Introduction
The poultry industry represents an increasingly intensive operation supplying high quality protein in the form of eggs and meat. The efficiency of production has increased dramatically to meet the increasing demand for high quality food for the world population.
In the United States, as well as in most developed and developing countries, animals are being slaughtered for further processing to supply ready-to-cook or cooked items. Further processing results in by-products that need to be disposed of. The options for disposal are limited and costly. They include incineration, burial and landfill dumping, composting, and rendering.
Concern about these activities' impact on the environment has led the Environmental Protection Agency in the United States and similar agencies in other countries to enforce stringent regulations that may eliminate the current practices of burial, landfill dumping, and incineration. Although composting represents a more acceptable method of by-product disposal, its future is uncertain because of concern about how it is done and how to use the compost itself.
The fourth option, rendering, more efficiently utilizes by-products' nutritional value, but it cannot always be economically justified. Most poultry processors choose not to operate their own rendering plants because such a plant has a high capital cost and a capacity far in excess of the processor's needs. Thus the poultry industry often gives away its valuable by-products to conventional renderers at a negative cost. The renderers, on the other hand, can choose which by-products to accept and which to refuse, often leaving the processor with the original dilemma of disposing of by-products.
Dry extrusion technology may provide an avenue for the poultry industry to economically process these by-products in an environmentally sound way.
An alternative method
A major layer breeder company was faced with an excessive amount of hatchery waste from its breeder operation, consisting of eggshells, infertile eggs, and unhatched embryos. Disposing of an average of 2 tons of waste per day cost over $lOO,OOO per year in trucking charges and landfill fees, in addition to in-plant labor costs to separate and bag the waste. The company was forced to discontinue this practice in August 1995, when the landfill stopped accepting hatchery waste. Fortunately, the company had been building an extrusion plant to process its by-products. The plant went into full production in August 1995.
The following flow chart describes the process:
Hatchery Waste - Vacuum System - Homogenizer - Carrier Bin (Soybean Meal)- Mixer - Live-Bottom Bin - Dry Extruder Thermal Dryer - Cooler =s Fished Product Bin.
The company adopted a biosecurity protocol that included an underground vacuum system to bring hatchery waste to the by-product processing plant. The plant was designed to prevent cross contamination and assure wholesomeness to the finished product. Table 1 shows the complete nutritional profile of the extruded by-product (Hy-Pro Meal). The product is sold as a feed component for a commercial layer operation and a protein supplement for beef. The company is now expanding its extrusion plant to process spent hens.
Table 1. Hy-Pro MealA (Typical analysis, as is basis)1
AHy-linen international, 1915 Sugar Grove Avenue, Dallas Center, IA 50063, Phone; (515) 992-3736
BAll values are typical analytical results and not guaranteed levels
By-product processing through extrusion
The dry extruder was developed in the early 1960s to process soybeans and grains. It utilizes friction as the only source of heat to cook, sterilize, and dehydrate products. Dry extrusion works by generating high temperatures in a short time (under 30 sec), as well as high pressure (estimated at 40 atmosphere). Cells are ruptured when the product leaves the extruder. The rupture of cell walls frees moisture from inside the cells, yielding an easily dehydrated final product. The moisture is then reduced by a thermal dryer to about 10% prior to cooling and storing the finished product.
Most poultry by-products contain high moisture and cannot be effectively dried or dehydrated without adversely affecting their nutritional value. Diluting the by-product with an ingredient such as soybean meal, corn, or wheat middlings, however, reduces its moisture to a level that the extruder can process. Extrusion can achieve full cooking, sterilization, and partial dehydration on a mixture of 5040% by-products with the dry ingredient of choice. Many universities have tested this concept with outstanding results in terms of the nutritional value of the extruded product and the performance of the animals when fed that product.
The nutritional quality of extruded by-products
The feeding value of various poultry byproducts processed through the dry extruder has been studied extensively. The following is a summary of some of those trials.
Haque [l] conducted two experiments to evaluate the use of ground whole hens in broiler starting diets processed through the Insta-Pro@ dry extruder. In both trials (Tables 2 and 3) the extruded whole hen diet improved growth rate and feed conversion in broiler chicks when compared with the unextruded corn-soybean meal control diet. They reported that no microorganisms were found in the extruded feed.
In two experiments, Tadtiyanant et al. [2] evaluated the nutritional contribution of dead broilers, dead turkeys, raw feathers, or feathers treated with a chemical and enzymatic premix. Samples of two different ages of dead birds and the two feather treatments were co-extruded with soybean meal and processed through an Insta-Pro extruder. The resulting six extruded products were used in formulating isocaloric and isonitrogenous diets that were compared with a diet containing cornsoybean meal or corn-soybean meal with commercial feather meal fed to broilers from 1 to 21 days of age.
