in the factory. In addition, this need becomes more pertinent when future feed formulations containing more fibrous co-products with difficult handling properties are used. With respect to mixing in the feed industry (both premix and complete feeds) the following directions of research may provide us with information on how to better mix our materials: i) Order of mixing, where the dosing order in the mixer is determined by its particle characteristic(s) e.g. size and distribution. This would require a further integration with the milling operation as well. ii) Adding liquids (hydrophilic: water, molasses, sugar syrups; and hydrophobic: fats and oils) with respect to order and time in the mixing process to make maximum use of these liquids as binders of fine particle material. As such the concept of ‘ordered mixing’ as used in the pharmaceutical industry may be adopted. Ultimately, the outcome of such research is the manufacture of nonsegregating feed mashes, which may make the use of pelleting as a fixation process for the structure of particles, obsolete.
Pelleting
The pelleting process typically entails the conditioning of a mash, followed by compaction through a die and subsequent cooling of the pellets obtained. Concepts related to conditioning, pelleting and cooling have been discussed in Thomas and Van der Poel (2020). Relevant contributing factors to a deeper understanding of the pelleting process and resulting pellet quality traits are the interaction between moisture, temperature and residence time given certain physicochemical properties of the original feed mash (e.g. chemical composition, particle size distribution). In addition, the dynamics in moisture and temperature alter the physico-chemical properties in the raw material constituents, which affect the energy required to push pellets through the die and the overall observable quality trait characteristics of the formed pellets. The connecting element between processing conditions and physico-chemical changes is the statephase diagram for relevant raw material constituents. With use of state-phase diagrams interactions between processing conditions and subsequent changes in raw material components can be understood and used as guiding framework in understanding resultant quality traits. For wheat flour and its components gluten and starch, examples on the use of such a state-phase diagram are given by Cuq et al. (2003). Taking native starch as an example, increasing the moisture and/or temperature will result at some point in a change from the glassy state to the rubbery state for those polymers which are in an amorphic state. Typically, these changes occur already at room temperature with moisture levels in the range of the base moisture level of many raw materials used (e.g. between 8 – 12%). Increasing the moisture level will lower the glass transition temperature. Despite different sources in raw materials for starch, it follows that many of the changes of state for starch can be described according to the state-phase diagram given in Figure 2 (Van der Sman and Meinders, 2010). The heterogeneous structure in proteins as for instance in pulses or animal proteins, leads to a broader range of glass-transition phenomena as compared to starch rich raw materials, e.g. rice or corn. Starch at the outer part of a particle will be the first to change states and depending on temperature, moisture and time, starch in the inner parts of the particle may change states given sufficient diffusion of moisture to the particle interior within the permitted (residence) time of the equipment (Thomas and van der Poel, 2018).
Starch in a rubbery state (above the glass transition) can deform during compaction, allowing particles to stack more densely and flow differently through the die, compared to starch below the glass transition which behaves as hard and brittle material. These changes translate to a certain amount of (mechanical) energy required to produce pellets. Furthermore, when particles are stacked more densely, there is more opportunity for interparticle bonds to form. During cooling, temperature and moisture drop, leading to a change from rubbery back to glass state. Both a combination of deformed particles and solid bonds appearing at the contact planes between particles affect the final physical pellet quality. To advance our understanding how to effectively pellet feed particles varying in composition, more information is required to build similar diagrams for the different proteins, fibers and other polymeric components present in raw materials. A better insight in the dynamic sorption or diffusion of heat and water in feed mash particles is also required to properly align with information provided in the (static) state-phase diagrams of feed raw materials. Moreover, for single raw materials such diagrams may have limited application in practical feed manufacturing yet. A framework needs to be established for mixtures of raw materials and how physico-chemical changes in individual raw materials contribute to overall behavior of the mix of interacting raw materials in conditioning, pelleting, cooling, and resultant pellet quality.
Figure 2. State-phase diagram of starch showing various moisture and temperature conditions at which changes of state occur. Included in the diagram are various changes of state relevant in compound feed manufacture as e.g. the glass-transition, melt-transition line and gelatinisation line (Van der Sman and Meinders, 2010).
Adaptive technology in feed manufacturing
Where mitigating technology investigates and refines current feed manufacturing practices, adaptive technology is focusing on new methods and procedures in feed manufacturing. Such processing technologies can include grinding, toasting, baking, infrared radiation, flaking, steam cooking, expander processing of single ingredients in combination with pelleting and extrusion cooking to enhance their nutritional value. For example, for fibrous feedstuffs these have been investigated by De Vries et al. (2012). The individual treatment of feedstuffs warrants the question to what extent energy (electric, thermal) increases the digestibility of the by-product and if this increased (fossil fuel) energy consumption outweighs the enhanced nutritional performance. New methods and procedures in feed manufacturing are also required to accommodate the ever-changing availability of feedstuffs. In the future, primary products like cereal grains will be exclusively used for human food production. Higher levels of co-products derived from these ingredients become available as feed raw material (van Zanten et al. 2019). These encompass products such as hulls, middlings and pulps made from whole raw materials soy, wheat or citrus products. These co-products are typically rich in protein (meals) and/or fiber (brans, pulps) and low in starch and oil (FEFAC, 2019). Co-products from such processed human food ingredients become depleted in terms of digestible nutrients, richer in fiber and, usually, have poor handling characteristics. The supply and quality of these co-products will be more diverse, and most likely with different functional properties in unpredictable quantities, depending on processing origin. Manufacturers will have to be more flexible and able to handle more heterogeneous ingredient mixtures, both in nutritional and in handling properties. This makes detailed knowledge of the physico-chemical processes important for effective use of the co-products in quality pelleted animal feeds. Currently in the Netherlands, co-products are derived from a.o. the potato industry (potato steam peelings, potato-starch, off-spec fries), flour milling industry (wheat bran, wheat middlings, wheat gluten feed, liquid wheat starch), bakery products (bread meal, off-spec cake and chocolate-cake meal), fermentation industry (wet corn or wet wheat separation processing (DDGS), yeast concentrates), dairy industry (permeates, milk concentrates, milk powders), and from the brewing industry) (yeast, brewery spent grains). In addition, trimmings and off-spec foodstuffs not suitable for human consumption and non-sold food products from e.g. supermarkets enter the feed chain. Finally, and though currently prohibited in Europe as a feed ingredient due to food safety measures, kitchen leftovers (swill) from e.g. restaurant or canteens which have a high feeding value especially for pigs and poultry (Westendorf, 2000) may re-enter the feed chain. If the quality and safety of these product can be guaranteed, these products might become, again, available for feed manufacturers. These energyrich, low fiber products contain high levels of starch, sugars, proteins, and/or fats as compared to high fibrous co-products from processed human food ingredients. Table 2 shows a small portion of co-products generally included in feed rations where a large part of the wet products is not included in pelleted feed.
Table 1. Examples of the chemical composition of wet by-products originating from different human food industries and used in animal feed production.
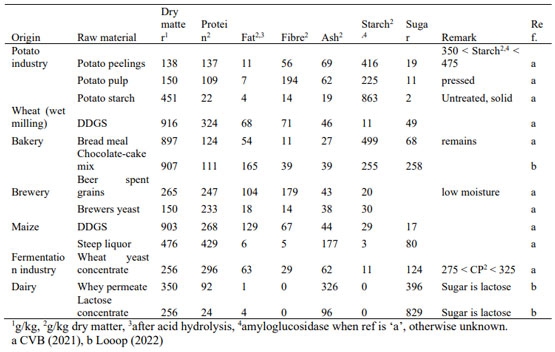
Many of the available dry (> 88% dry matter) co-products are easily used in combination with the current feed manufacturing practice. This is, after all, at the core of existence of feed manufacture, increasing the value of edible waste streams and co-products by standardization and turning this mix in a handleable form (pellets). Wet streams (< 75% dry matter) as such, however, are generally not included in pelleted feeds for a number of reasons: i.) blending high moisture feed raw materials with dry ingredients leads to lumping and caking of feed material on the inside of mixers and transport elements leading to problems in transport and sanitary status of the feed(-mash) due to microbial and mold formation. ii.) a high level of free moisture in feed mash leads to blocking of the pelletizer. The base moisture level of feed ingredients plus added moisture from condensing steam, in practice, does not exceed 18% moisture level after which blockage of the pellet press may occur. This limits the use of moist co-products in dry feed mash for pelleting. The use of an expander permits higher moisture levels, since expanders tend to run more stable at elevated moisture levels. Expanders permit to run to moisture levels of the feed mash up till 30% (Mościcki, 2011). However, if the expander is used in combination with a pelletizer, still the upper moisture limit should be respected in order to prevent blockages of the pelletizer. iii.) The whole concept of feed manufacture rests on being able to reduce the moisture and heat-content of the hot pellets after manufacture by using the cooling process, without the addition of drying energy to actively reduce the moisture content of the pellets. The addition of heat by condensing steam and friction in the die of the pelletizer and/or heat dissipation by an expander motor introduces enough energy that pellet moisture content comes back to approximately base moisture level of the ingredients with pellet temperature within 5°C of the ambient air temperature. If more water is added, not enough energy is stored in the pellets to dry to base moisture levels. The installation of drying equipment with its high energy requirement makes the process of standard feed manufacture uneconomical and prevents the inclusion of more free water possibly derived from wet co-products.