Table 2. Performance of broiler chicks (day-old to 3-wk of age) fed extruded and unextruded diets and aerobic plate counts of these diets (Experiment 1)*
a Body weight, feed intake, and feedbody weight represent means of 4 replicates of batterypens with 10 chickslpen.
b PBM = Poultry by-product meal; FM = Feather meal; Feathers = Ground feathers fromspent hens; LSD = Least significant difference.
a-d Meanswithin the same column with no common superscript differ significantly (Pd≤05).
Table 3. Performance of broiler chicks (day-old to 3-wk of age) fed extruded and unextruded diets and aerobic plate counts of these diets (Experiment 2)*
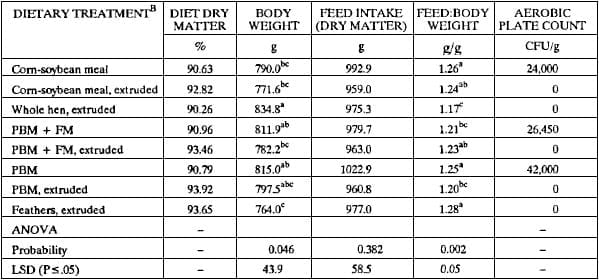
*Body weight, feed intake, and feed:bodyweight represent means of 4 replicates of battery pens with 10 chicks/pen.
bPBM= Poultry by-product meal; FM= Feather meal; Feather = Ground feather from spent hens; LSD = Least significant difference.
a-c Means within the same column with no common superscript differ significantly (P ≤.05).
In Experiment 1, diets containing dead broilers supported higher (P c .05) body weight than those receiving the corn-soybean meal control diet. The treated feathers diet improved growth rate but not feed conversion. In Experiment 2, dead poultry and treated feathers extruded products resulted in feed efficiency and growth responses comparable to the corn-soybean meal control diet (Table 4).
Tadtiyanant et al. [2] co-extruded either eggshells, hatchery waste, or turkey deboning residue with corn. They reported that the resulting ingredients were sterile and that incorporating them into the laying hens' diet caused no significant differences (P > .05) in egg production, egg weight, feed conversion, egg specific gravity, or Haugh units compared to the control diet (Table 5).
Table 4. Effects of extruded dead poultry and feathers on broiler body weight and feed conversión (Experiments 1 and 2)A
a Means of 4 pens of 10 chicks/pen
b Feed intake: body weight
c Extruded with 75 % soybean meal (45% CP) with 25% mortalities or feathers (wet basis)
d Feathers grounds prior to extrudinge Treated by proteolytic enzyme premix (2.5%, wet basis). Enzyma Premyx No. 1955 provided by Insta-Pro International, Des Moines, IA.
a-d Means within the same column no common superscript differ significantly (p ≤.05).
Table 5. Effects of extruded eggshells, hatchery waste, and turkey deboning residue on laying hen performance (Experiments 3 and 4)A
aMeans of 6 group of cages; 30 laying hens/group.
bGround corn and centrifuged eggshells in a 25:75 ratio (wet basis).
cGround corn and centrifuged hatchery solids in a 40:60 ratio (wet basis).
a,bMeans withn the same column with no common superscript differ significantly (P ≤.05).
The microbiological test (total aerobic count) for both the broiler and layer feeding trials indicated that the pre-extrusion blended mixtures had significant numbers of CFU/g of sample. The extruded products, however, were free of aerobic microorganisms (Table 6). Tadtiyanant et al. concluded that high temperature-short time extrusion is a feasible disposal method for converting these poultry industry residuals into high quality feedstuffs.
Table 6. Aerobic plate counts of dead poultry, feathers, eggshells, hatchery waste, and deboning residual mixtures before and after extruding
aMixtures d75% soybean meal (48% CP) and 25% dead birds or feathers (wet basis). %rested by roteolytic enzyme premix (2.5% wet basis).
bTreated by proteolityc Enzyme Premix No. 1955 provided by Insta-Pro Internationa1,bes Moines, IA.
cGround corn and centrifuged eggshells in a 2575 ratio (wet basis).
dGround corn and centrifuged hatcherysolids in a 40:60 ratio (wet basis).
eGround corn, centrifuged hatchery solids, and liquid in a 65:19.6:15.4 ratio (wet basis).
fGround corn and mechanically deboned residue in a 73.2:26.8 ratio (wet basis).
Froning and Bergquist [3] fed extruded eggshells and technical egg white to a commercial flock of laying hens. They reported that the rate of lay was significantly higher (P < .05) for those birds receiving the extruded product compared to the control group (Table 7). No differences in mortality, feed conversion, breaking strength, or shell thickness were found. They concluded that extrusion technology may provide an avenue for better utilization of eggshells as well as other waste from egg processing plants.
Table 7. Effect of feeding extruded eggshells on Shell quality, rate of lay, feed conversión, and mortality.
aBreking strength and shell thickness were measured on 2 replicates of 30 eggs each (a total 60 eggs/treatment).
bWeekly averages were taken over a 12-wk period.
a,bValue within the same column with no common superscript differ significantly (P ≤.05).
Patterson et al. [4] extruded a blend of offal and condemned buds with inexpensive ingredients such as wheat middlings, barley, cassava. The resulting new ingredients were incorporated into broiler diets at 5, 10, and 20% and performance compared with a cornsoybean meal control diet. They reported (Table 8) that all extruded products except the 20% barleyby-product blend resulted in equal broiler performance at a lower cost than that of the control diet.They also reported that ensiling poultry by-products was a viable method of preservation before extrusion.
Table 8. Final body weight and overall feed conversion of broilers raised to 3 wk of age (Experiment 1).
aDietary treatments: CS-10,10% cassava extruded with fresh poult by-product; CS-20,20% cassava extruded with fresh poultry by-product; WM-5, 5% wheat middlings extruded wit7 fresh poultry b -product; WM-IO, 10% wheat middlings extruded with fresh poultry by-product; B-10, 10% barley extruded with IresKpoultry by-producl; B-20,20% barley extruded with fresh poultry by-product.
abMeans within the same column with no common superscript differ significantly (P e .OS).
Blake et al. [5] investigated the feasibility of extruding turkey processing plant offal and farm mortalities. When those by-products were co-extruded with soybean meal, the nutrient composition of the resulting product compared favorably to that of soybean meal (Table 9). Furthermore, they presented the results of a digestibility trial and a complete analysis of one of the resulting ingredients (30/70 turkey mortalityhoybean meal) (Table 10). This information was used in formulating diets for a turkey feeding trial. The results of this trial indicate that the substitution of up to 100% extruded turkey meal for soybean meal had no effect on growth performance and feed efficiency (Figure 1). Similar results were obtained when extruded turkey meal replaced soybean meal in a broiler trial (Figure 2).
Table 9. Nutrient composition of extruded by-product meals.
aComposed of condemned parts, heads, feet, viscera, and bone residue.
bComposed of 68.6% offal, 25.5% feathers, and 6.2% blood.
Table 10. Nutrient composition and digestibility of amino acids in extruded turkey meal (30% farm mortalities and 70% soybean meal) on a drv matter basis.
Figure 1. Body weig ht and feed efficiency of 18-wk-old Large White male turkeys fed varying levels of extruded turkey meal.
Figure 2. Body weight and feed efficiency of broilers fed varying levels of extruded turkey meal to 5 wk of age.
Lyons and Vandepopuliere [6] processed round spent hens alone or in combination with wheat middlings in a fluidized bed dryer followed by steeping or extrusion. All heat treatments supported equal or better broiler performance to 21 days of age (Table 11). steeping resulted in a marked reduction in aerobic plate colonies, coliform, yeast, and mold. Extrusion of spent hens and wheat middling product, however, achieved the greatest reduction of aerobic plate colonies :Table 12).
Table 11.Broiler performance when fed diets containing ground spent hens processed whith and without wheat middlings (Experiment 1)A
aDiet fed from day 1 to day 21.
bStandard error of the mean.
cSH= Spent hens ground and formed in a Pellet Pro, heated and dried in a Jet-pro, and steeped;SH-WM=Spent hens ground with wheat middlings at a 1:1 ratio on a dry matter basis and treated as SH above; SH-wm-E = SH-wm partially dried, extruded, and air dried, but not steeped.
a-bMeans within a column with no common superscript differ significantly (P ≤.05).
Table 12. Microbiological assay results of ground spent hens processed with and without wheat middlings.
aAssays conducted by University of Missouri Veterinary Medical Diagnostic Laboratory, Columbia; MO.
bAssays conducted by ConAgra Frozen Food Co., Columbia Analytical Laboratory; Columbia; MO.
cSpenthens processed through a Weiler and Co., Whitewater, WI Model 6 grinder equipped with ¼* hole orifice plate.
dSalmonella serogroup B.
eProcessed through Jet-Pro procedure, Atchinson, KS, with an inlet air temperature of 360ºF and exit product temperatude of 190ºF.
fThe dried product was steeped in an insulated chamber at 230ºF for 30 min.
gMixed to provide an approximate 1:1 ratio of ground whole hen and wheat middlings on a dry matter basis.
hSH= Spent hens ground and formed in a Pellet Pro, heated and dried in a Jet-Pro, and steeped;SH-WM = Spent hens ground with wheat middlings at a 1:1 ratio on a dry matter basis and treated as SH above; SH-WM-NSSH-WM without being steeped; SH-WM-E = SH-WM partially dried, extruded, and air dried, but not steeped.
jThe blend was dried to approximately 25 % moisture using the Jet-Pro procedure and then extruded through an Insta-Pro Extruder (Triple “F”, Inc., Des Moines, IA) and spread on cardboard to air dry for 72 hr.