Adaptive technologies are therefore required to (further) upcycle these resources as feedstuffs in the food chain. Such new methods, procedures and techniques aim to facilitate the use and/or to increase the nutritional value of certain (novel) ingredients or co-products as originating from human food industry. Figure 3 shows technology possibilities for high fibrous co-products when moving from wet to dry state and the possible technologies that can act upon these co-products during transition from wet to dry. In addition, it shows technology options when leaving such coproducts in the wet stage. These include, amongst others, enzymatic, fermentation, ensiling and fungi treatment of such products. For example, the application of enzymes to modify raw materials in the processing chain of feed manufacture is hampered by the high required moisture content and residence time to bring about the desired effect. Wet milling processes like starch production do incorporate separation stages at elevated moisture contents in which, in principle, additional enzyme modification steps could be introduced. Enzymes can also be added to (spontaneous) fermentation process to increase efficiency of this process and target specific ANFs or nutrients (Goodarzi Boroojeni et al., 2017, Zentek and Boroojeni, 2020). Treating large volumes of wet, fermented co-products is traditionally not incorporated in the current industrial wet separation processes. Further processing of these co-products on farm level seems to be most logical step in further increasing its feeding value.
Figure 3. Principles of operation for adaptive technologies (see text).
White rot fungi can be used to degrade lignin in lignocellulosic biomass to improve the availability of the cellulose and hemi-cellulose components for either ruminant nutrition or biofuel production (van Kuijk, 2016). Although the technology is low cost, simple and environmentally friendly, loss of carbohydrates during the process of fungal incubation requires further study and optimization of the technology to be used in large scale feed applications (van Kuijk, 2016). Prior to the drying stage but after enzymic or fermentative stages, wet co-products may be subjected to other thermal technologies such as extrusion, expander treatment, or wet-milling to modify these co-products into higher nutritional value products.
The economic value for high-energy, low fibrous wet co-products and food waste permits drying (including homogenization, standardization and hygienization) of these products. This makes these products suitable for inclusion in standard feed manufacturing operations. For example, Japan and South Korea collect and heat-treat swill and upcycle in total 36% and 43% of the food leftovers (Sugiura et al., 2009; Zu Ermgassen et al., 2016). In many cases, such co-products are included in sensitive stages of animal production like young animal feeds, since often such feeds include high levels of sugars and fats which are desirable to enhance feed intake and energy level.
Much of the focus in animal nutrition is on replacing soy as protein source for alternative protein rich feed ingredients. Tallentire et al. (2018) investigated micro- and macro-algae, duckweed, yeast protein concentrate, bacterial protein meal, leaf protein concentrates and insects as alternative novel feed ingredients. Using a modelling approach, they found that soybean products could be replaced by the novel feed ingredients while at the same time reducing greenhouse gas emissions and arable land requirements, pending sufficient upscaling of the production processes. To reduce drying costs, it is of interest to either build processing plants at places where residual heat from industrial processes can be transferred and used to dry these novel feedstuffs or further integration of the production of such novel feed ingredient with energy production (e.g. biodiesel or bio ethanol for drying). In addition, improving the drying process may additionally lead to claimed reductions of up to 65% in net energy for drying (Geelen, 2022).
Feed manufacturing is one of the most viable and efficient industries to upcycle co-products and incorporate novel feed ingredients into valuable animal products. The increases in variability in future feed raw materials with reduced nutrient content and poor handling properties, combined with societies demand for reduced greenhouse gas emission and energy consumption pose new challenges for the feed manufacturer. Part of the solution lies in further upstream integration with suppliers of (novel) feed ingredients and further refinement and understanding of the current unit operations.
Take home points
- Post mill grinding as currently executed, limits control over the resulting particle size of the ground raw materials. As a result, changes in dosing order to the mill may affect particle size distribution of a raw material to an unknown extent.
- The effects of dosing order according to particle size or cohesive properties on mixing time and homogeneity have not been assessed for animal feed.
- Addition of liquids during the mixing stage may be combined with the concept of ordered mixing, to reduce segregation and improve homogeneity of the feed. Investigations on how to best dose, in terms of time, order of hydrophilic and hydrophobic liquids in addition to equipment design (mixer and liquid dosing system) should be set up.
- Combining process conditions with state-phase diagrams enhances our understanding of the interactions between conditioning, pelleting, cooling and functional properties of feed raw material components. Currently, information is lacking to include dynamic behavior e.g. sorption or diffusion of heat and water in feed mash particles to properly align with information provided in the (static) state-phase diagrams of feed raw materials.
- There’s an upper limit in moisture content in standard feed manufacturing practice of about 18% moisture. Higher moisture levels lead to blocking of the pelletizer. In addition, residual heat in the hot pellets is not high enough to reduce the moisture content to the original raw materials base moisture level (usually between 8 – 12% moisture). This limits the inclusion of wet co-products.
- Increasing the nutritional value of high-fiber co-products in the wet stage by processes such as wet milling or enzymic treatment is paramount for upcycling. If, as part of the production, energy carriers like bio-ethanol or bio-diesel are produced, an economical combination with drying is possible.
Presented at the 2022 Animal Nutrition Conference of Canada. For information on the next edition, click here.