The microbiological quality of extruded by-products
Because of the nature and conditions of the starting material (mortalities), the question arises: Is it safe to feed dead bird meal to poultry?" Reynolds [7] conducted studies to answer this question.
A preparation of avian infectious disease agents containing Salmonella typhimurium, coccidia (Eimeria tenella), turkey rotavirus, turkey astrovirus, and Streptococcus faecium was added to the pre-extruded material. After extrusion, the mortality meal was tested for microorganisms (Table 13). Furthermore, feeding trials were conducted with turkey poults. At necropsy, there were no visible signs of lesions of disease. Salmonella cultures were negative, and no viruses were isolated from the intestinal tract. Reynolds [T1] concluded that extruded products in feed posed no risk of transmitting infectious agents.
Table 13. Microbiological evaluation of extruded turkey meal.
aBA = Blood agar, MA = MacConkey´s agar, SC = Salmonella culture; S-B = Slanetz-Bartley agar; THIO = Thioglycolate tubes; NB = Nutrient broth; SD = Sabouraud dextrose agar.
Other by-products that have been extruded and tested include feathers and offal, turkey litter, broiler litter, partially dehydrated layer manure, farm mortalities, dissolved air flotation, restaurant grease, fish waste, eggshells and unsalable eggs, cheese trimmings, tallow, and other food industry by-products.
Commercial extrusion operations are being installed in the United States and the rest of the world to pursue the idea of upgrading and complimenting conventional rendering. Such operations seek to consistently produce ingredients of the highest quality with regard to both nutrition and microbiological safety.
Determining feasibility by-product extrusion
To determine the economic feasibility of constructing an extrusion plant for its by-products, a poultry producer or prospect must first identify the volume of by-product of concern and its current value (negative, positive, or zero). The moisture content and nutritional profile of the by-product, and the intended use of the finished extruded product, will determine what dry ingredient can provide optimal results when co-extended with the by-product. The value of the proposed extruded product can then be determined through least cost formulation using the prospect’s specification for a given species, ingredient prices, and all variables associated with the process including labor, electricity, depreciation, etc. These factors in turn will determine the size of the extrusion plant and Will make it possible to calculate the approximate cost of recovery. The difference between the value of the final product and the cost of recovery and processing, compared to the current value of the raw by-product, will determine the feasibility of the project.
Conclusions and applications
1. By-product processing through dry extrusion has been developed, studied, and implemented. It provides an environmentally and nutritionally sound alternative to the outdated disposal methods of landfill dumping, burial, and incineration.
2. The process does not replace conventional rendering but rather complements it to consistently produce high-quality, microbiologically safe feed ingredients.
References and notes
1. Haque, A.K.M.A., J.J. Lyons, and J.M. Vandepopuliert, 1991. Extrusion processing of broiler starter diets containing &round whole h e n s , r l t r y byproduct meal, orground eathers. Poultry Sci. 0 234-240.
2. Tadllyanant, C., J.J. Lyons, and J.M. Vandepopuliere, 1993. Extrusion processing used to convert dead poultry, feathers, eggshells, hatcherywaste, and mechanically debonded residue into feedstuffs for poultry. Poultry Sci. m151.5-1527.
3. Froning, G.W. and D. Bergquist, 1990. Research note: Utilization of inedible eggshells and technical egg white using extrusion technology. Poultry Sci. 692051- 2053.
4. Palterson, P.H., N. hac, and W.C. Coleman, 1994. Feeding value of poultry by-products extruded with cassava, barley, and wheat middlings for broiler chicks: 2. The effect of ensiling poultry b products as a presemtion method prior to extrusion.L ul t ry~ci7.3 :1107-1115.
5. Blake, J.P., M.E Cook, and D. Reynolds, 1991. Fktruding poultry farm mortalities. Pages 1-6 in: Proc. Amer. SOC. of Agric. Eng., Intl. Summer Meeting, Albuquerque, NM.
6. Lyons, JJ. and J.M. Vandepopuliere, 1996. S nt hens converted into a feedstuff. J. Appl. Poultry ces.
7. Reynolds, D., 1990. Microbiological evaluation of dead bird meal. Presented at the Midwest Poultry Federation Education Program, Minneapolis, MN.